Facing Sand in Foundries An Overview
In the world of metallurgy and casting, the choice of materials plays a crucial role in determining the quality of the final product. One of the significant materials utilized in the foundry industry is facing sand. This article delves into the importance of facing sand, its properties, and its role in the casting process.
What is Facing Sand?
Facing sand is a specific formulation of sand used in the foundry industry, primarily applied to the surface of the sand molds or cores. Its purpose is to provide a fine layer that directly comes into contact with molten metal during the casting process. The term facing refers to its strategic position as the outermost layer of sand, ensuring that the mold surface can accurately replicate the desired shape and surface finish of the final product.
Composition and Properties
The composition of facing sand can vary based on the type of metal being cast and the requirements of the foundry. Typically, it consists of fine silica sand mixed with various additives to enhance its performance. Key properties that define effective facing sand include its grain size, permeability, thermal stability, and refractoriness.
1. Grain Size Fine grains help in achieving a smooth surface finish on the cast product. A smaller grain size can lead to better detail replication but may decrease permeability.
2. Permeability Adequate permeability is essential for allowing gases to escape during the pouring and cooling of molten metal. If gases are trapped within the mold, it can lead to defects such as blowholes and porosity.
3. Thermal Stability Facing sand must withstand the high temperatures generated during the casting process. The ability to resist thermal shocks minimizes the risk of cracking or deformity.
facing sand in foundry
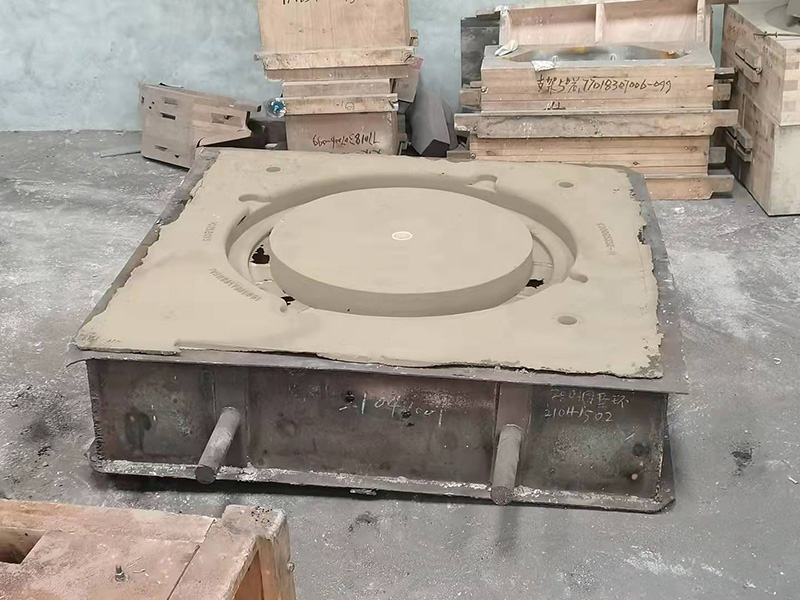
4. Refractoriness This property ensures that the sand can endure the extreme heat without sintering or melting, which could compromise the mold’s integrity.
Role in the Casting Process
The primary function of facing sand is to create an excellent surface finish on the final cast, which is vital for aesthetic and functional purposes. When molten metal is poured into a mold coated with facing sand, the sand helps capture intricate details of the mold design.
Moreover, facing sand plays a significant role in facilitating the release of gases produced during the pouring process. If the facing sand's permeability is well optimized, it will allow gases to escape, thereby minimizing defects in the cast. Additionally, the thermal properties of facing sand help insulate the mold, ensuring uniform cooling of the casting material, which is critical in preventing warping and cracking.
Challenges and Considerations
While facing sand is an integral part of the foundry process, several challenges arise in its application. One major issue is the potential for sand erosion during the metal pouring process, which may lead to surface imperfections on the cast. Foundries need to strike a balance between grain size and the amount of facing sand used to reduce these risks.
Moreover, environmental concerns regarding sand disposal and reclamation have pushed foundries to adopt more sustainable practices. Many foundries are now exploring the usage of synthetic sands or recycled materials to meet both performance and environmental standards.
Conclusion
Facing sand is an invaluable component of the foundry industry, contributing significantly to the quality of cast products. Understanding its properties and carefully managing its application can enhance casting accuracy and surface finish, ultimately leading to higher-quality manufactured goods. As foundries continue to innovate and adapt to environmental challenges, the optimization of facing sand will remain a critical focus for achieving excellence in the casting process.
Post time:ನವೆಂ . 06, 2024 16:54
Next:different types of sand casting