Understanding Resin-Coated Sand A Comprehensive Overview
Resin-coated sand (RCS) is a specialized material commonly utilized in foundry applications and other industrial processes. It plays a crucial role in producing high-quality castings with enhanced surface finishes and dimensional accuracy. This article aims to detail what resin-coated sand is, its composition, manufacturing process, and various applications, all while highlighting the advantages it brings to modern manufacturing.
What is Resin-Coated Sand?
Resin-coated sand is essentially sand grains that are coated with a thermosetting resin. These resins are typically phenolic or urethane-based, which provide excellent bonding properties and improve the sand's performance during molding and casting processes. The coating not only enhances the mechanical properties of the sand but also ensures that it retains its shape and integrity throughout the casting process.
Composition of Resin-Coated Sand
The base material for resin-coated sand is silica sand, which is selected for its high purity and consistent grain size. This uniformity is essential for producing castings with precise dimensional tolerances. The resin used for coating can vary depending on the specific application requirements. Common types include
- Phenolic Resin Known for its excellent heat resistance and strength, making it suitable for high-temperature applications. - Urethane Resin Provides greater flexibility and toughness, ideal for intricate mold designs.
Additives may also be incorporated into the mixture to enhance its properties, such as improving flowability or reducing binding time.
Manufacturing Process
The production of resin-coated sand consists of several key steps
1. Preparation of Sand The silica sand is first cleaned and dried to remove any impurities that could affect the quality of the final product.
2. Coating Application The prepared sand is then mixed with the selected resin under carefully controlled conditions. The amount of resin and the method of application play a vital role in determining the performance characteristics of the sand.
what is resin coated sand
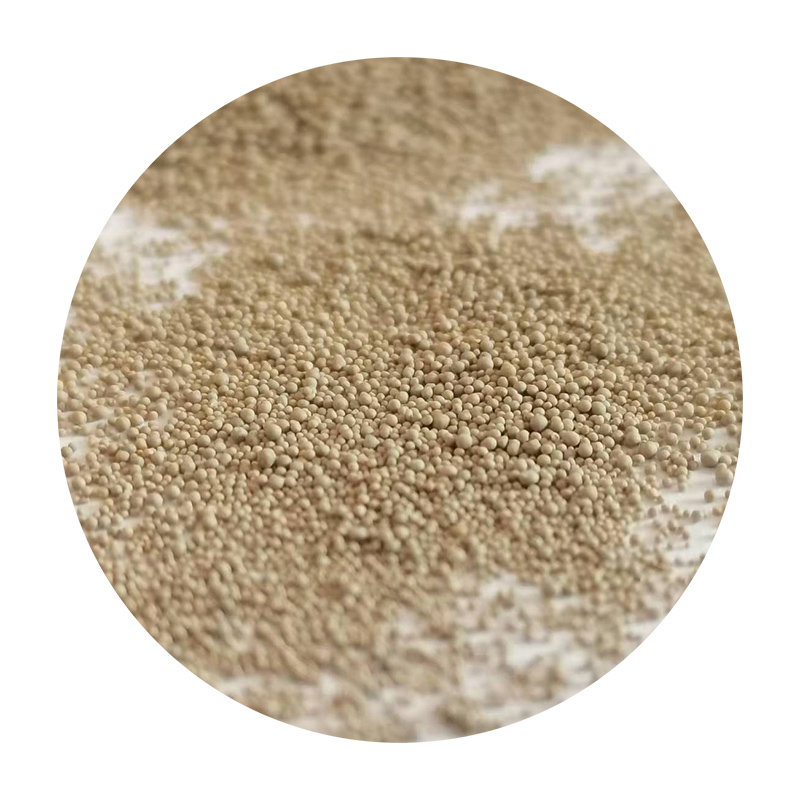
3. Curing After the sand has been coated, it undergoes a curing process, where heat is applied to harden the resin, ensuring a durable and stable coating on the sand grains. This step solidifies the bond between the sand and the resin, enhancing the overall strength and performance of the material.
4. Screening and Packaging The final product is screened to achieve the desired particle size distribution and then packaged for distribution to foundries and manufacturers.
Applications of Resin-Coated Sand
Resin-coated sand is predominantly used in foundries for producing metal castings. Its applications extend to various industrial sectors, including
- Automotive Industry Used for making engine blocks, transmission housings, and other intricate parts that require high precision. - Aerospace Industry Essential for producing components where safety and accuracy are paramount. - Oil and Gas Industry Utilized in the production of high-performance components that can withstand harsh environmental conditions.
Beyond these sectors, RCS is also becoming increasingly popular in the production of synthetic turf for sports fields, where its properties contribute to the durability and performance of athletic surfaces.
Advantages of Resin-Coated Sand
The use of resin-coated sand offers numerous benefits, including
- Improved Surface Finish Castings produced with RCS have superior surface qualities, reducing the need for additional machining. - High Dimensional Accuracy The precise nature of the material contributes to tighter tolerances, enabling the production of complex geometries.
- Reduced Casting Defects The uniform coating reduces the likelihood of defects such as sand adhesion and surface imperfections.
- Reusability RCS can often be reclaimed and reused multiple times, leading to cost savings and reduced waste.
In conclusion, resin-coated sand is a versatile and essential material in modern manufacturing processes. With its unique properties and benefits, it continues to support innovations across various industries, making it a vital component in the production of high-quality castings and components. Understanding its applications and advantages can help manufacturers make informed decisions to enhance their production capabilities.
Post time:មករា . 01, 2025 16:27
Next:रेत ढलाई के लिए 3डी प्रिंटिंग पैटर्न एक नवाचार का मार्गदर्शन