Advantages and Disadvantages of the Sand Casting Process
Sand casting is one of the oldest and most widely used metal casting processes in manufacturing. It involves creating a mold from sand and then pouring molten metal into that mold to form a desired item. This method has several advantages and disadvantages that manufacturers need to consider when deciding whether to use it for specific projects.
Advantages
1. Cost-Effectiveness One of the primary advantages of sand casting is its economic feasibility. The materials required, including sand and metal, are relatively inexpensive. Additionally, the setup costs for sand casting are generally lower than for other casting processes, making it an attractive option for small-scale production and prototypes.
2. Versatility Sand casting can accommodate a wide range of metals, including ferrous and non-ferrous alloys. This versatility makes it suitable for producing various components, from small parts to large industrial components.
3. Complex Designs The sand casting process allows for the creation of complex shapes and intricate designs. The flexibility of sand molds means that manufacturers can easily modify the mold to create different product variations without significant additional costs.
4. Good Surface Finish While the surface finish of sand-cast parts is generally not as high as other casting methods, it can be improved with additional machining. Sand casting produces a surface that is typically satisfactory for many applications.
5. Low Production Lead Time The sand casting process can be completed relatively quickly, especially for small runs. This reduced lead time can be advantageous for industries that require rapid prototyping or short production runs.
advantages and disadvantages of sand casting process
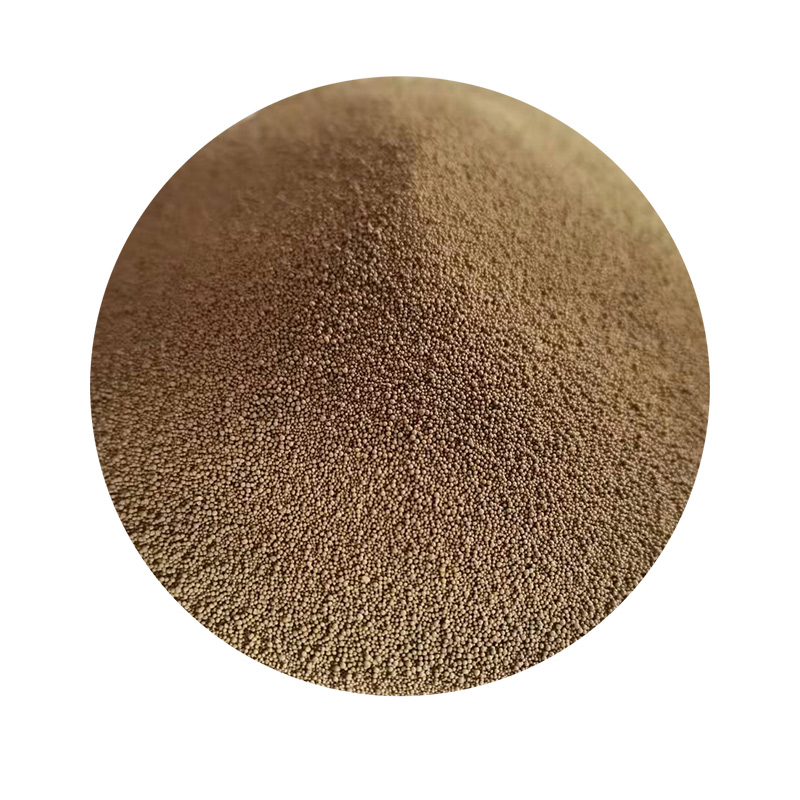
Disadvantages
1. Surface Finish Quality Although sand casting allows for complex shapes, it often results in a rough surface finish. This may require additional machining processes to achieve the desired surface quality, increasing overall production time and costs.
2. Limited Dimensional Accuracy Sand casting is generally not as precise as other methods, like investment casting. The dimensional tolerances achievable with sand casting can be looser, which might require additional quality control measures.
3. Environmental Concerns The sand casting process can have environmental implications. The disposal of used sand and the emissions from pouring molten metal can pose challenges for sustainability.
4. Labor Intensive The sand casting process can be labor-intensive, requiring skilled workers for mold preparation and metal pouring. This dependency on skilled labor can increase the total cost of production.
5. Longer Cooling Times Depending on the metal being cast and the size of the object, cooling times can be lengthy. This may extend the overall lead time for production and affect efficiency.
In conclusion, while sand casting offers several advantages such as cost-effectiveness, versatility, and the ability to create complex designs, it also presents challenges, including surface finish quality and dimensional accuracy. Manufacturers must weigh these factors against their specific needs to determine if sand casting is the right process for their applications.
Post time:ಸೆಪ್ಟೆಂ . 06, 2024 14:08
Next:Types of Sand Used in Sand Casting | A Comprehensive Guide