Exploring Sand Casting Technology An Essential Technique in Manufacturing
Sand casting, a widely recognized manufacturing process, has been an integral part of metal forming for centuries. It is a versatile and economically viable technique that allows for the production of complex metal parts with relatively low initial costs. The core principle of sand casting involves using sand as the mold material to create shapes for molten metal, which solidifies into the final part once cooled. This essay delves into the intricacies of sand casting technology, its advantages, applications, and future prospects.
At the heart of sand casting is the creation of a mold, which starts with the design of the pattern. The pattern, usually made from wood, metal, or plastic, is an exact replica of the desired part. It is placed in a sand mixture, typically composed of silica sand, clay, and water, to create a mold. Once the pattern is removed, the two halves of the mold are assembled, leaving a cavity that mirrors the shape of the pattern. The molten metal is then poured into this cavity, filling it completely. After the metal cools and solidifies, the sand mold is broken to reveal the cast part.
One of the key advantages of sand casting is its versatility. This process can accommodate a vast range of metals, including aluminum, bronze, iron, and various alloys. As a result, sand casting is suitable for producing both small and large components. Furthermore, the ability to create intricate designs and geometries enables manufacturers to meet specific customer requirements, making sand casting an attractive option for custom parts.
Cost-effectiveness is another significant advantage of sand casting. Compared to other manufacturing processes such as die casting or investment casting, sand casting has lower tooling costs. The molds can be created quickly, and the raw materials are readily accessible. This makes sand casting an ideal choice for small to medium-sized production runs, as well as for prototype development.
sand casting technology
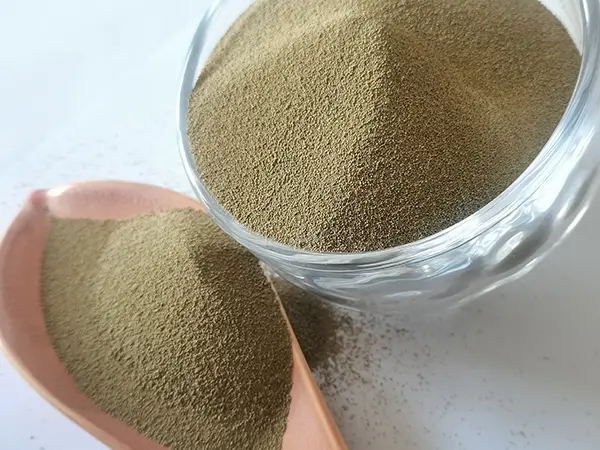
Moreover, sand casting is a highly adaptable process. It can be employed in various industries, including automotive, aerospace, and construction. In the automotive industry, for instance, sand casting is commonly used to produce engine blocks, gearbox housings, and other critical components. Its ability to produce complex geometries makes it an invaluable technique for engineers and designers seeking to push the boundaries of innovation.
However, sand casting is not without its challenges. One of the primary drawbacks is the surface finish of the cast parts, which is generally rougher compared to other processes. This can necessitate additional machining or finishing operations, adding to the overall production time and cost. Furthermore, achieving tight tolerances can be difficult, which may limit the use of sand casting in certain applications where precision is paramount.
Despite these challenges, advancements in sand casting technology are continually being made
. The integration of computer-aided design (CAD) and simulation software has significantly improved the mold design process, allowing for better visualization and optimization of the casting process. Modern materials and additives have also enhanced the properties of the sand, improving mold strength and reducing defects.The future of sand casting technology is promising. As industries increasingly prioritize sustainability, sand casting processes are adapting to incorporate environmentally friendly practices. Innovations such as the development of recycled sand and new binders aim to reduce waste and enhance the ecological footprint of sand casting operations. Furthermore, the rise of 3D printing technology is revolutionizing the way molds are created, allowing for greater design flexibility and faster turnaround times.
In conclusion, sand casting technology is a cornerstone of modern manufacturing, providing a versatile, cost-effective, and adaptable method for producing a wide range of metal parts. Despite facing challenges, its continued evolution through technological advancements ensures its relevance in the manufacturing landscape. As industries move toward more sustainable practices and innovative design approaches, sand casting is poised to remain a vital player in shaping the future of metalworking.
Post time:ನವೆಂ . 20, 2024 00:07
Next:coated sand casting