Understanding the Buy Sand Casting Process
Sand casting is a widely utilized manufacturing process that allows for the creation of complex metal parts with high precision and excellent surface finishes. It is one of the oldest metal-forming techniques and remains relevant in modern manufacturing due to its versatility, cost-effectiveness, and ability to produce intricate geometries. In this article, we will explore the intricate process of sand casting, its advantages, applications, and important considerations when sourcing this type of manufacturing service.
What is Sand Casting?
Sand casting involves creating a mold from sand, which is then filled with molten metal to create a specific part. The process begins with the preparation of a pattern, typically made from wood, metal, or plastic, which is used to create a cavity in the sand. The sand is mixed with a binding agent, usually clay and water, to give it strength and cohesion. Once the pattern is embedded in the sand and the mold halves are secured, molten metal is poured into the cavity, filling it completely.
After the metal cools and solidifies, the mold is broken away to reveal the final cast part. This technique is popular for creating large components and complex shapes, especially in industries such as automotive, aerospace, and construction.
Advantages of Sand Casting
1. Cost-Effective Sand casting is generally more affordable compared to other manufacturing processes, especially for low to medium production volumes. The materials used for molds are inexpensive, and modifications to the mold can be made easily without significant expenses.
2. Versatility This method can accommodate a wide variety of metals, including aluminum, bronze, iron, and steel, making it suitable for many applications. Sand casting is particularly advantageous for producing large castings exceeding several hundred pounds.
3. Intricate Designs Sand casting allows for the creation of intricate and detailed designs. The ability to manipulate the sand and the flexibility of mold making enable manufacturers to produce complex shapes and fine details that would be difficult to achieve through other methods.
4. Flexibility in Production Volumes Sand casting is adaptable for both small batch production and larger scale manufacturing. It can efficiently accommodate varying production volumes without requiring significant adjustments to the setup.
5. Good Surface Finish While not as refined as some other casting processes, sand casting can achieve a satisfactory surface finish, which often can be enhanced through secondary processing techniques.
Applications of Sand Casting
Sand casting is utilized in numerous industries, with some notable examples including
buy sand casting
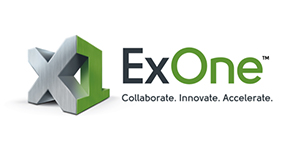
- Automotive Industry It is commonly used to produce engine blocks, transmission cases, and various other parts that require robustness and a complex design. - Aerospace Components such as turbine housings and structural parts often rely on the precision and reliability that sand casting provides.
- Marine Engineering The manufacture of parts for ships, including valves and pumps, frequently employs sand casting due to its ability to withstand harsh environments.
- Art and Decorative Items Sand casting is also employed in the production of sculptures and jewelry, where artisans can create unique designs.
Choosing a Sand Casting Provider
When looking to purchase sand casting services, there are several key considerations to keep in mind
1. Experience and Expertise Look for a foundry with a solid track record and experience in the specific type of casting you require. This includes familiarity with the materials and designs pertinent to your project.
2. Quality Assurance Ensure that the provider follows stringent quality control standards to deliver consistent and reliable products. It is crucial that parts meet the required specifications and tolerances.
3. Technology and Equipment Evaluate the technology and equipment used by the foundry. Modern facilities employing advanced techniques can often produce higher-quality castings with improved turnaround times.
4. Lead Times and Production Capacity Discuss lead times and the foundry’s capacity to meet your production needs. Ensuring that they can deliver on schedule is vital for maintaining your project timelines.
5. Customer Service A responsive and communicative supplier will enhance the overall experience, making it easier to address any questions or concerns that arise during the process.
Conclusion
Sand casting remains a popular choice for manufacturing due to its multiple advantages, including cost-effectiveness, versatility, and ability to produce complex designs. Its applications span numerous industries, demonstrating its enduring relevance in the manufacturing sector. When sourcing sand casting services, pay careful attention to the provider's expertise, quality assurance measures, and overall customer service to ensure a successful partnership.
Post time:ಡಿಸೆ . 31, 2024 07:00
Next:Exploring the Fundamentals and Innovations in Sand Casting Techniques for Metal Production