Understanding Sand Casting The Role of Resin in Casting Processes
Sand casting is one of the oldest and most widely used methods for metal casting. This technique involves creating a mold by compacting sand around a pattern, typically made of metal or plastic. The use of resin in sand casting has revolutionized the process, improving the quality and precision of castings. In this article, we will explore the intricacies of sand casting and the significant role that resin plays in this time-honored method.
The Basics of Sand Casting
Sand casting begins with the creation of a pattern that represents the object to be produced. The pattern is placed in a mold box, and fine sand is packed around it. Traditional sand casting uses a mixture of sand and clay, but the introduction of resin has enhanced this process. The resin-bonded sand can create a stronger and more stable mold that can withstand the high temperatures of molten metal.
After creating the mold, the pattern is removed, leaving a cavity in the shape of the desired object. The molten metal is then poured into this cavity and allowed to cool and solidify. Once cooled, the mold is broken apart to reveal the cast object. This method is celebrated for its ability to produce complex shapes and large parts.
The Role of Resin in Sand Casting
Resin contributes significantly to the sand casting process, particularly in the formulation of the mold. There are two main types of resin used in this method epoxy and phenolic resin.
1. Epoxy Resin Epoxy resins offer excellent adhesion and flexibility. When mixed with sand, they create a mold that can hold its shape under the thermal stress of molten metal. The use of epoxy resin results in smoother surface finishes on cast parts, reducing the need for extensive machining after casting.
2. Phenolic Resin Known for its higher thermal stability and strength, phenolic resin is widely used in sand casting applications that require durability and high temperature resistance. It creates a firmer bond within the sand, leading to a mold that can endure the harsh conditions of casting without deforming.
sanding casting resin
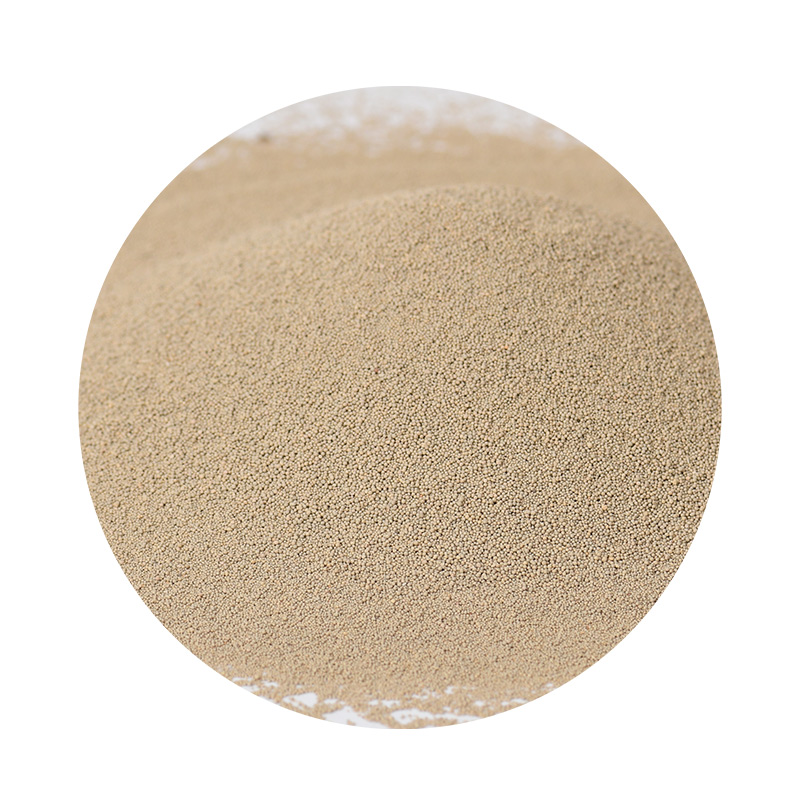
The incorporation of these resins allows for the production of more intricate and detailed designs that might be challenging to achieve with traditional clay-bonded sand molds. Furthermore, the resin system reduces the environmental impact by eliminating the need for water, which can be a contaminant in traditional sand casting processes.
Advantages of Resin-Bonded Sand Casting
The advantages of using resin in sand casting are numerous
- Improved Surface Quality Parts produced using resin-bonded sand molds generally have better surface finishes, leading to reduced post-processing costs.
- Enhanced Precision and Detail The ability of resin to form intricate shapes enables manufacturers to produce complex designs without sacrificing accuracy.
- Reduced Defects Molds made from resin-bonded sand are less prone to collapse or shift during metal pouring, resulting in fewer casting defects like misalignment and incomplete fills.
- Versatile Applications From automotive components to artistic sculptures, resin sand casting is adaptable for a wide range of industries.
Conclusion
Sand casting remains a pivotal method in metal fabrication, and the introduction of resin has significantly improved its capabilities. The enhanced properties of resin-bonded sand molds have allowed for greater precision, better surface finishes, and reduced environmental impact, making it a preferred choice for many modern manufacturing processes. As technology continues to advance, the future of sand casting with resin holds exciting possibilities, paving the way for even more innovative applications in various industries. Whether for mass production or artisanal creations, resin in sand casting is undeniably shaping the future of metal casting.
Post time:ಡಿಸೆ . 05, 2024 16:45
Next:Current Market Trends for Resin Coated Sand Pricing and Analysis