Steps of Sand Casting
Sand casting is a widely used method for manufacturing metal parts and components. It offers versatility in design and the ability to cast complex shapes with high accuracy. The process begins with creating a mold, typically made of sand, which can be reused for multiple castings. Here, we outline the key steps involved in sand casting, highlighting its importance in various industries.
1. Pattern Making
The first step in sand casting is the creation of a pattern, which serves as a replica of the final product. Patterns can be made from various materials, including wood, metal, or plastic, and are designed slightly larger than the final dimensions to account for shrinkage during the cooling process. The pattern is crafted with precision to ensure that the details of the final casting are captured accurately.
2. Mold Preparation
Once the pattern is ready, the next step is preparing the sand mold. This involves mixing sand with a binding agent, such as clay, and moisture to enhance its cohesiveness. The mold is created by compressing the sand around the pattern in a two-part mold box. After the sand is packed firmly, the pattern is removed, leaving a cavity in the shape of the desired part. Sometimes, additional features are incorporated into the mold for ease of casting and improved finishing.
3
. Core MakingFor parts with internal cavities or complex geometries, cores are used. Cores are typically made from sand and are inserted into the mold before pouring the molten metal. This allows for more intricate designs and improves the functionality of the final product. Cores are usually designed to be easily removable once the casting has solidified.
steps of sand casting
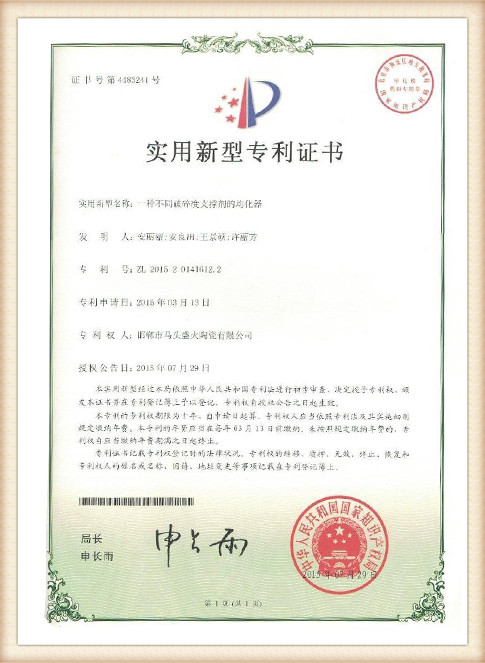
4. Melting and Pouring
The next step involves melting the metal that will be cast. This is typically done in a furnace where the metal is heated to its melting point. Once the metal reaches the required temperature, it is poured into the mold through a gating system, which directs the flow of molten metal into the cavity. Care must be taken to pour continuously and avoid introducing air pockets, which can lead to defects in the final product.
5. Cooling and Solidification
After pouring, the mold is left to cool, allowing the molten metal to solidify. The time required for cooling depends on the thickness of the casting and the type of metal used. Proper cooling is critical to achieve the desired mechanical properties and surface finish.
6. Mold Removal and Finishing
Once the metal has cooled and solidified, the mold is broken away to reveal the casting. The casting may then go through various finishing processes, such as grinding, sanding, or machining, to achieve the final dimensions and surface quality.
In conclusion, sand casting remains a vital manufacturing process due to its adaptability and cost-effectiveness. By following these six steps—pattern making, mold preparation, core making, melting and pouring, cooling and solidification, and finishing—manufacturers can produce high-quality metal components for a wide range of applications. Its significance in industries like automotive, aerospace, and metalworking underscores the enduring relevance of this traditional yet efficient method of production.
Post time:ಸೆಪ್ಟೆಂ . 22, 2024 10:52
Next:sand resin mixture