Types of Sand Used in Sand Casting
Sand casting is one of the oldest and most versatile metal casting methods, employed in various industries for producing components of diverse shapes and sizes. The process involves creating a mold from sand, into which molten metal is poured to form the desired object once cooled. The choice of sand is crucial for the success of the casting process, as different types of sand offer unique properties and advantages. In this article, we will explore the primary types of sand used in sand casting, highlighting their characteristics and applications.
1. Silica Sand
Silica sand is the most common type of sand used in sand casting. Composed primarily of silicon dioxide (SiO2), it possesses excellent melting properties and is highly resistant to heat. Silica sand is favored for its ability to retain shape and withstand the thermal shock associated with molten metal. It also provides good strength and permeability in the mold, allowing gases to escape during the casting process. However, its properties can vary based on grain size, shape, and purity. Fine-grained silica sand is ideal for intricate designs, while coarser grains are used for larger molds.
2. Green Sand
Green sand is a mixture of silica sand, clay, water, and various additives. It is called green because it is used in a moist state, which gives it a unique capability to maintain its shape and provide strength to the mold. The clay content in green sand acts as a binder, helping the sand grains adhere to one another. Green sand is particularly popular in foundries due to its low cost and reusability. It provides excellent surface finish and dimensional accuracy, making it suitable for casting a wide range of ferrous and non-ferrous metals.
3. Resin Sand
Resin sand is another type of molding sand that uses a resin binder instead of clay. This type of sand is characterized by its high strength and durability, which allows for the production of complex molds with thin walls and intricate details. Resin sand molds can withstand higher temperatures than traditional green sand molds, making them suitable for casting metals with high melting points. However, the process of preparing resin sand involves additional steps, such as mixing the sand with the resin and curing it, which can increase production costs.
types of sand used in sand casting
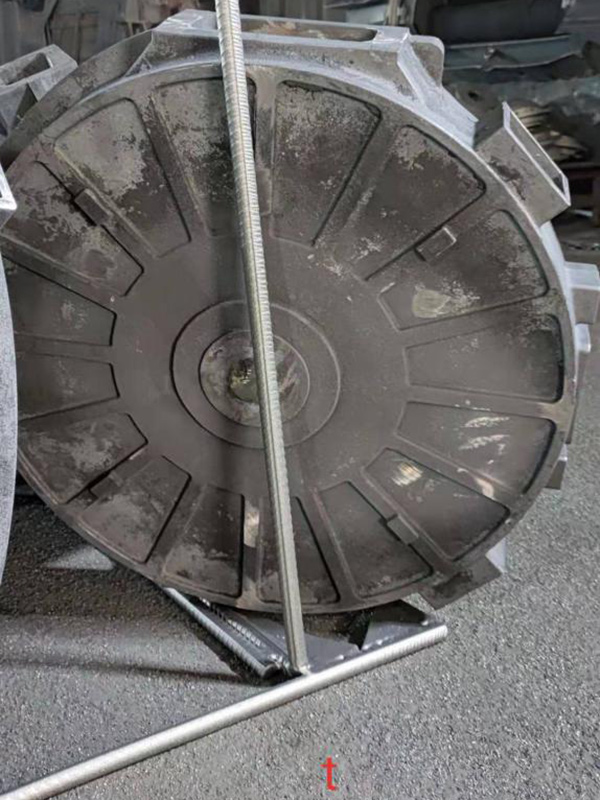
4. Oil-bonded Sand
Oil-bonded sand, also known as no-bake sand, is a mixture of sand, oil, and a catalyst (typically a hardener). This type of sand mold does not require moisture, making it less susceptible to defects caused by moisture-related issues. Oil-bonded sand provides excellent surface finish and dimensional accuracy, akin to resin sand, while still being suitable for heavier casting applications. It is particularly useful for producing molds and cores with a complex geometrical structure.
5. Shell Sand
Shell sand casting involves using a thin layer of a resin-coated sand to create molds. The sand is mixed with a thermosetting resin binder and heated, causing the resin to cure and form a hard shell around the mold. This method is ideal for production runs where high precision and excellent surface finish are required. Shell sand casts are consistent and detailed, making this type of sand particularly popular for complex parts in the automotive and aerospace industries.
6. Zircon Sand
Zircon sand is derived from the mineral zircon (zirconium silicate) and is valued for its high thermal stability and low thermal expansion. This makes it an excellent choice for casting metals that require high precision and accurate dimensions. Zircon sand is typically used in foundries that produce high-end applications, including turbine blades and aerospace components. While it is more expensive compared to silica sand, its superior properties can justify the cost in specific applications.
Conclusion
The choice of sand is vital in the sand casting process and influences the quality and precision of the final product. Each type of sand brings its unique properties and advantages to the casting process, ranging from traditional silica sand and green sand to more modern alternatives like resin sand and zircon sand. Understanding the characteristics of these sands enables manufacturers to select the appropriate material for their specific casting needs, ensuring efficient production and high-quality results. By leveraging the strengths of various sand types, foundries can continue to innovate and produce complex components essential for diverse industries.
Post time:វិច្ឆិកា . 27, 2024 22:12
Next:The History and Invention Timeline of Sand Casting Techniques