Understanding Foundry Sand Types A Comprehensive Overview
Foundry sand is a crucial material in the metal casting process, serving as a mold for various metal components. The right type of sand can significantly influence the quality of the final cast product. Foundry sands come in various types, each with unique properties that make them suitable for specific applications. This article explores the primary types of foundry sands, their characteristics, and their applications in the casting industry.
1. Silica Sand
Silica sand, or quartz sand, is the most commonly used type of sand in foundries. It is composed primarily of silicon dioxide (SiO2) and possesses high heat resistance, making it well-suited for metal casting processes. The primary advantage of silica sand is its availability and low cost. It is used extensively in both ferrous and non-ferrous metal casting.
Silica sand has different grades based on particle size and shape, which can affect mold properties. Smaller grain sizes provide better surface finishes for the cast metal but may lead to higher pressure due to mold thermal expansion. Conversely, coarser sands are more forgiving regarding thermal stress but can result in rougher surface finishes.
2. Resin-Coated Sands
Resin-coated sands are a newer development in foundry materials, combining traditional sand with a thermosetting resin. This mixture is usually applied to silica sand grains, enhancing the sand's properties. Resin-coated sands offer excellent dimensional accuracy, surface finish, and overall strength, making them suitable for high-quality casting applications.
One significant advantage of resin-coated sands is their ability to be reused multiple times, reducing material costs and waste. They are commonly used in the production of complex cores and molds in industries requiring high precision, such as automotive and aerospace sectors.
foundry sand types
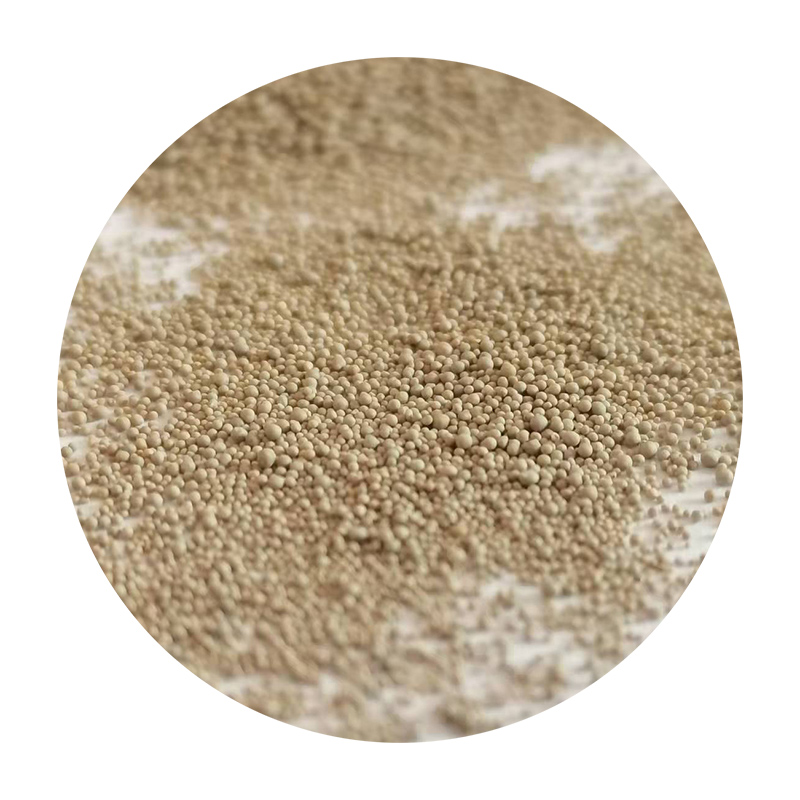
Clay-based sands contain a significant proportion of clay, which acts as a binder to hold sand grains together. The most commonly used clay in foundries is bentonite due to its excellent binding characteristics. Clay sands provide good mold strength and are relatively inexpensive.
These sands are typically used in a process known as green sand casting, where the mold is created from a mixture of sand, clay, and water. The flexibility of clay-based sands allows for the creation of complex shapes, but they can suffer from poor surface finishes compared to resin-coated options. Additionally, they may require careful management of moisture content to maintain optimal mold properties.
4. Specialty Sands
In addition to the standard types of sands, several specialty sands cater to specific casting needs
- Chromite Sand This type of sand contains chromium oxide and is known for its high thermal stability and resistance to metal penetration. It is particularly valuable in high-temperature applications and is often used in the casting of steel and other ferrous alloys.
- Zircon Sand With high melting points and low thermal expansion, zircon sand is often used in applications requiring high precision and excellent surface finishes, such as in the aerospace and marine industries.
- Olivine Sand This natural sand is known for its ability to withstand high temperatures without warping. Olivine sand is less commonly used than silica but is appreciated for its unique properties, making it ideal for specific foundry applications.
Conclusion
Understanding the different types of foundry sands is essential for selecting the right material for specific casting applications. Each type, from silica to specialty sands, offers unique advantages and disadvantages that can affect both the casting process and the quality of the final product. As technology and materials science evolve, the use of foundry sands will continue to adapt, providing new solutions to meet the demands of modern manufacturing. For engineers and foundry professionals, staying informed about these materials' latest trends and innovations is vital for improving efficiency and product quality in the competitive casting industry.
Post time:12월 . 15, 2024 04:56
Next:resin coated sand uses