The Type of Sand Used for Sand Casting
Sand casting is a widely used method in the manufacturing process of various metal components. It is favored for its simplicity, low cost, and ability to produce parts in a variety of shapes and sizes. One of the most critical elements in the sand casting process is the type of sand used. In this article, we'll delve into the different types of sand suited for sand casting, their properties, and the reasons why certain sands are preferred over others.
1. The Importance of Sand in Casting
The primary function of sand in the casting process is to create a mold into which molten metal can be poured. The sand must possess specific properties to ensure that it can hold the shape of the mold, withstand high temperatures, and allow for easy removal of the casting after it has solidified. The quality of the sand can directly affect the overall quality of the finished product, making it essential to select the right type.
2. Common Types of Sand Used in Casting
a. Silica Sand
Silica sand, composed mainly of silicon dioxide (SiO2), is the most commonly used sand in sand casting. Its high melting point and thermal stability make it suitable for casting processes that involve high temperatures. Silica sand is available in various grain sizes, which allows manufacturers to select the appropriate size for their specific applications. Furthermore, its availability and low cost contribute to its widespread use.
b. Green Sand
Green sand, also known as wet sand, is a mixture of silica sand, clay, and water. The clay binds the grains of sand together, while the water provides moisture necessary for mold creation. Green sand is favored because it has excellent flowability and compaction properties, which help in forming intricate molds. It is often used for iron and nonferrous metal castings.
what type of sand is used for sand casting
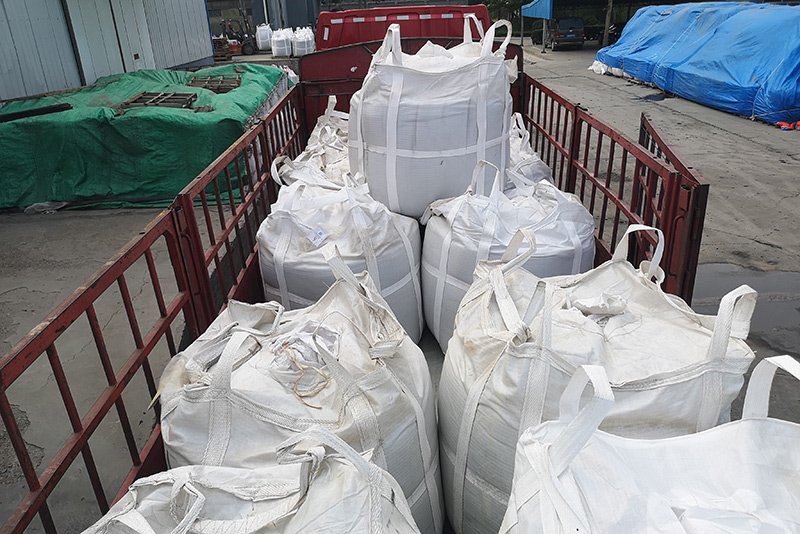
c. Resin Sand
Resin sand is a mixture of silica sand and a synthetic resin binder. This type of sand is typically used in production foundries where high precision and superior surface finishes are required. Resin sand molds can withstand higher temperatures compared to green sand molds and possess better dimensional accuracy. The use of resin sand is growing due to its ability to produce complex geometries and superior surface finishes in castings.
d. No-Bake Sand
No-bake sand, or chemically bonded sand, involves the use of a liquid binder that hardens at room temperature. This type of sand does not require moisture like green sand does, making it easier to handle. No-bake sand molds can achieve excellent surface finishes and can be reused multiple times, thus making it an economical choice for some applications. Its ability to produce detailed molds makes it popular for specific engineering applications.
3. Properties of Good Casting Sand
When selecting sand for casting, certain properties are desirable
- Grain Shape Round or sub-round grains are preferred as they will flow better and pack more densely, resulting in stronger molds. - Grain Size The size of the sand grains affects the surface finish of the casting. Finer grains yield smoother surfaces, while coarser grains can create rougher textures. - Thermal Stability The sand must be able to withstand the high temperatures of molten metal without breaking down or deforming. - Moisture Content The right amount of moisture is crucial, particularly in green sand, as it affects the bonding quality and strength of the mold.
4. Conclusion
The type of sand used in sand casting plays a vital role in determining the quality and efficacy of the casting process. Silica sand remains the most prevalent due to its cost-effectiveness and availability, while specialized sands such as resin sand and no-bake sand offer advantages for more precise applications. Understanding the properties and suitability of different sands helps manufacturers select the best material for their specific casting needs, leading to enhanced performance and reduced production costs. In the ever-evolving landscape of manufacturing, the choice of sand remains a foundational element that impacts the final product's quality and aesthetic.
Post time:ធ្នូ . 03, 2024 10:54
Next:sand castings manufacturer