Materials Used for Sand Casting An Overview
Sand casting, a widely used metal casting process, involves the creation of metal parts by pouring molten metal into a mold formed from sand. This method's popularity can largely be attributed to its low cost and flexibility, accommodating various materials and sizes. In this article, we will explore the primary materials used in sand casting, focusing on sand types, bonding agents, and additives, as well as the metals commonly cast through this process.
1. Sand Types
The most crucial component of sand casting is the sand itself. The characteristics of the sand significantly influence the quality of the casting. Traditionally, the most common type of sand used is silica sand due to its high melting point and excellent thermal properties. The sand grains must be fine and uniform to create a detailed mold, allowing the molten metal to take on the precise shape of the cavity.
Another type of sand used is olivine sand, consisting of magnesium iron silicate. Olivine sand is less prone to thermal expansion and has a high melting point, making it suitable for casting high-temperature metals. Other alternatives include zircon sand and chromite sand, both known for their thermal stability and ability to produce high-quality castings, although they are typically more expensive than silica sand.
To bind the sand particles together, bonding agents are necessary. The most common bonding agent used in sand casting is clay, specifically bentonite clay. Its unique properties enable it to hold sand grains together, creating a cohesive mold that can withstand the weight of the molten metal. Bentonite clay is mixed with water to achieve the desired consistency, ensuring the mold's stability during casting.
In addition to clay, other bonding agents can be used. Synthetic resins, for example, provide enhanced strength and reduce the tendency to crack under heat. Resin-bonded sand molds are often used in applications requiring high precision, as they can produce finer details and smoother surfaces on the final product.
what materials are used for sand casting
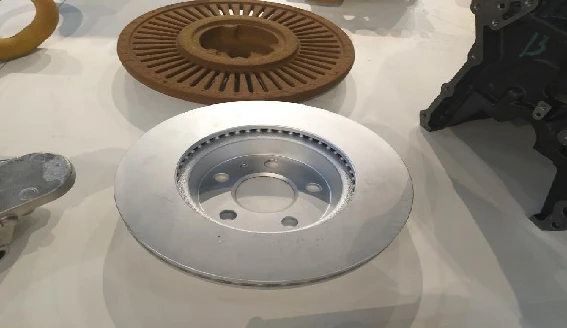
3. Additives
To enhance the qualities of the mold and improve casting performance, various additives are incorporated into the sand mixture. These additives can modify the sand's properties, such as its strength, permeability, and thermal conductivity. Common additives include
- Seeding Agents These materials enhance the mold's strength and reduce the chances of defects by promoting a more uniform flow of molten metal. - Defoamers Added to minimize the formation of gas bubbles within the mold, leading to a smoother surface finish on the cast product. - Coloring Agents Used primarily for aesthetic purposes, these agents give the sand a specific color and make it easier to differentiate between different batches or types of sand.
4. Metals Used in Sand Casting
The versatility of sand casting allows for the use of various metals, each chosen based on the desired properties of the final product. Common metals include
- Aluminum Known for its lightweight and excellent corrosion resistance, aluminum is frequently used in the automotive and aerospace industries. - Iron Cast iron, distinguished for its durability and ability to withstand wear and tear, is commonly used in engineering applications and manufacturing heavy machinery components. - Bronze This metal alloy, primarily consisting of copper and tin, is renowned for its strength and resistance to corrosion, suitable for marine applications and artistic sculptures. - Steel Carbon and alloy steels are often sand-cast for critical applications that demand strong and resilient components.
In conclusion, sand casting is a practical and efficient method for producing a wide array of metal parts. The choice of materials—ranging from silica sand and bonding agents to the specific metals cast—plays a pivotal role in determining the quality, precision, and performance of the final products. Understanding these materials and their properties is essential for engineers and manufacturers looking to maximize the effectiveness of the sand casting process.
Post time:ធ្នូ . 22, 2024 16:19
Next:Feuchter Sand für 3D-Drucktechniken und innovative Anwendungen im Schaffensprozess