Parting Sands in Foundry The Role and Importance of Sand Molding in Metal Casting
The foundry industry is a cornerstone of manufacturing, providing essential components for various sectors including automotive, aerospace, and construction. Among the critical processes in foundry operations is sand molding, where parting sands play a significant role. Understanding the function of parting sands and their relevance to the metal casting process can provide insights into the overall efficiency and quality of foundry outputs.
Understanding Parting Sands
Parting sands are fine-grained materials used in sand molding to create a separation between different layers of sand in a mold. The primary purpose of parting sand is to prevent the adherence of the molding sand to the pattern or to previously layered sand. This separation is crucial for ensuring that the pattern can be easily removed from the mold without damaging the sand structure, which could lead to defects in the final cast piece.
Parting sand is typically composed of a variety of silica sand that is coated with a thin layer of oil or other agents to enhance its properties. This treatment minimizes friction and helps maintain the integrity of the mold. The choice of parting sand significantly influences the surface finish of the cast product, making it a vital component of the molding process.
The Role of Parting Sands in Molding
The application of parting sands occurs primarily in two scenarios when creating the cope and drag pieces of a mold and in complex molds requiring multiple layers. In each case, the parting sand allows for smoother operations when assembling and disassembling the mold, and it helps achieve the intricate details often required in modern metal casting.
1. Ease of Mold Release The most critical advantage of parting sands is their ability to facilitate the easy removal of patterns. When patterns are crafted with a high level of detail, any sticking can result in damage. The incorporation of parting sands mitigates this risk, ensuring that the pattern can be extracted cleanly.
parting sand in foundry
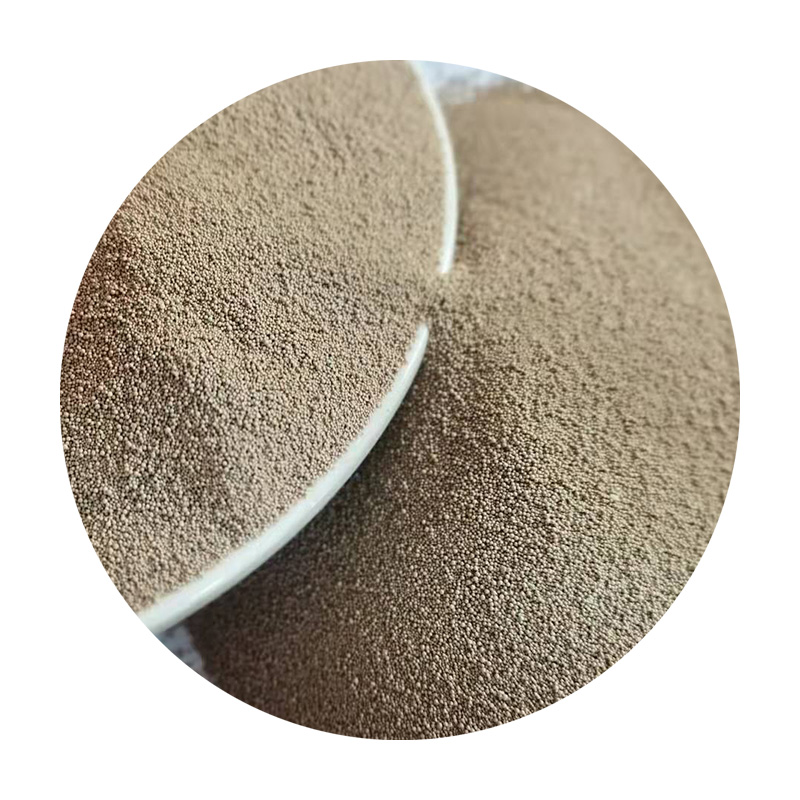
2. Surface Finish A good quality parting sand contributes to the surface finish of the final cast. Coarser sands may lead to rough finishes, while finer, well-prepared parting sands can help produce smoother surfaces that comply with stringent quality standards.
3. Durability of Molds Parting sands help in preserving the integrity of the mold throughout the casting process. By reducing the friction and wear between the mold materials, they enable longer-lasting molds, which can withstand multiple uses without significant degradation.
Quality Control and Management
In foundry operations, the selection of appropriate parting sands is also a matter of quality control. Foundry managers must monitor the characteristics of parting sands, including grain size, shape, and the presence of impurities that may affect the overall casting performance. Continuous testing and adjustment can ensure optimal performance, culminating in high-quality cast products.
Additionally, the environmental impact of parting sands is garnering increased attention. The use of sustainable materials, as well as recycling of used sands, are becoming common practices in modern foundries. This shift not only enhances the overall sustainability of the foundry process but also contributes to a circular economy within the industry.
Conclusion
Parting sands may appear to be a minor element in the vast landscape of foundry operations, yet their significance cannot be understated. Their role in ensuring the smooth release of patterns, enhancing the surface finish of castings, and contributing to the durability of molds underscores their importance in the metal casting process. As foundries strive for greater efficiency and sustainability, the optimization of parting sands will remain a key focus. By recognizing the crucial function of these materials, stakeholders in the foundry industry can enhance their operations, improve product quality, and adapt to the evolving landscape of manufacturing.
Post time:ಡಿಸೆ . 05, 2024 16:44
Next:فريدة من نوعها صب الرمل