The Foundry Sand Casting Process An Overview
The foundry sand casting process is a time-honored manufacturing technique that has been employed for centuries to produce a wide variety of metal components. This method is particularly favored for its versatility, affordability, and ability to create intricate shapes with a smooth surface finish. Understanding the fundamental stages of the foundry sand casting process is essential for anyone involved in manufacturing, engineering, or metallurgy.
1. Pattern Creation
The first step in the sand casting process is the creation of a pattern, which serves as a replica of the final product. Patterns are typically made from materials such as wood, metal, or plastic and can be constructed in sand-casting or shell-casting designs. They must account for the shrinkage of material as it cools and solidifies, which is an important consideration for dimensional accuracy. Patterns may also incorporate cores that define internal features of the casting.
2. Molding
Once the pattern is prepared, the next step is to form a mold using a mixture of sand and a binding agent, usually clay or resin. The sand is compacted around the pattern to create a mold cavity. A typical molding process involves placing the pattern in a molding box, filling the box with the sand mixture, and compacting the sand around the pattern. Care must be taken to ensure that the mold is uniform and that there are no air pockets or inconsistencies. After compacting, the mold is split, and the pattern is removed, leaving a hollow cavity that mirrors the original pattern's shape.
foundry sand casting process
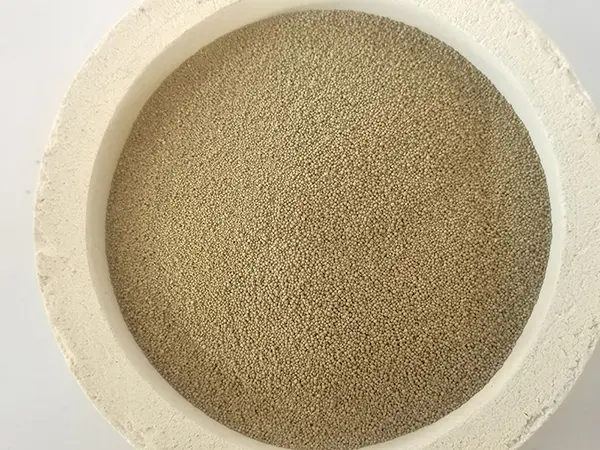
The next phase involves melting the metal that will be cast into the mold. Common metals used in sand casting include aluminum, iron, and bronze. The metal is melted in a furnace, which can be fueled by electricity, natural gas, or coke depending on the required temperature and volume of metal. Once the metal reaches the appropriate temperature, it is poured into the mold cavity via a pouring cup connected to a sprue, allowing the molten metal to flow and fill the mold. This step requires precision and care, as improper pouring can lead to defects in the casted part.
4. Cooling and Solidification
After the mold is filled with molten metal, it is allowed to cool and solidify. The solidification process can vary depending on the type of metal and mold used; however, it typically takes several hours. During this time, the molten metal transforms into a solid state while contracting slightly as it cools. The cooling rate is a critical factor as it influences the mechanical properties of the metal. Generally, slower cooling rates allow for coarser grain structures, while rapid cooling promotes finer microstructures.
5. Mold Removal and Finishing
Once the casting has fully cooled, the next step is to break open the mold and remove the newly formed casting. This is usually done by hand or with the aid of tools, depending on the size of the component. After removal, the cast part typically requires further finishing operations, such as trimming excess material, sandblasting, or machining to achieve the desired tolerances and surface finish. These post-casting operations are crucial for ensuring that the final product meets specific requirements for strength, accuracy, and aesthetics.
Conclusion
The foundry sand casting process is a pivotal manufacturing technique that blends ancient practice with modern technology. It allows for the production of complex shapes and is applicable to various metals, making it an indispensable method in the manufacturing sector. As industries continue to demand customized and efficient manufacturing solutions, the foundry sand casting process remains a vital option, showcasing its enduring relevance and adaptability in the ever-evolving landscape of production engineering.
Post time:ನವೆಂ . 05, 2024 22:10
Next:Understanding the Fundamentals and Techniques of Sand Casting Processes in Metalworking