3D Printing and Sand Casting The Innovative Fusion of Technologies
In the world of manufacturing, innovation has continually propelled the sector forward. Among the latest advancements are 3D printing and sand casting—two techniques that, when used in conjunction, can revolutionize the production process. This article examines how the integration of these technologies can enhance manufacturing efficiencies, reduce costs, and improve the overall quality of products.
Understanding 3D Printing and Sand Casting
To appreciate the synergy between 3D printing and sand casting, we first need to understand both processes individually. 3D printing, or additive manufacturing, involves creating objects layer by layer from a digital file. This technique allows for high precision and complexity in design, enabling manufacturers to produce intricate components that would be challenging or impossible to create using traditional subtractive methods.
On the other hand, sand casting is a metal casting process that uses sand as the mold material. It involves creating a mold by compacting sand around a pattern, which is then removed to leave a cavity for pouring molten metal. While sand casting has been a staple in manufacturing for centuries due to its low cost and ability to produce large-scale components, it has limitations regarding design complexity and lead times.
The Benefits of Combining 3D Printing with Sand Casting
1. Design Flexibility By using 3D printing to create mold patterns for sand casting, manufacturers can exploit the design flexibility offered by additive technology. Complex geometries, internal structures, and intricate cooling channels can be incorporated into designs without the limitations inherent in traditional mold-making.
2. Reduced Lead Times Traditional sand casting involves a lengthy process of mold making, which can take weeks or even months. However, with 3D printed patterns, manufacturers can drastically reduce lead times, going from design to production in a matter of days. This rapid prototyping capability enables quicker iterations and modifications, facilitating faster product development cycles.
3d printer sand casting
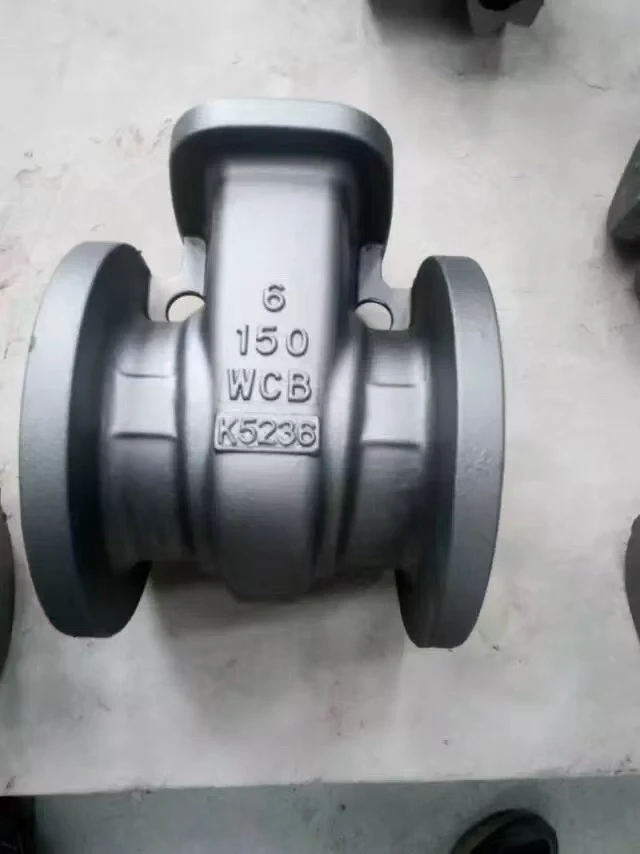
3. Cost Savings The use of 3D printing in the sand casting process can lead to significant cost savings in multiple ways. First, it eliminates the need for expensive, time-consuming mold-making processes. Second, the precision of 3D printed patterns reduces material waste during the casting process, ultimately lowering material costs. Additionally, the speed of production leads to reduced labor costs.
4. Enhanced Product Quality The accuracy that 3D printing delivers translates to better fitting and more consistent patterns. This precision results in higher-quality castings with fewer defects, leading to a reduction in rework and scrap rates. As a result, the final products are more reliable and meet the stringent quality standards demanded by industries such as aerospace, automotive, and healthcare.
5. Sustainability Sustainability is an increasingly important consideration in the manufacturing sector. By combining 3D printing with sand casting, manufacturers can minimize material waste and reduce energy consumption associated with traditional manufacturing methods. Furthermore, the ability to produce small batches of products on demand reduces the necessity for large inventories, supporting a more sustainable production model.
Challenges and Future Directions
Despite the many advantages of integrating 3D printing and sand casting, there are challenges to address. For instance, the materials used in 3D printing must be compatible with the sand casting process, and there may be a learning curve for manufacturers to fully adapt to this dual approach. Additionally, the initial investment in 3D printing technology can be substantial, although the long-term savings often justify the expense.
Looking forward, the future of manufacturing lies in the seamless integration of various technologies. As advancements in 3D printing materials and processes continue to develop, the synergies with traditional techniques like sand casting will only improve. Researchers are actively exploring new materials that can withstand the casting process while allowing for innovative designs. Moreover, the data-driven approach enabled by Industry 4.0 technologies will facilitate the optimization of both processes, enhancing overall efficiency.
Conclusion
The fusion of 3D printing and sand casting represents a significant leap forward in manufacturing capabilities. By harnessing the strengths of both methodologies, manufacturers can achieve greater design flexibility, reduced lead times, cost savings, and enhanced product quality. As technology continues to evolve, the collaborative potential of these two processes will likely usher in a new era of innovation, ultimately reshaping the manufacturing landscape.
Post time:12월 . 26, 2024 03:08
Next:Advancements and Innovations in Sand Casting Techniques for Modern Manufacturing Processes