The Art and Science of Cast Iron Sand Casting
Cast iron sand casting stands as a venerable technique within the foundry industry, melding traditional craftsmanship with modern technology. This process utilizes sand as the primary mold-making material, allowing for the production of intricate shapes and robust components that are vital for various applications ranging from automotive parts to industrial machinery.
The Basics of Sand Casting
At its core, sand casting involves creating a mold from sand to hold molten metal. The sand is typically mixed with a binding agent, which allows it to retain its shape when packed around a pattern, usually made of metal or wood, that represents the object to be cast. Once the mold has been formed, the pattern is removed, leaving a cavity in the shape of the desired part.
After preparing the mold, molten cast iron, known for its excellent casting properties and high fluidity, is poured into this cavity. Cast iron is favored for sand casting due to its durability, strength, and ability to withstand thermal stress. Once the metal cools and solidifies, the sand mold is broken away, revealing the finished product.
Advantages of Cast Iron Sand Casting
One of the principal benefits of sand casting is its ability to produce complex geometries. The flexibility of sand molds allows for intricate designs that would be challenging or even impossible to achieve with other casting methods. This is particularly valuable in industries where customization is key.
Furthermore, the process is economical for small to medium production runs. The materials involved, primarily sand and cast iron, are widely available and relatively inexpensive. This affordability, combined with the ability to easily adapt mold designs for different products, makes sand casting a practical choice for manufacturers.
cast iron sand casting
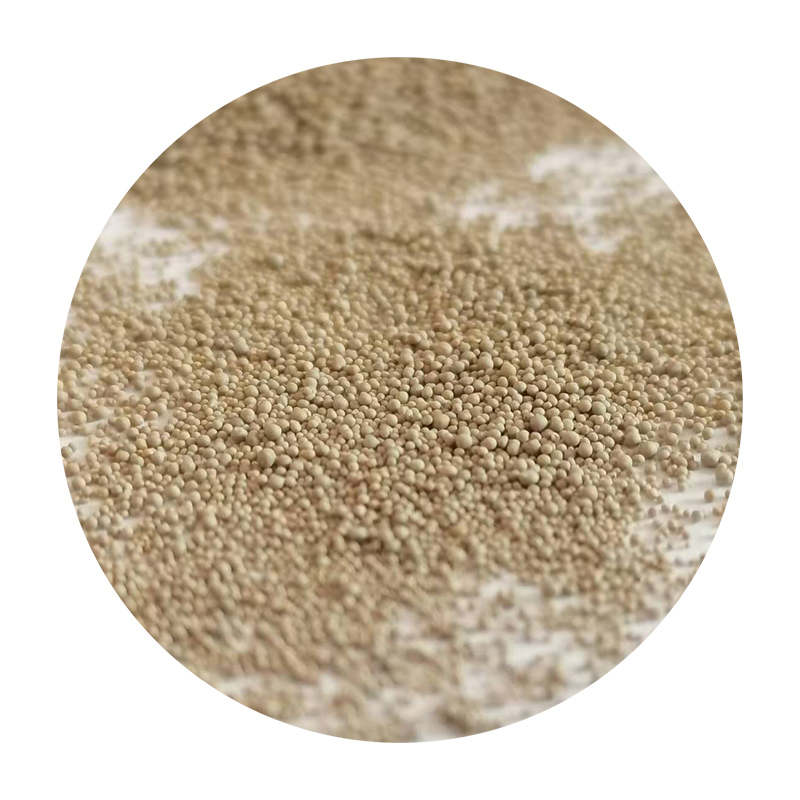
Applications and Industries
The versatility of cast iron sand casting is reflected in its wide array of applications. In the automotive sector, components such as engine blocks, crankshafts, and brake rotors are often produced using this method. The heavy-duty nature of cast iron makes it ideal for parts that must endure high levels of stress and wear.
In addition to automotive parts, sand casting is employed in the production of machinery components, agricultural equipment, and even decorative items. The construction industry also benefits from this technique, as sand casting is used to create architectural elements and structural components that require both strength and aesthetic appeal.
Innovations in Sand Casting
While sand casting may seem traditional, it has not remained static. Recent innovations have introduced new materials and technologies that enhance the efficiency and quality of the casting process. For example, the use of 3D printing technology in mold creation can significantly reduce lead times and allow for more precise and complex designs.
Moreover, advancements in computer-aided design (CAD) have allowed engineers to visualize and optimize casting processes before actual production. This leads to improvements in yield rates and reductions in material waste, making the process more sustainable.
Conclusion
In conclusion, cast iron sand casting is a fascinating intersection of art and science, embodying centuries of craftsmanship refined by modern innovations. Its applications are numerous, and its ability to produce reliable, complex components makes it an indispensable part of various industries. As technology continues to evolve, the future of sand casting looks promising, with increased efficiency and enhanced capabilities on the horizon. Whether it's for creating the sturdy parts of a vehicle or the decorative elements of a building, cast iron sand casting remains a vital process, marrying tradition and modernity seamlessly.
Post time:ಡಿಸೆ . 16, 2024 15:01
Next:Exploring the Benefits and Uses of Cerabead Sand in Various Applications