Foundry Molding Sand Essential Material in Metal Casting
Foundry molding sand, a critical component in the metal casting process, plays an indispensable role in the manufacturing industry. As the backbone of foundries, it provides the necessary characteristics for forming molds that ensure the production of high-quality metal castings. Understanding its composition, types, and applications can greatly enhance the efficiency and effectiveness of casting operations.
Composition of Foundry Molding Sand
Foundry molding sand is primarily composed of silica sand, which serves as the main aggregate. The sand particles are spherical, which facilitates better flow and packing properties, ensuring the mold’s strength and stability. In addition to silica, other materials such as clay, water, and various additives are incorporated to tailor the sand's properties to specific casting requirements. Clay acts as a binding agent that helps the sand adhere together, while water serves to activate the clay and improve the mold's cohesiveness.
Types of Foundry Molding Sand
There are several types of molding sands, each with unique properties tailored to different casting processes
1. Green Sand This is the most commonly used molding sand, consisting of silica sand mixed with a small percentage of clay and water. Its adaptability and cost-effectiveness make it a popular choice among foundries. Green sand molds are notable for their ability to retain heat, allowing for uniform metal cooling.
2. Dry Sand Unlike green sand, dry sand is moisture-free, providing excellent dimensional accuracy, making it suitable for precision castings. Dry sand molds are typically cured by heating, which hardens the mold and increases its strength.
3. Sodium Silicate Sand This type uses sodium silicate as a binder and is activated by carbon dioxide gas. The resulting molds boast high strength and can withstand the thermal stresses during metal pouring. Sodium silicate sand is often used in high-temperature applications.
foundry molding sand
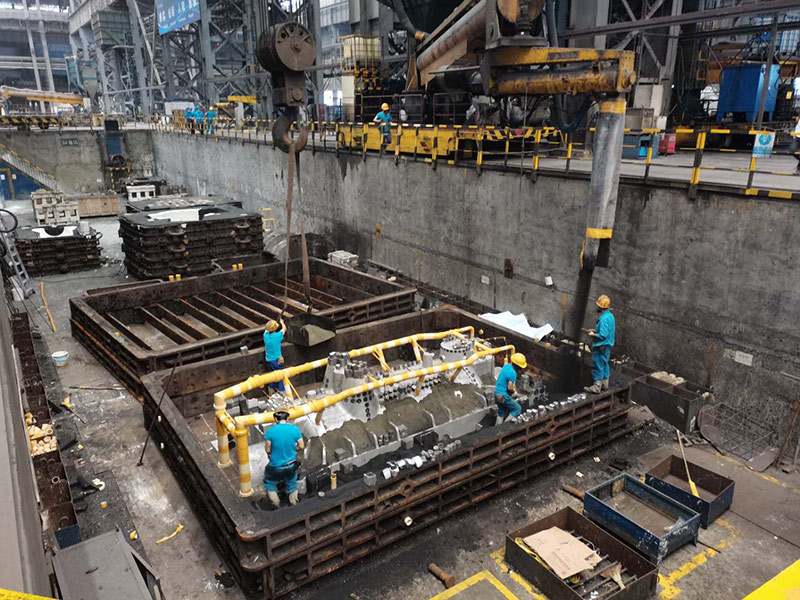
4. Resin-Bonded Sand This variant uses synthetic resins as bonding agents. It offers superior mold strength and allows for finer details in castings. Resin-bonded sands are often used for complex shapes and intricate designs, where high precision is required.
Applications of Foundry Molding Sand
The applications of foundry molding sand are extensive, spanning various industries including automotive, aerospace, and machinery. The ability of molding sand to produce intricate designs and withstand high temperatures makes it ideal for casting components such as engine blocks, turbine blades, and various machine parts.
In addition, molding sand is also instrumental in the production of prototypes and custom parts, which are vital for research and development in different sectors. The flexibility in adjusting sand properties enables foundries to cater to specific requirements, thereby enhancing production efficiency.
Environmental Considerations
With increasing regulatory scrutiny regarding environmental impacts, foundries are exploring sustainable practices related to molding sand usage. Efforts such as sand recycling and the use of eco-friendly binders are being implemented to minimize waste and reduce the carbon footprint associated with metal casting. Moreover, innovative technologies are being developed to ensure the sand can be reused multiple times without compromising mold quality.
Conclusion
In summary, foundry molding sand is a vital material in the casting industry, crucial for producing high-quality metal parts. Its versatility and ability to be tailored to various casting requirements underscore its importance. As the industry evolves, so too will the technologies and practices surrounding molding sand, paving the way for more sustainable and efficient metal casting processes. Understanding and leveraging the benefits of different types of molding sand will continue to be key to maintaining competitiveness in an ever-changing manufacturing landscape.
Post time:11월 . 07, 2024 10:51
Next:Innovative Ceramic Beads for Enhanced Durability and Performance in Various Applications