Sand Casting Foundry Process An Overview
Sand casting is one of the oldest and most versatile metal casting processes, renowned for its ability to produce complex shapes with excellent dimensional accuracy. This method is widely used in various industries, including automotive, aerospace, and manufacturing, to create parts from a variety of metals such as iron, aluminum, and bronze. The sand casting foundry process involves several key steps, each critical to the successful production of high-quality cast components.
1. Design and Pattern Making
The first step in the sand casting process is the design of the component to be cast. Engineers use computer-aided design (CAD) software to create precise 3D models. Once the design is finalized, a pattern is created. Patterns can be made from various materials, including wood, metal, or plastic, depending on the complexity of the part and the volume of production. The pattern serves as a reference for creating the mold cavity and is typically slightly larger than the final part to account for metal shrinkage upon cooling.
2. Mold Creation
The mold is created by compacting sand around the pattern. The sand used in this process is usually a mixture of silica sand, a bonding agent (commonly clay), and water. The process can take several forms, including green sand molding, where the sand is used in its natural state, or resin-bonded sand molding, which involves chemically treated sand for better durability and surface finish. Once the sand is compacted around the pattern, it is carefully removed, leaving a mold cavity that mirrors the shape of the pattern.
3. Core Making
In cases where the casting requires internal features or complex geometries, cores are created. Cores are made from similar sand mixtures and are placed in the mold cavity to define the internal surfaces of the part. Cores are also designed with vents to allow gases to escape during the melting and pouring process. Proper core placement is crucial to ensure that the final casting meets design specifications.
sand casting foundry process
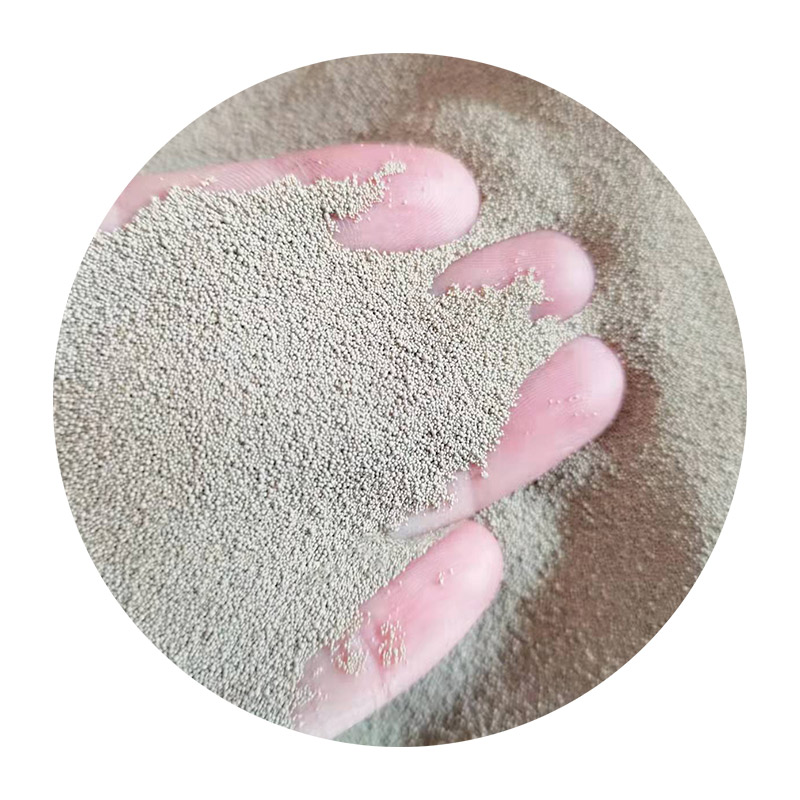
4. Melting and Pouring
Once the mold and cores are ready, the next step is to prepare the metal for casting. The selected metal is melted in a furnace, reaching temperatures high enough to liquefy it. The molten metal is carefully poured into the mold through a sprue, which leads to the mold cavity. Proper pouring techniques are essential to prevent defects such as inclusions or air pockets, which can compromise the integrity of the final product.
5. Cooling and Solidification
After pouring, the molten metal begins to cool and solidify within the mold. The cooling rate can significantly affect the properties of the cast metal, including its strength and hardness. Once the metal has completely solidified, the mold is broken apart, and the casting is revealed. This process can involve shaking out sand or using tools to remove the mold from the casting.
6. Finishing
The final step in the sand casting process is finishing. This involves several operations such as trimming, grinding, and surface treatment to remove any imperfections, sharp edges, or excess material left from the casting process. Depending on the application, further treatments, such as heat treatment or coating, may be applied to improve the mechanical properties and corrosion resistance of the cast component.
Conclusion
The sand casting foundry process is characterized by its flexibility, cost-effectiveness, and ability to produce intricate designs. From the initial pattern making to the final finishing touches, each step in the process is critical to ensuring that high-quality cast parts are produced. As industries continue to evolve, advancements in materials and technologies will further enhance the capabilities of sand casting, maintaining its relevance in modern manufacturing.
Post time:ಆಕ್ಟೋ . 16, 2024 06:29
Next:Harnessing the Power of Sanding Resin for Superior Finishing Results