Understanding Sand Used for Sand Casting
Sand casting is a widely used metal casting process that involves pouring liquid metal into a mold made of sand. This method is popular due to its simplicity, versatility, and cost-effectiveness. However, the quality of the sand used in the process is crucial, as it directly affects the final product's characteristics. In this article, we will delve into the types of sand used for sand casting, their properties, and the importance of selecting the right sand for specific applications.
Types of Sand Used in Sand Casting
1. Silica Sand By far the most commonly used sand in the sand casting process, silica sand is composed primarily of silicon dioxide (SiO2). Its high melting point and excellent molding characteristics make it an ideal choice for a variety of casting applications. Silica sand is available in different grain sizes, which can affect the permeability and surface finish of the final product.
2. Zircon Sand This sand is made from zirconium silicate and is used primarily for casting high-temperature alloys. Zircon sand has a high melting point and excellent thermal stability, which makes it suitable for producing castings that require a high degree of dimensional accuracy. Its low thermal expansion also reduces the risk of casting defects.
3. Olive Sand Also known as olivine sand, this type is composed of magnesium iron silicate. Olive sand is less common but has unique properties that make it suitable for certain applications, particularly in high-temperature environments. It is characterized by its ability to withstand thermal shock and has a low expansion rate, which is beneficial in preventing casting defects.
4. Clay Bonded Sand This is a mixture of sand and clay, which provides the necessary binding characteristics to hold the mold together. The most commonly used clay in sand casting is sodium bentonite, which has excellent binding capabilities. The clay helps to retain moisture, making it easier to mold and less prone to cracking.
5. Resin-Bonded Sand This type of sand is mixed with a thermosetting resin, which cures to form a durable mold. Resin-bonded sand offers superior surface finish and dimensional accuracy compared to traditional sand casting methods. It is often used in applications where precision is critical, such as in the automotive and aerospace industries.
Properties of Casting Sand
The selection of sand for casting is based on several key properties
sand used for sand casting
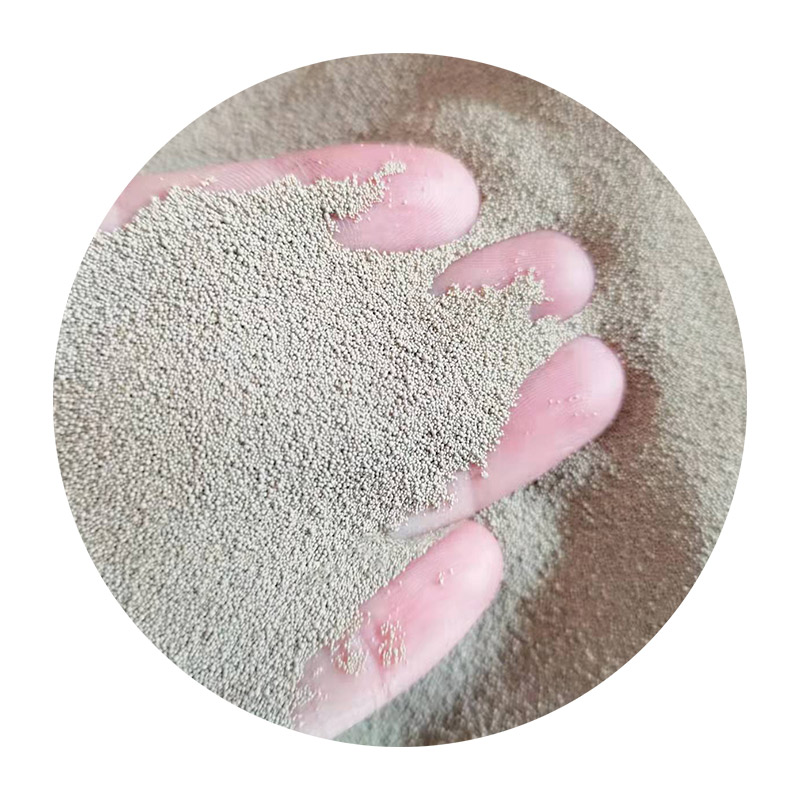
- Grain Size The size of the sand grains influences the mold's permeability and surface finish. Finer grains tend to produce smoother surfaces, while coarser grains provide better permeability.
- Shape The shape of the sand particles affects the flowability of the sand mixture and its ability to pack tightly. Rounded grains pack more efficiently than angular grains.
- Moisture Content The moisture in the sand mixture must be carefully controlled, as too much moisture can lead to defects in the mold, while too little can cause the mold to crack.
- Compacting Ability Good casting sand should be able to be compacted easily to achieve the necessary strength for the mold.
Importance of Selecting the Right Sand
Choosing the right sand for sand casting is critical for several reasons. The quality of the sand affects the final product's mechanical properties, surface finish, and dimensional accuracy. Using the wrong type of sand can lead to defects such as sand inclusions, surface imperfections, and dimensional inaccuracies.
Additionally, the properties of the sand can influence the casting process itself. For example, sands with higher thermal stability can better handle the heat of molten metal, reducing the risk of mold failure. Furthermore, ensuring that the sand has the right grain size and shape can improve the flow of the molten metal, leading to better filling of the mold and improved casting quality.
Conclusion
In conclusion, the sand used for sand casting plays a vital role in determining the success of the casting process. Understanding the different types of sand, their properties, and the importance of selecting the right sand for specific applications is essential for achieving high-quality castings. As industries continue to evolve and require more precise and reliable castings, ongoing research and development in sand materials will remain a critical area of focus in the field of foundry technology.
Post time:តុលា . 12, 2024 09:20
Next:sand casting manufacturers