Understanding Foundry Sand Composition A Key to Successful Casting
Foundry sand is an essential material in the metal casting industry, serving as a mold-making agent that shapes the final product. The composition of foundry sand plays a critical role in determining the quality and efficiency of the casting process. In this article, we will explore the various components of foundry sand, their significance, and the impact they have on casting performance.
1. Basic Composition of Foundry Sand
At its core, foundry sand is primarily composed of a granular material, typically silica sand. Silica, or silicon dioxide (SiO2), is favored for its high melting point and thermal stability. It is the dominant component, usually making up 85% to 95% of the sand mixture. The specific grain size, shape, and distribution of silica particles are crucial for creating molds that can withstand the thermal stresses of molten metal.
In addition to silica, foundry sand often contains clay, which acts as a binder, helping grains adhere to one another. Common types of clay used include bentonite, which is prized for its plasticity and ability to hold moisture. Clay content typically ranges from 3% to 10%, depending on the desired mold characteristics. The presence of clay enhances the strength and resilience of the mold, preventing cracking during metal pouring.
2. Additives and Their Functions
Beyond silica and clay, other additives, such as coal dust and chemical binders, may be mixed with foundry sand to improve its performance. Coal dust, or carbonaceous materials, is often used to enhance the surface finish of castings. Additionally, chemical binders, like phenolic resins, can provide excellent strength and thermal properties, producing molds that are suitable for high-temperature applications.
foundry sand composition
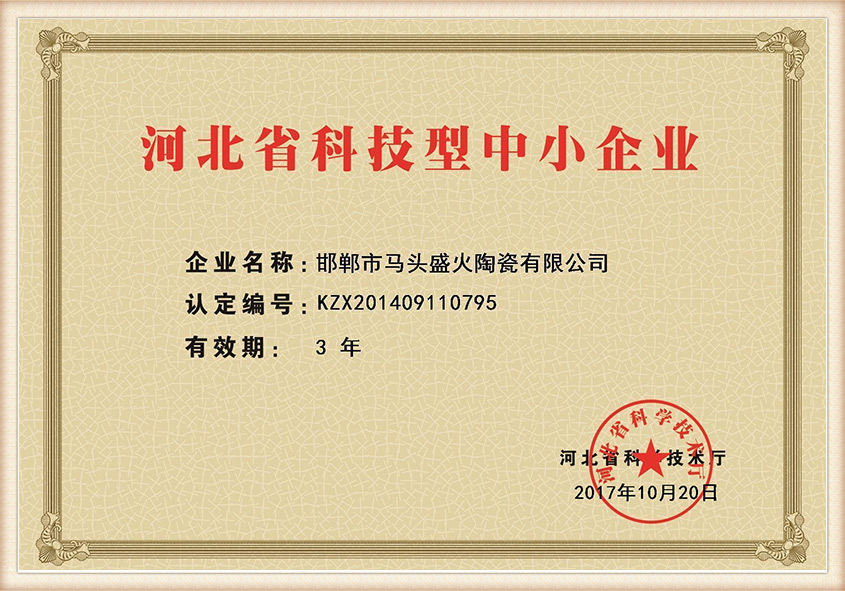
The choice of additives depends on the specific requirements of the casting process, as well as the type of metal being cast. For instance, ferrous alloys might require different sand characteristics than non-ferrous materials. This adaptability highlights the importance of formulating the right sand composition for each application.
3. Reusability and Environmental Considerations
One of the advantages of foundry sand is its reusability. After a casting process, spent sand can often be reclaimed and reprocessed for further use. This not only reduces material waste but also minimizes the environmental impact of sand mining. Reclamation methods typically involve vibrating screens, air classifiers, and thermal processes to remove contaminants and regenerate the sand to its original quality.
However, the management of foundry sand disposal is crucial, as the sand may contain residues of metals and other substances that could be harmful if not handled properly. Foundry operators must ensure compliance with environmental regulations related to hazardous waste.
4. Conclusion The Importance of Sand Composition in Casting
Ultimately, the composition of foundry sand is integral to the metal casting process. The right balance of silica, clay, and additives ensures that molds can withstand high temperatures, provide suitable surface finishes, and support the overall efficiency of the casting operation. As the industry evolves, ongoing research into advanced materials and recycling techniques will continue to enhance foundry sand performance.
In conclusion, understanding and optimizing foundry sand composition is not only vital for achieving high-quality castings but also plays a significant role in advancing sustainable practices in the foundry industry. As manufacturers strive for more innovative and ecologically sound production methods, the importance of suitable sand composition will undoubtedly remain a focal point in the quest for excellence in metal casting.
Post time:11월 . 17, 2024 13:36
Next:bauxite frac sand