Lost Foam Metal Casting An Overview
Lost foam metal casting is an innovative manufacturing process that combines the advantages of traditional casting with the efficiency of modern techniques. This method, which emerged in the 1970s, allows for the creation of complex shapes and high-quality metal parts, making it a popular choice in industries such as automotive, aerospace, and engineering.
The Process
The lost foam casting process begins with the creation of a foam pattern, typically made from expanded polystyrene (EPS). This foam pattern is designed to match the exact dimensions and shape of the final metal part. The foam is then coated with a refractory material, such as a ceramic shell or sand, which acts as a mold. This coating not only provides structural support to the pattern but also aids in the prevention of defects in the final cast.
Once the coating is applied and has hardened, the foam pattern is subjected to heat. The heat causes the foam to vaporize, leaving a cavity that retains the shape of the original pattern. This is a key feature of the lost foam process, as it eliminates the need for a traditional mold, thus reducing materials and energy costs.
After the foam is vaporized, molten metal is poured directly into the cavity. The metal fills the space left by the foam and solidifies, forming the final cast part. The simplicity of this method allows for intricate designs to be created with minimal tooling, resulting in less waste and a more environmentally friendly approach to metal casting.
Advantages
One of the most significant advantages of lost foam metal casting is its ability to produce complex shapes with high dimensional accuracy. Since the foam pattern can be easily molded into intricate designs, manufacturers can create parts that would be challenging or even impossible to achieve with conventional casting methods. This capability is particularly beneficial in sectors where lightweight and highly detailed components are essential, such as in aerospace applications.
lost foam metal casting
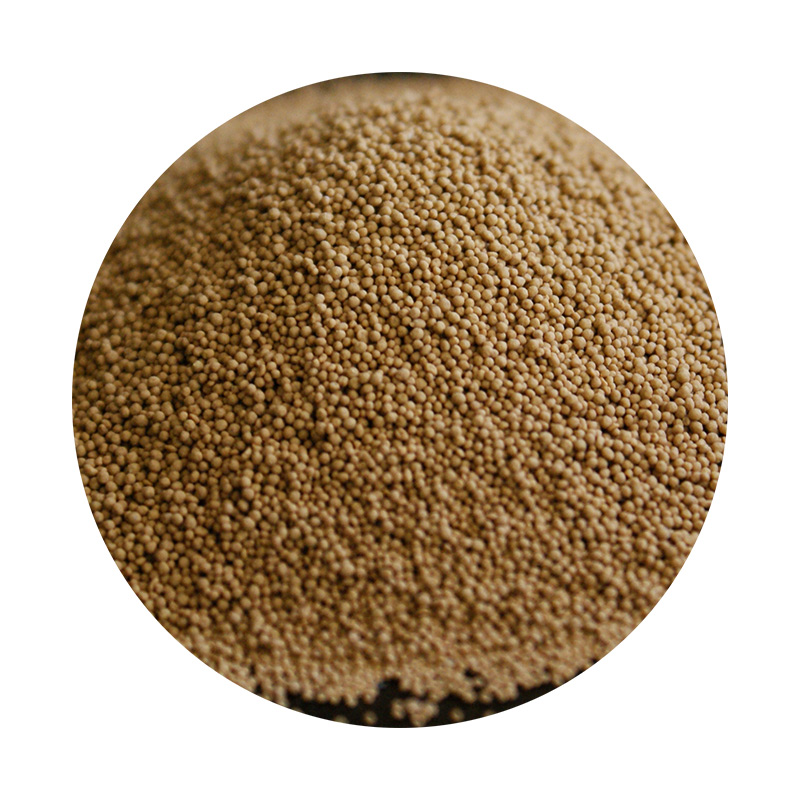
Furthermore, the lost foam process reduces the amount of secondary machining required on parts. Because the foam fills the mold completely, the final product often requires less finishing work, saving both time and costs. The reduced need for additional machining also leads to improved material utilization, resulting in less scrap and waste.
Another notable advantage is the cycle time. The lost foam method typically provides quicker turnaround times compared to traditional sand casting. This efficiency can help manufacturers meet tight production schedules without sacrificing quality.
Challenges
Despite its many benefits, lost foam metal casting is not without its challenges. The initial setup, including the creation of foam patterns and molds, can be costly. Additionally, controlling the heating and pouring processes requires a high level of precision to avoid defects such as inclusions or misruns, which can affect the integrity of the final product.
The material selection is also crucial. While aluminum is commonly used for lost foam casting, other metals may not perform as reliably in this process. As such, careful consideration of the metal's properties and its compatibility with the foam pattern is necessary.
Conclusion
Lost foam metal casting represents a significant advancement in the field of manufacturing, providing a versatile and efficient method for producing complex metal parts. Its ability to create high-quality components with reduced waste and quicker turnaround times establishes it as a valuable option in various industries. While challenges remain, ongoing advancements in technology and materials promise to enhance the effectiveness of lost foam casting, potentially expanding its applications and benefits in the future. As industries continue to seek innovative solutions, lost foam metal casting is poised to play an integral role in shaping the future of metal manufacturing.
Post time:11월 . 11, 2024 06:40
Next:sand casting stainless steel