Metal Sand Casting Process A Comprehensive Overview
The metal sand casting process is a widely used manufacturing technique that plays a crucial role in various industries, including automotive, aerospace, and machinery. This method is appreciated for its versatility, ability to produce complex shapes, and cost-effectiveness, making it a preferred choice for both small and large-scale production.
Understanding Sand Casting
At its core, sand casting involves creating a mold from a sand mixture to hold molten metal in order to shape it as it cools and solidifies. The process begins with the preparation of the sand, typically composed of silica, clay, and water, which gives it the ability to retain shape when compacted. The first step is to create a pattern, usually made of metal or wood, which is a replica of the final product. This pattern is placed in the sand to form an impression that will become the mold.
The Molding Process
Once the pattern is created, it is placed into a mold box, and the sand mixture is poured around it. The sand is compacted firmly to ensure it retains the shape of the pattern. After the sand has sufficiently hardened, the mold is carefully separated, and the pattern is removed, leaving a hollow cavity in the shape of the desired part. This process can be repeated to create multiple molds, depending on production needs.
Pouring the Metal
With the mold prepared and the pattern removed, the next step is to pour molten metal into the cavity. The type of metal used can vary significantly depending on the application's requirements. Common metals used in sand casting include aluminum, iron, and bronze. The metal must be heated to its melting point and then carefully poured into the mold, ensuring that it fills all voids without introducing contaminants or air pockets, which could lead to defects in the final product.
metal sand casting process
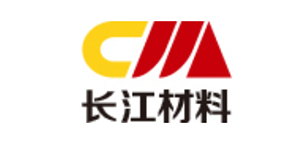
Cooling and Finishing
After the metal is poured, it is left to cool and solidify, which can take several minutes to hours, depending on the size and type of metal. Once cooled, the sand mold is broken away, revealing the metal casting. The casting often requires additional finishing processes, such as trimming excess metal (known as flash), machining for precise dimensions, and surface treatments to enhance appearance and durability.
Advantages of Sand Casting
One of the most significant advantages of sand casting is its adaptability to various metal types and the ability to produce complex shapes that might be challenging with other methods. This process can accommodate large items with intricate geometries, making it ideal for producing components such as engine blocks, machinery parts, and art sculptures. Additionally, since the materials for sand casting are relatively inexpensive, it offers a cost-effective solution for both prototyping and production runs.
Challenges and Innovations
Despite its benefits, the sand casting process does have its challenges. Sand can lead to defects like sand inclusions or surface finish imperfections. Moreover, achieving tight tolerances can be difficult. However, with advancements in technology, many challenges are being addressed. The introduction of computer-aided design (CAD) and computer-aided manufacturing (CAM) systems has improved pattern design and mold precision. Furthermore, the use of 3D printing technology to create sand molds is revolutionizing the industry by allowing for more intricate designs and quicker turnaround times.
Conclusion
In summary, the metal sand casting process is an essential manufacturing technique that combines traditional practices with modern advancements. Its ability to produce complex shapes with diverse materials makes it invaluable in many sectors. As technology continues to evolve, the efficiency, precision, and quality of sand casting will likely see further improvement, ensuring its relevance in the future of manufacturing. Whether used for small components or large-scale productions, sand casting remains a cornerstone of metal fabrication and innovation.
Post time:11월 . 20, 2024 07:17
Next:Traitement de ponçage pour impression 3D