The Iron Sand Casting Process
Iron sand casting is a well-established manufacturing technique widely used in the production of various components and parts across different industries. This process involves the use of iron-rich sand as the primary material, providing various advantages, including cost-effectiveness, versatility, and the ability to produce complex shapes with excellent surface finishes. The following article explores the intricacies of the iron sand casting process, its advantages, and its applications.
Overview of the Iron Sand Casting Process
The iron sand casting process primarily involves creating a mold from a mixture of sand and binding agents, which is then filled with molten iron to form a desired shape. The process can be categorized into several key steps
1. Pattern Making The first step is to create a pattern, which is a replica of the desired final product. Patterns can be made from various materials such as wood, metal, or plastic. The choice of material often depends on the production volume and the specifics of the design.
2. Mold Preparation Once the pattern is ready, it is used to create a mold. This involves packing the iron sand around the pattern to form a cavity. The sand is often mixed with a binding agent (such as clay) and water to improve its cohesion. The packed sand is compacted to ensure it holds the shape of the mold once the pattern is removed.
3. Core Making In cases where the casting requires hollow spaces or intricate internal shapes, cores made of sand are created. These cores are placed within the mold before pouring in the molten iron.
4. Pouring After the mold and cores are prepared, molten iron is poured into the mold cavity. The temperature of the molten iron is crucial; it typically ranges from 1,400°C to 1,500°C (2,550°F to 2,732°F). The molten iron fills the mold, taking its shape as it cools.
5. Cooling and Solidification Once poured, the molten iron begins to cool and solidify. The cooling rate can affect the properties of the final product; slower cooling often leads to a finer grain structure, enhancing the mechanical properties of the casting.
6. Mold Removal and Finishing After sufficient cooling, the mold is broken away to reveal the casting. The casting might have rough edges and surface defects, requiring further machining or finishing processes to achieve the desired specifications.
Advantages of Iron Sand Casting
iron sand casting process
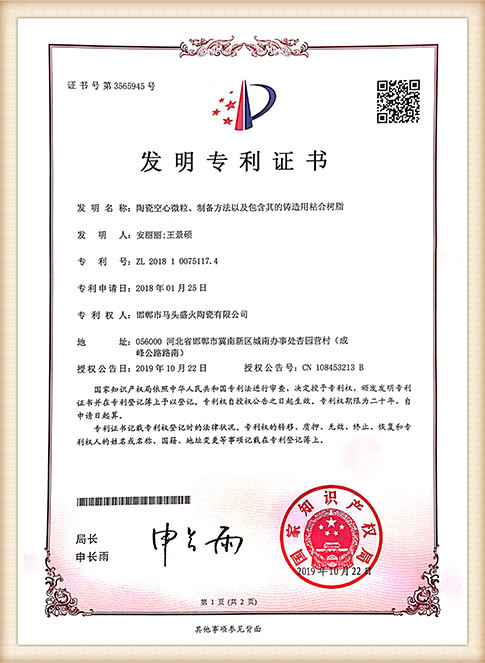
One of the most significant advantages of iron sand casting is its cost-effectiveness, especially for low to medium production runs
. The materials required for sand molds are relatively inexpensive, and the process allows for the recycling of sand, reducing waste.Iron sand casting also offers excellent versatility. It can be used to produce a wide range of products, from small components to large industrial parts. The technique accommodates complex geometries, making it possible to create intricate designs that might be challenging with other manufacturing processes.
Another notable benefit is the fine surface finish achievable with iron sand casting. When properly prepared and managed, the quality of the final product meets high standards, reducing or even eliminating the need for extensive post-processing.
Applications of Iron Sand Casting
Iron sand casting is utilized across various industries, marking its significance in modern manufacturing. Some common applications include
- Automotive Industry Iron sand casting is often used to create engine blocks, transmission cases, and other essential components that require durability and strength. - Construction The construction industry relies on iron sand casting for products such as pipe fittings and heavy machinery parts, which require robust materials to withstand stress and wear.
- Marine Engineering Components exposed to harsh marine environments, including propellers and engine parts, benefit from the corrosion resistance and strength offered by iron castings.
- Art and Sculpture Beyond industrial applications, artists utilize iron sand casting to create sculptures and artistic pieces, benefiting from the material's versatility and aesthetic appeal.
Conclusion
The iron sand casting process remains a vital manufacturing technique due to its efficiency, cost-effectiveness, and versatility. As industries continue to evolve, innovations in casting techniques and materials promise to enhance the quality and capabilities of iron sand castings. Understanding this process not only highlights the significance of traditional manufacturing techniques but also emphasizes their relevance in the face of emerging technologies. The future of iron sand casting looks promising, maintaining a central role in creating durable and complex components across various fields.
Post time:ಆಕ್ಟೋ . 21, 2024 01:28
Next:Time Required for Sand Casting Process and Factors Influencing It