Steps in Sand Casting A Comprehensive Overview
Sand casting, a method that has been used for centuries, remains one of the most versatile and widely employed techniques in metalworking today. Its popularity can be attributed to its cost-effectiveness and ability to produce complex shapes. The process involves several critical steps, each playing a vital role in ensuring the final product's quality and accuracy. This article explores the essential steps in sand casting, from preparation to finishing.
1. Pattern Making
The first step in the sand casting process is the creation of a pattern. A pattern is a replica of the final product that will be cast and is usually made from materials such as wood, plastic, or metal. Patterns can be classified as solid, split, or expandable, depending on the complexity of the shape. The pattern must be slightly larger than the intended casting, as metal shrinkage occurs during cooling. The accuracy of the pattern directly influences the quality of the final casting.
2. Molding
Once the pattern is ready, the next step is molding. This involves creating a mold cavity in which the molten metal will be poured. Sand, often mixed with a binding agent like clay, is packed around the pattern to form the top and bottom halves of the mold. The sand mold must be compact enough to withstand the pressure of the molten metal while allowing for proper venting. Once the mold is set, the pattern is carefully removed, leaving a cavity that replicates the pattern's shape.
3
. Core MakingFor castings with internal features or complex geometries, cores are used. Cores are made from sand and are placed inside the mold to create voids or hollow sections in the casting. The core must be strong enough to withstand the molten metal but can be easily removed after the casting process. Cores can be created using similar techniques as mold-making and are essential for achieving intricate designs and internal shapes.
4. Pouring
steps in sand casting
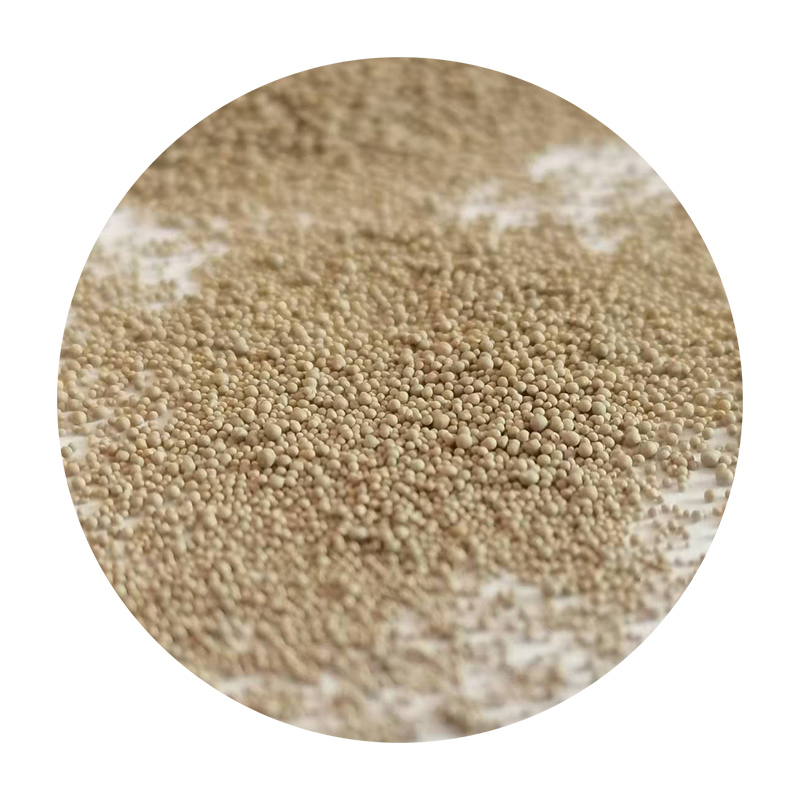
With the mold and cores in place, the next step is pouring the molten metal. This phase requires skill and precision, as any misstep can lead to defects in the casting. The metal is typically heated in a furnace until it reaches its melting point and then poured into the mold through a specially designed pouring cup. It’s crucial to control the temperature and pouring speed to ensure the metal fills the cavity evenly, avoiding issues like cold shuts or misruns.
5. Cooling
After pouring, the molten metal needs to cool and solidify. This cooling process can take anywhere from a few minutes to several hours, depending on the size and thickness of the casting. The cooling time must be carefully monitored to prevent defects such as warping or cracking. Once solidified, the mold can be broken open to reveal the casting.
6. Cleaning
Once the casting is removed from the mold, a cleaning process is necessary. This usually involves removing the sand, which may be accomplished through mechanical means or by shaking. Additional cleaning may involve removing any excess metal, such as gates or risers that were added during the pouring process. The final cleaning prepares the casting for inspection and further processing.
7. Finishing
The last step in the sand casting process is finishing. This may include machining, grinding, or polishing the casting to achieve the desired surface finish and dimensional accuracy. Additional treatments such as painting or coating may also be applied, depending on the application requirements. The finishing touches are essential to enhance the aesthetic appeal and performance of the final product.
Conclusion
Sand casting is a remarkable process that merges traditional techniques with modern technology, offering a reliable method for producing high-quality metal components. Understanding the steps involved—from pattern making to finishing—provides insight into the complexity and craftsmanship inherent in sand casting. With continuous advancements in materials and methodologies, sand casting remains a valuable process in various industries, from automotive to aerospace, demonstrating its timeless appeal and effectiveness in metal production. Whether producing small, intricate pieces or large, robust components, the fundamental steps of sand casting ensure that each casting meets the rigorous standards expected in today's manufacturing world.
Post time:ធ្នូ . 20, 2024 01:12
Next:sintered sand