Sand Used in Sand Casting An In-depth Exploration
Sand casting is one of the oldest and most versatile metal casting processes utilized in manufacturing today. It involves the use of sand as a primary mold material for shaping molten metal into desired forms. The type of sand used in this process plays a crucial role in determining the quality of the final castings. This article will delve into the characteristics, types, and implications of using sand in sand casting.
The most commonly used sand in sand casting is silica sand, primarily due to its availability and favorable properties. Silica sand is composed mainly of silicon dioxide (SiO2), which can withstand high temperatures encountered during the melting of metal. This type of sand possesses excellent thermal stability, making it suitable for the casting process where temperatures may exceed 1500 degrees Celsius.
Sand Used in Sand Casting An In-depth Exploration
To enhance the properties of silica sand, it is often mixed with additives such as clay and water to form a moldable mixture. Clay, particularly bentonite, is added to improve binding properties and plasticity. When mixed with water, this combination allows the sand to retain its shape when compacted around the pattern, creating a solid mold that can withstand the weight of molten metal. The right proportion of clay and moisture content is critical; too much clay can result in excessive “burn-on” defects, while too little can lead to weak molds.
sand used in sand casting
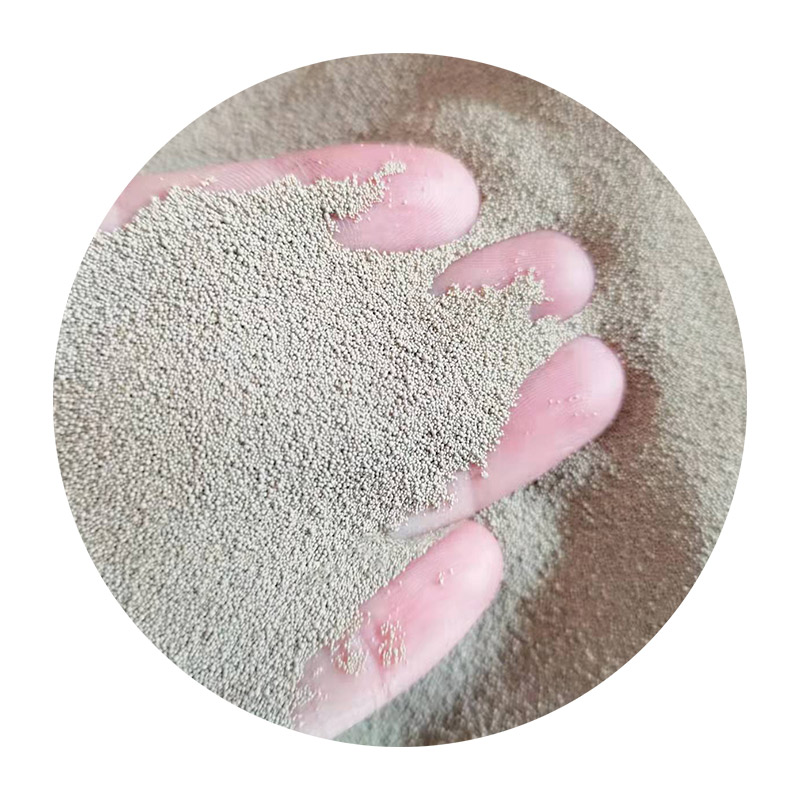
Moreover, sand casting utilizes various types of sands, each suitable for specific applications. For instance, olivine sand and zircon sand are alternatives that offer unique advantages such as lower thermal expansion and higher dimensional stability. These sands can be particularly beneficial when high precision is required in the final product. Similarly, although more expensive, using specialty sands can yield better results in applications demanding intricate designs or high tolerances.
The environmental impact of sand used in casting has also gained attention in recent years. The extraction and processing of silica sand can lead to ecological concerns, prompting manufacturers to consider recycled sand. This practice not only minimizes waste but also reduces costs associated with raw materials. Effective cleaning and reprocessing methods have advanced, making the reuse of sand in casting more viable and environmentally friendly.
In terms of sustainability, the industry is evolving towards alternatives that may reduce reliance on traditional casting sands. Developments in 3D printing technology for molds and cores present exciting opportunities. This advancement allows for more complex mold designs without the limitations imposed by conventional sand molds, suggesting a potential shift in sand casting practices in the future.
In conclusion, the choice of sand used in sand casting is pivotal to the overall success of the casting process. With the right type and treatment of sand, manufacturers can achieve high-quality castings that meet stringent industry requirements. As technology progresses and environmental considerations become increasingly critical, the sand casting industry is poised for innovations that will enhance both production efficiency and sustainability.
Post time:ಸೆಪ್ಟೆಂ . 10, 2024 03:02
Next:resin sand casting