How Does Sand Casting Work?
Sand casting is one of the oldest forms of metal casting, a process that involves pouring molten metal into a sand mold to create a specific shape. It has been used for centuries and remains a popular technique in both industrial and artistic applications. This article will explore the fundamentals of sand casting, its processes, advantages, and applications in modern manufacturing.
The Basics of Sand Casting
The sand casting process begins with creating a mold, which consists of two main parts the cope (the top half) and the drag (the bottom half). The mold is made from a mixture of sand, clay, and water. The sand provides the structure, while the clay acts as a binding agent, helping to hold the mold together when the molten metal is poured in. This mixture is typically compacted around a pattern—a replica of the object to be cast.
After the pattern is placed into the sand mixture, it is removed to leave a cavity in the shape of the desired part. This cavity is then prepared for pouring by ensuring that it is clean and free of any debris. Once the mold is ready, it is assembled, and additional features such as risers or gates may be added to facilitate the flow of the molten metal and compensate for any shrinkage that occurs as the metal cools.
Pouring the Metal
With the mold prepared, the next step is to melt the chosen metal, which can range from aluminum, iron, bronze, or others according to the final product's requirements. The molten metal must be heated to the appropriate temperature, ensuring it is in a liquid state and can fill the mold uniformly.
Once the metal reaches the desired temperature, it is poured into the mold through the gate system. This step requires precision, as any turbulence or rapid cooling can lead to defects in the final product. The casting is left to cool, during which time the metal solidifies and takes the shape of the mold.
Removing the Casting from the Mold
After the metal has cooled and solidified, the next step is to remove the casting from the mold. This is done carefully to avoid damaging the newly formed part. The sand mold is typically broken apart, and the casting is then cleaned to remove any residual sand or impurities.
how does sand casting work
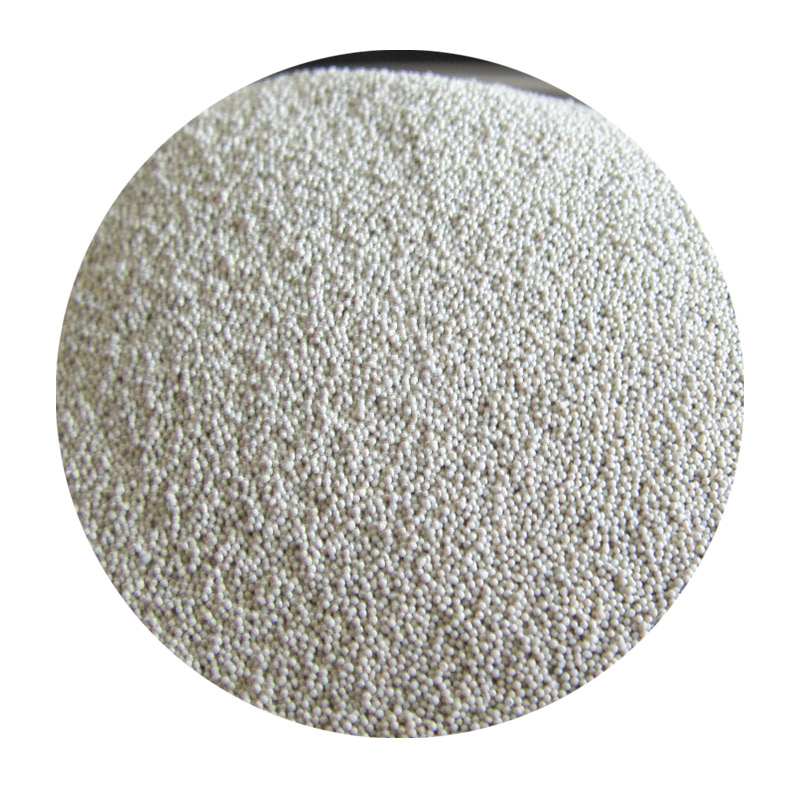
Depending on the complexity of the design, additional machining may be necessary to achieve the precise dimensions and surface finish demanded by the application. This can include grinding, milling, or polishing the casting.
Advantages of Sand Casting
Sand casting offers numerous advantages, making it a favored method in various industries. One of the most significant benefits is its versatility; it can produce a wide range of sizes, from small components to large industrial parts, with varying levels of complexity.
Another advantage is cost-effectiveness. The materials used in sand casting, primarily sand, are readily available and inexpensive. Additionally, the ability to reuse sand after the mold is broken reduces material waste and costs.
The process also allows for intricate designs and the incorporation of cores for hollow components, expanding the possibilities for design. Furthermore, sand casting can accommodate various metals, further enhancing its applicability across different industries.
Applications of Sand Casting
Sand casting finds applications in numerous sectors, from automotive to aerospace and artistic production. In the automotive industry, it is commonly used to create engine blocks, housings, and various small components. In the aerospace sector, the precision and lightweight nature of aluminum castings produced through sand casting are particularly valuable.
Artisans and sculptors also use sand casting for producing sculptures and decorative objects, showcasing the process's creative potential. Whether for mass production or unique artistic works, sand casting remains a fundamental method of metal processing.
Conclusion
In summary, sand casting is a dynamic and adaptable method used for creating metal components. Its blend of traditional techniques and contemporary applications demonstrates its enduring relevance in modern manufacturing. As industries evolve and demand for precision components increases, sand casting will continue to be a key player in meeting these challenges while upholding its rich historical significance.
Post time:10월 . 12, 2024 16:12
Next:Exploring the Benefits and Techniques of Metal Sand Casting in Modern Manufacturing