How to Make Foundry Sand
Foundry sand plays a crucial role in the metal casting industry, offering a core material that ensures the formation of high-quality molds and cores. Its unique properties allow for excellent heat resistance, minimal thermal expansion, and a reusable nature, which makes it a sustainable choice for foundries. If you’re curious about how to make your own foundry sand, this guide will walk you through the steps, materials, and considerations needed to create an effective product.
Understanding Foundry Sand
Before diving into the making of foundry sand, it's essential to understand its composition. Foundry sand is primarily made from silica sand, which is known for its fine grain and ability to withstand high temperatures. In addition to silica, the sand may include additives that enhance its binding properties, strength, and ability to retain shape during the casting process.
Materials Needed
To make foundry sand, you will need the following materials
1. Silica Sand This is the primary ingredient. High-quality silica sand that is fine and sharp-edged is preferred. Avoid sand that contains clay or impurities.
2. Clay Commonly used clay types include bentonite. This acts as a binder and helps the sand hold its shape.
3. Water Though not always necessary, water can help in mixing the sand and clay to achieve the desired moisture content.
4. Additives Depending on your specific requirements, you may consider adding other materials, such as resins or ceramic dust, to improve the properties of the foundry sand.
how to make foundry sand
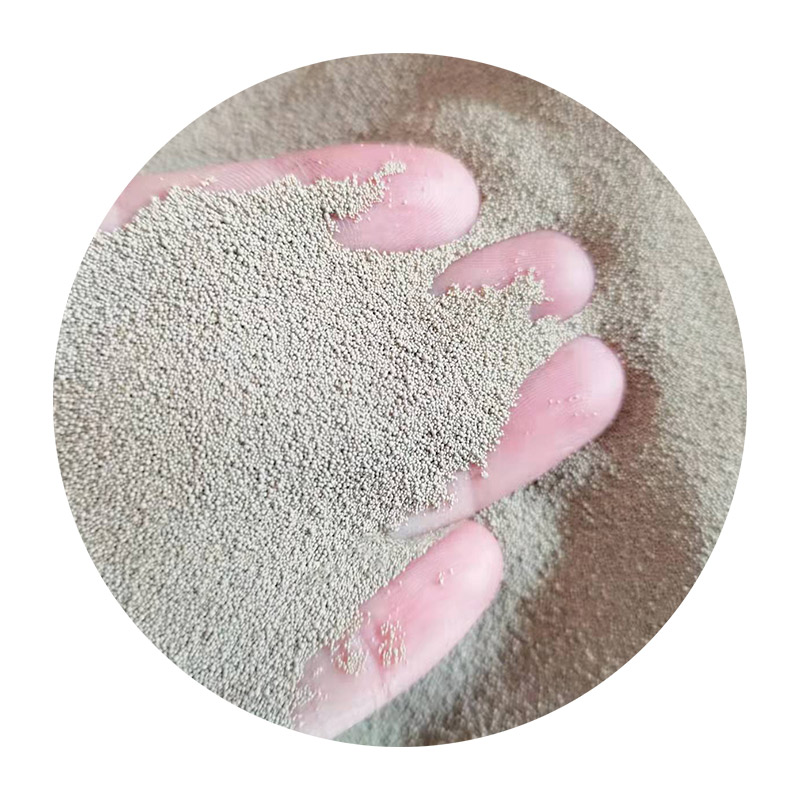
Steps to Make Foundry Sand
1. Gather Raw Materials Start by sourcing high-quality silica sand and bentonite clay. It's important to ensure that the silica is as free from impurities as possible to maintain the integrity of your molds.
2. Processing the Sand The silica sand may need to be screened to remove larger particles and debris. This ensures a uniform grain size, which is crucial for the sand's performance in casting.
3. Mixing the Clay For every 100 pounds (about 45 kg) of sand, you will typically need 5 to 10 pounds (about 2.5 to 4.5 kg) of bentonite clay. The exact ratio may depend on the specific requirements of your casting process and the type of mold you are creating.
4. Combining the Materials In a mixing container, gradually combine the silica sand and bentonite clay. Ensure that the clay is evenly distributed throughout the sand. This can be done using a mechanical mixer or by hand, depending on the quantity of sand you are producing.
5. Adding Water If the mixture appears too dry, you can slowly add water while continuing to mix. The goal is to achieve a consistency where the sand can form clumps without being overly wet. About 4 to 5% moisture is usually sufficient.
6. Testing the Mixture Before using the foundry sand for production, test its properties. Check for the strength of the molds and the ability of the sand to retain shape when pressure is applied. Adjust the moisture content or the clay ratio as needed.
7. Storing the Foundry Sand Once prepared, store your foundry sand in a cool, dry place to prevent clumping or moisture absorption. Proper storage ensures that the sand remains usable for extended periods.
Conclusion
Making your own foundry sand can be a rewarding process, allowing for customization to meet the specific needs of your metal casting projects. By understanding the materials and following the correct mixing procedures, you can produce high-quality foundry sand that will enhance your casting results. Whether you are a hobbyist or a professional in the metallurgical field, mastering the art of foundry sand production is an invaluable skill set that can lead to improved efficiency and quality in your casting operations. Happy casting!
Post time:11월 . 24, 2024 22:12
Next:Beneath the Radiant Dunes of Shimmering Sands