Steps of Sand Casting A Comprehensive Guide
Sand casting, an age-old metal-forming technique, has stood the test of time due to its versatility and cost-effectiveness. Employed in various industries, from automotive to aerospace, sand casting allows for the manufacturing of intricate shapes and sizable components. This article outlines the steps involved in the sand casting process, providing a clear understanding of how this method works.
1. Design and Pattern Making
The initial step in sand casting is the design of the component. Engineers must consider the part's geometry, dimensions, and material properties to create a functional design. Once the design is finalized, a pattern is constructed. Patterns can be made of wood, metal, or plastic and must accurately represent the desired final product. The pattern includes a slight oversize to account for the metal shrinkage during cooling.
2. Mold Preparation
The next step involves preparing the mold using sand. The most commonly used sand is a mixture of silica sand, clay, and water. The sand is compacted around the pattern in a flask, which is a container used for mold making. The pattern is then removed, leaving a cavity that mirrors the part's shape. Two halves of the mold are generally created, allowing for easier removal of the casting after the metal has cooled down.
3. Core Making (if necessary)
If the casting requires internal features or hollow sections, a core made from a similar sand mixture is produced. Cores are placed inside the mold cavity before pouring the metal to create the desired internal shape. Special care is taken to ensure the core is securely positioned and does not break apart during the metal pouring process.
4
. Melting the MetalOnce the mold is ready, it’s time to melt the metal. The type of metal used will depend on the application, but common choices include aluminum, iron, and bronze. The metal is heated in a furnace until it reaches a liquid state. The melting temperature varies based on the specific metal chosen, and it’s vital to maintain optimal conditions to ensure quality and reduce impurities in the final casting.
5. Pouring the Metal
steps of sand casting
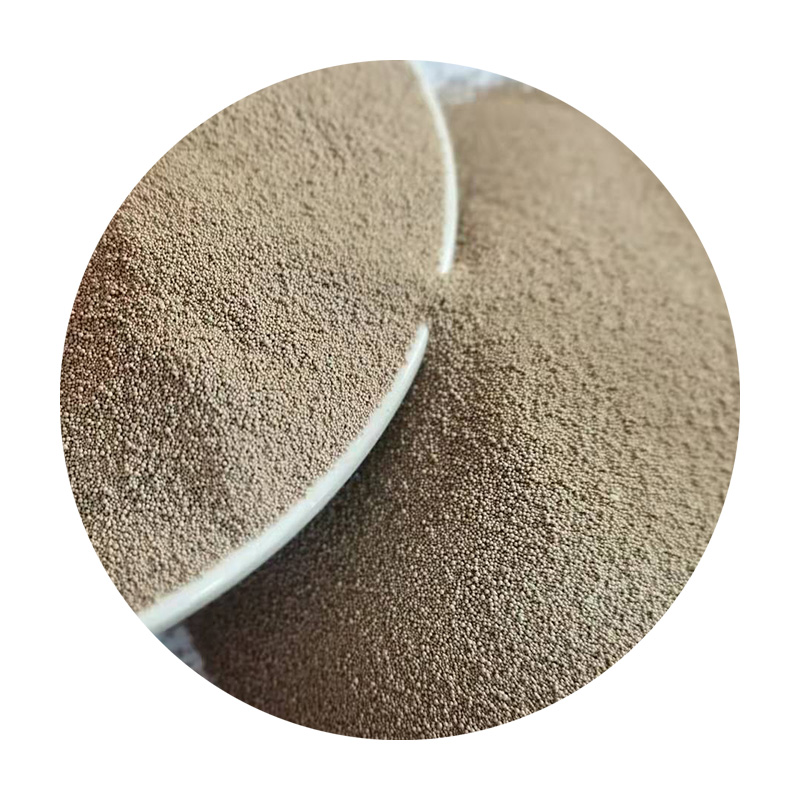
With the mold prepared and the metal melted, the next step is pouring the liquid metal into the mold cavity. This should be done carefully to avoid any spills or splashes that could cause defects. Pouring is typically performed from a ladle or special pouring apparatus designed to control the flow and speed of the molten metal. The metal fills the cavity, taking on the shape of the mold.
6. Cooling and Solidification
After the mold is filled, the liquid metal needs time to cool and solidify. The cooling rate may vary based on the metal and the thickness of the casting. As the metal cools, it transitions from liquid to solid, and a process called crystallization occurs, which ultimately affects the properties of the final product.
7. Mold Removal
Once the metal has completely cooled and solidified, the next step is to remove the mold. This can be done by breaking apart the sand mold, as sand casting is typically a single-use process. Care must be taken to avoid damaging the freshly cast part while separating it from the mold.
8. Cleaning and Finishing
After removal, the casting often requires cleaning to remove any sand residues from the surface. This can be done using sandblasting or other methods. Additionally, machining processes may be necessary to achieve tight tolerances or a smooth surface finish. Depending on the application, further finishing processes like polishing, coating, or welding might be applied.
9. Inspection and Testing
Finally, quality control is crucial in the sand casting process. The finished part undergoes inspection to check for dimensional accuracy, surface defects, and mechanical properties. Non-destructive testing methods may be employed to ensure the integrity of the casting without compromising its structure.
Conclusion
Sand casting is a fundamental manufacturing technique characterized by its straightforward process and adaptability to various applications. Understanding the steps involved—from design and pattern making to inspection—illustrates the intricacies of creating high-quality metal parts. This method remains a preferred choice for manufacturers aiming for efficiency and cost-effectiveness in production.
Post time:ធ្នូ . 15, 2024 04:09
Next:Innovations and Applications in Sand Casting Technology for Modern Manufacturing Processes