Advantages and Disadvantages of Sand Casting
Sand casting is a widely used metal casting process that involves the creation of a mold from sand and then pouring molten metal into that mold to produce a desired shape. This method has been employed for centuries and remains a popular choice in the manufacturing industry for various reasons. However, like any manufacturing process, sand casting has its own set of advantages and disadvantages.
Advantages of Sand Casting
One of the primary advantages of sand casting is its cost-effectiveness. Sand is an abundant and inexpensive material, making it a suitable choice for producing molds without incurring significant costs. This is particularly beneficial for small to medium production runs, where the expense of more advanced molding techniques would be unjustifiable.
Another notable advantage is the versatility of the process. Sand casting can accommodate a wide range of metal types, including aluminum, bronze, iron, and many others. This flexibility allows manufacturers to use sand casting for various applications, from intricate parts in machinery to large components in construction.
The design flexibility offered by sand casting is also a considerable benefit. The process can produce complex shapes and intricate details that would be challenging or impossible to achieve with other methods. Sand molds can be easily shaped, which permits the production of both simple and intricate designs without significant additional costs.
Furthermore, sand casting is highly scalable. It can be used for both small-scale operations and large volume productions, accommodating varying demands without requiring a complete overhaul of the process. This adaptability makes it an attractive option for manufacturers looking to scale their production capacities over time.
advantages and disadvantages of sand casting
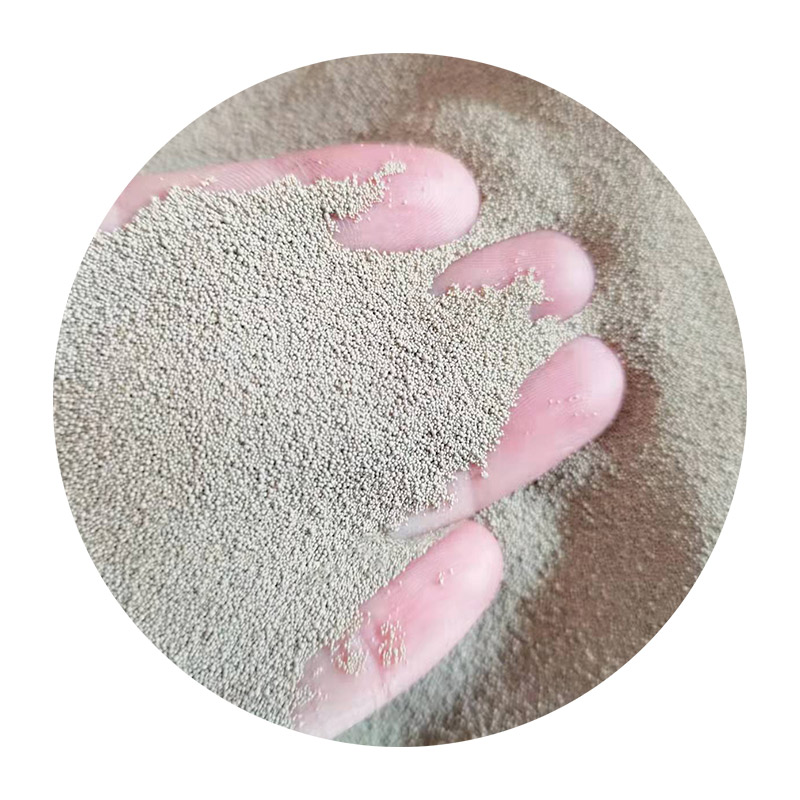
Disadvantages of Sand Casting
Despite its many advantages, sand casting also has significant drawbacks. One major disadvantage is the surface finish quality of the final product. The rough texture of sand molds can lead to castings that require additional machining or finishing to achieve the desired surface quality. This can increase production time and costs, which can negate some of the savings from using sand casting in the first place.
Another drawback is the relatively limited precision of sand casting compared to other casting methods such as investment casting. The inherent nature of sand as a mold material means that it may not capture intricate details as accurately. This can pose challenges for industries that require tight tolerances and precise dimensions in their components.
Sand casting also has lower production rates compared to other casting methods. While it can be economical for small to medium production runs, mass production often requires faster and more efficient methods, such as die casting, which can produce parts more swiftly and with higher precision.
Additionally, the process has environmental considerations. The sand used in casting often needs to be treated with binders, and the disposal of used sand can pose an environmental challenge. Furthermore, the emissions from melting metal can contribute to air pollution if not properly managed.
Conclusion
In summary, sand casting is a widely utilized manufacturing process with several advantages, including cost-effectiveness, versatility, and design flexibility. However, it also suffers from disadvantages such as surface finish quality, precision limitations, and environmental concerns. Manufacturers must weigh these pros and cons when deciding whether sand casting is the right method for their specific production needs, considering both the nature of the end products and the operational capabilities of their facilities.
Post time:ಆಕ್ಟೋ . 13, 2024 23:44
Next:cerabead