Understanding Sand Casting A Traditional Metal Casting Process
Sand casting, one of the oldest and most versatile metal casting processes, plays a pivotal role in manufacturing a wide range of metal components used in various industries today. This process involves using sand as the primary mold material, which allows for relatively low cost and flexibility in producing intricate shapes. In this article, we will explore the fundamentals of sand casting, its advantages, key components, and applications in modern manufacturing.
The Sand Casting Process
The sand casting process begins with the creation of a mold. This involves two halves the cope (top half) and the drag (bottom half). A pattern—typically made from metal, plastic, or wood—is placed in a sand mixture that contains a binding agent like clay. The sand is compacted around the pattern to create a mold cavity. Once the pattern is removed, two halves of the mold are assembled, forming a hollow shape that represents the desired part.
Next, molten metal is poured into the mold cavity through a gating system designed to control the flow and minimize turbulence. The metal is then allowed to cool and solidify, forming the final product. After solidification, the mold is broken apart, and the casting is removed. Subsequent processes, such as trimming and machining, may be performed to achieve the required dimensions and surface finish.
Advantages of Sand Casting
Sand casting offers several advantages, making it an ideal choice for various applications
1. Cost-Effectiveness The materials used for the molds are relatively inexpensive compared to other molding materials, making sand casting an economical option for producing both low and high volumes of parts.
2. Versatility Sand casting can be used with a variety of metals, including iron, aluminum, bronze, stainless steel, and other alloys. This versatility makes it suitable for diverse applications across different industries.
3. Complex Geometries The flexibility of sand allows for the creation of complex and intricate shapes that would be challenging or impossible to achieve with other casting methods. This is particularly beneficial for parts with internal cavities and complex designs.
4. Scalability Sand casting is scalable; it can be used for small prototype runs as well as large production batches. This makes it an attractive choice for manufacturers looking to develop new products without the need for extensive initial investment.
sand casting metal process
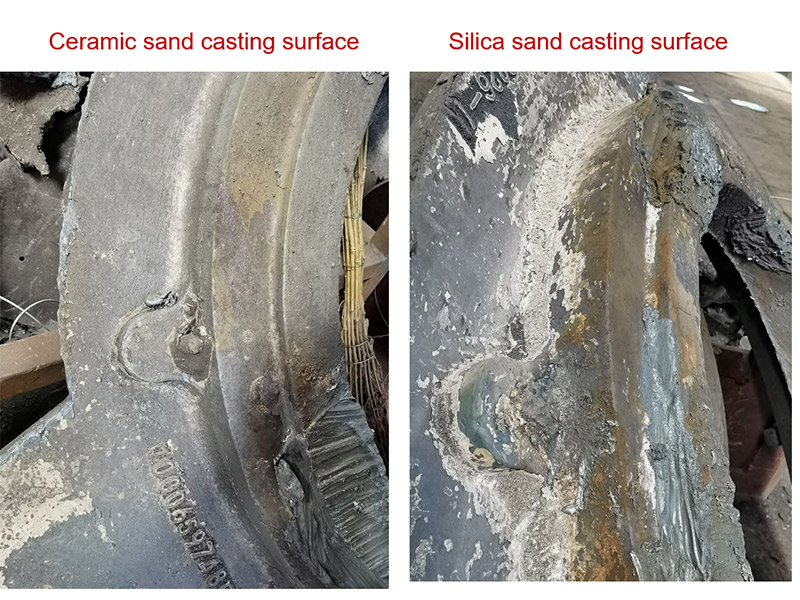
Key Components of Sand Casting
Several key components are essential to the sand casting process
- Pattern The pattern is a replica of the final product that determines the mold's cavity. Patterns can be made from various materials, depending on the required precision, durability, and cost.
- Molding Sand The primary material for the mold, consisting of silica sand mixed with clay and water. The properties of the sand affect mold strength, permeability, and thermal stability.
- Binder Often clay, the binder helps hold the sand grains together, providing strength to the mold. The right binder ensures that the mold maintains its shape during metal pouring.
- Gating System The design of the gating system is crucial for managing the flow of molten metal into the mold. An efficient system minimizes defects and enhances the overall quality of the casting.
Applications of Sand Casting
Sand casting is widely utilized in various industries including automotive, aerospace, construction, and art. It is commonly used to produce engine blocks, cylinder heads, and components for heavy machinery. Additionally, its ability to create large, heavy castings makes it particularly valuable in industries requiring robust components.
In the aerospace sector, sand casting facilitates the production of intricate parts such as turbine housings and brackets. Furthermore, the artistic community benefits from sand casting for creating sculptures and decorative metal works, showcasing the process's adaptability beyond mass production.
Conclusion
In conclusion, sand casting remains a fundamental metal casting process that blends tradition with modern advances in technology. Its cost-effectiveness, versatility, and ability to produce complex geometries ensure its continued relevance in contemporary manufacturing. Whether producing simple components or intricate designs, sand casting will always hold a significant place in the world of metal fabrication, proving that sometimes the oldest techniques can adapt and thrive alongside advanced technologies.
Post time:ನವೆಂ . 24, 2024 15:41
Next:is sand casting expensive