Materials Used for Sand Casting
Sand casting is one of the oldest and most versatile metal casting processes, renowned for its ability to produce complex shapes and large parts. The process utilizes a mixture of sand, a bonding agent, and other materials to create molds in which molten metal is poured. The selection of materials plays a crucial role in determining the quality, strength, and finish of the final product. This article explores the primary materials used in sand casting, highlighting their importance and characteristics.
1. Sand
The most significant material in sand casting is, of course, the sand itself. Silica sand is the most commonly used type due to its excellent properties. It is composed primarily of silicon dioxide (SiO2) and has a high melting point, making it ideal for withstanding the heat from molten metal. The grain size of the sand can vary; finer grains provide a better surface finish but may be more challenging to work with in terms of mold strength, while coarser grains offer better strength but a rougher finish.
To hold the sand grains together, binders are essential. Clay is the most traditional binder used in sand casting, particularly when mixed with silica sand to form a green sand mold. This mixture retains sufficient moisture, allowing it to retain its shape while being strong enough to withstand the pouring of molten metal. Other modern binders include resin systems, which provide superior strength and flexibility, allowing for more intricate designs. The choice of binder can significantly influence the mold's characteristics, including its ability to withstand heat and its overall durability.
3. Additives
materials used for sand casting
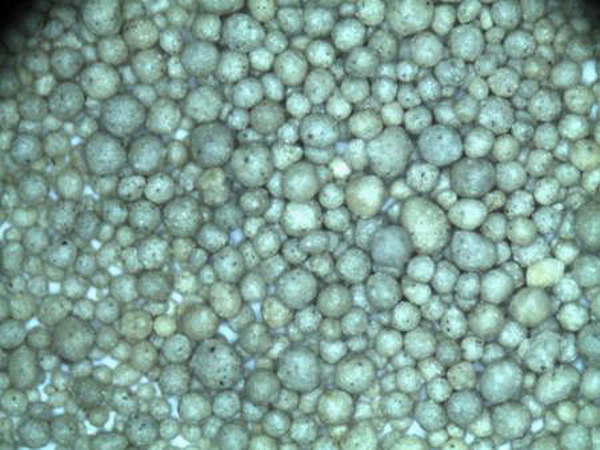
Additives may be incorporated into the sand mixture to enhance specific properties. For instance, coal dust is commonly added to improve the surface finish and reduce casting defects. Other additives, such as inorganic binders and surfactants, can be used to modify the mold’s permeability and thermal stability, ensuring the casting process runs smoothly without complications.
4. Metal Alloys
The type of metal poured into the sand mold is another crucial aspect of sand casting. Common materials include aluminum, brass, bronze, and iron, each of which possesses unique properties. Aluminum is favored for its lightweight and corrosion resistance, while iron is typically preferred for applications requiring greater strength and durability. The selection of metal not only affects the casting's physical properties but also influences the cooling rates and solidification patterns, which are vital for dimensional accuracy and the integrity of the final product.
5. Core Materials
For hollow castings, cores made from sand or metal are used to create internal cavities. These cores are typically made from a sand mixture and are baked or treated with a binder to ensure they maintain their shape during the casting process. The choice of core material can impact the overall quality and complexity of the final casting.
Conclusion
The materials used in sand casting are fundamental to the casting's success. From the selection of sand and binders to the choice of molten metal and core materials, each component plays an important role in achieving high-quality castings. Understanding these materials and their properties can significantly enhance the efficiency and effectiveness of the sand casting process, leading to better performance and greater customer satisfaction. As technology evolves, continued innovations in materials will likely expand the possibilities within sand casting, contributing to its ongoing relevance in the manufacturing industry.
Post time:ಸೆಪ್ಟೆಂ . 14, 2024 01:54
Next:3D Geprinte Zandgiettechnologie voor Innovatieve Productie