The Art and Science of Casting Sand An Exploration into Its Uses and Techniques
Casting sand, also known as sand casting or foundry sand, is a crucial process in metalworking that dates back thousands of years. This technique involves forming molds from sand to produce metal castings, a method known for its versatility, cost-effectiveness, and ability to create complex shapes. In this article, we explore the significance of casting sand, its composition, and various applications across industries, alongside the process itself.
The Composition of Casting Sand
Casting sand is primarily composed of silica, which is the main component contributing to its excellent flow characteristics and heat resistance. The quality of the sand affects the final product; therefore, it typically needs to have certain properties. A good casting sand should have high strength, stability, refractoriness, and the ability to retain shape.
The most commonly used type of sand in casting is silica sand, but other materials may be added to enhance performance. For example, clay is often mixed with sand to improve binding properties, resulting in a stronger mold. Other additives can include water, ammonium compounds, and organic materials that assist in achieving the desired mold characteristics.
The Sand Casting Process
The sand casting process generally involves several key steps, including pattern making, mold preparation, pouring the metal, and finishing the cast parts.
1. Pattern Making The first step involves creating a pattern, which is a replica of the object to be cast. Patterns can be made from various materials, including wood, metal, or plastic, and are crucial for controlling the dimensions and surface quality of the final product.
2. Mold Preparation Once the pattern is ready, it is placed in a mold box, and sand is packed around it. The sand mixture is typically compacted to create a strong mold. The pattern is then removed, leaving a hollow cavity that mirrors the shape of the object to be cast.
3. Pouring the Metal After the mold has been prepared and finalized, molten metal is poured into the cavity. This step requires precision, as the temperature and composition of the metal must be controlled to ensure proper filling of the mold.
casting sand
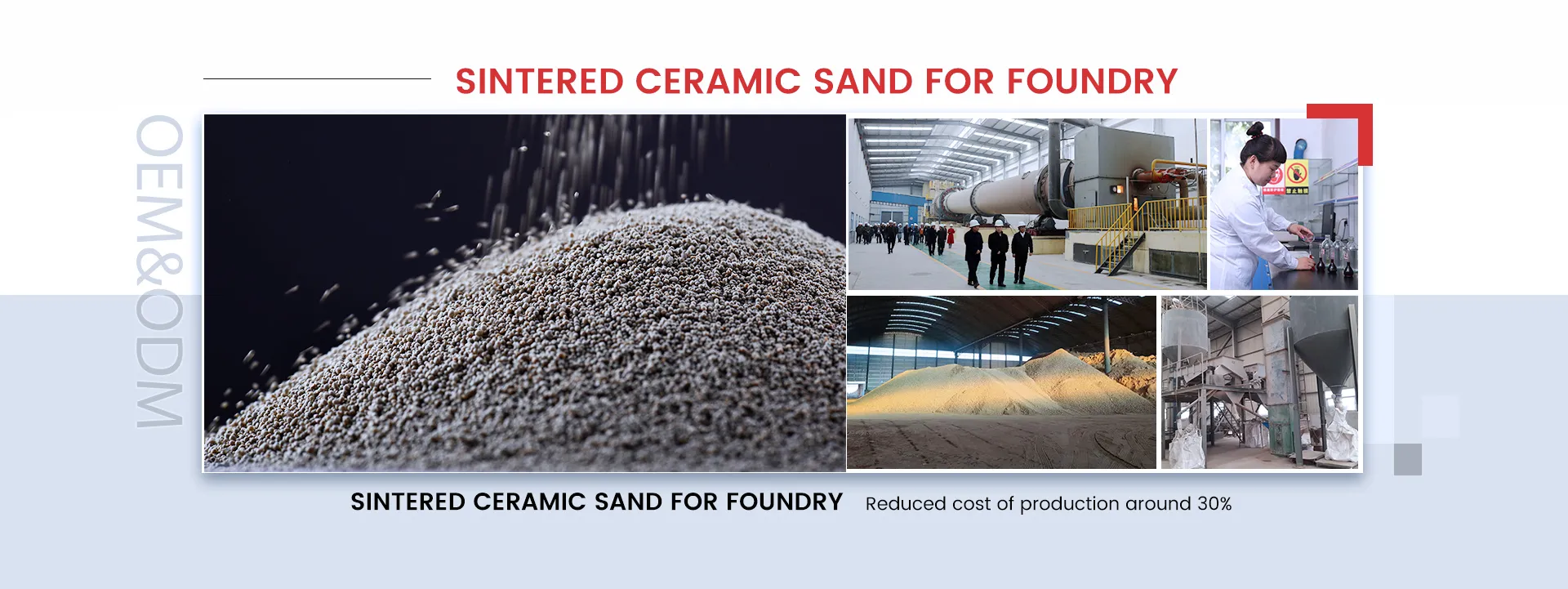
4. Cooling and Finishing Once the metal cools and solidifies, the mold is broken away to retrieve the cast item. The finishing process may involve grinding, sanding, or machining to achieve the desired surface finish and exact dimensions.
Applications of Casting Sand
Casting sand is used extensively across various industries due to its adaptability and effectiveness in producing complex and large-scale components.
1. Automotive Industry Many engine blocks, transmission cases, and other critical components are made using sand casting. The ability to produce intricate designs and strong parts makes it suitable for automotive applications.
2. Aerospace Lightweight and high-strength components are critical in aerospace engineering. Sand casting allows for the production of sophisticated shapes needed for aircraft parts, such as turbine housings and airframe components.
3. Art and Sculpture Beyond industrial applications, sand casting is also a beloved technique in the world of art. Artists create unique sculptures and artifacts via sand casting, taking advantage of the medium's flexibility in forming various shapes.
4. Construction In the construction industry, sand casting is used to produce architectural elements and tools. Its durability and versatility make it a go-to method for creating items like concrete molds and decorative facades.
Conclusion
Casting sand plays a vital role in manufacturing, art, and engineering, showcasing an incredible intersection of craftsmanship and technology. Its unique properties and the ability to produce detailed, robust components make it indispensable across various sectors. As industries continue to evolve with new materials and technologies, the traditional method of sand casting remains relevant, proving its timeless value in modern manufacturing. Whether for mass production or unique artistic expressions, the legacy of casting sand endures, solidifying its place in the rich tapestry of human innovation.
Post time:9월 . 28, 2024 17:02
Next:Exploring the Applications and Advantages of Sand Casting in Manufacturing Industries