Sand Preparation in Foundry An Essential Process for Quality Casting
The foundry industry plays a pivotal role in manufacturing components across various sectors, from automotive to aerospace. A crucial aspect of foundry operations is sand preparation, an often overlooked but essential process that directly influences the quality of castings produced. In this article, we will explore the significance of sand preparation, the types of sand used, and the various stages involved in preparing sand for successful metal casting.
Importance of Sand Preparation
Sand serves as the primary mold material in foundries, and its preparation is vital for ensuring the accuracy and reliability of the final product. Properly prepared sand ensures that molds can hold their shape under the weight of molten metal, allows for even heat distribution, and helps achieve fine surface finishes. Moreover, the characteristics of the sand mix affect the thermal properties, permeability, and strength of the molds. This ultimately influences the casting's dimensional accuracy and integrity, diminishing the chances of defects like sand inclusions or misalignments.
Types of Sand Used in Foundries
While several types of sand can be used in foundries, green sand is the most common. This sand consists of a mixture of silica sand, clay, and water, which creates a mold that can withstand both the pouring of molten metal and the subsequent cooling phase. Other types of sand employed include resin-bonded sand, silica sand, and investment casting sand, each tailored for specific casting processes and requirements.
1. Green Sand Made from silica sand and about 2-10% clay, this sand is cost-effective and easily moldable. Its properties allow for good surface finishes, making it ideal for many types of castings.
2. Resin-Bonded Sand This type uses a chemical binder to form molds. It offers a higher strength and finer detail than green sand but is more expensive and requires a longer preparation time.
sand preparation in foundry
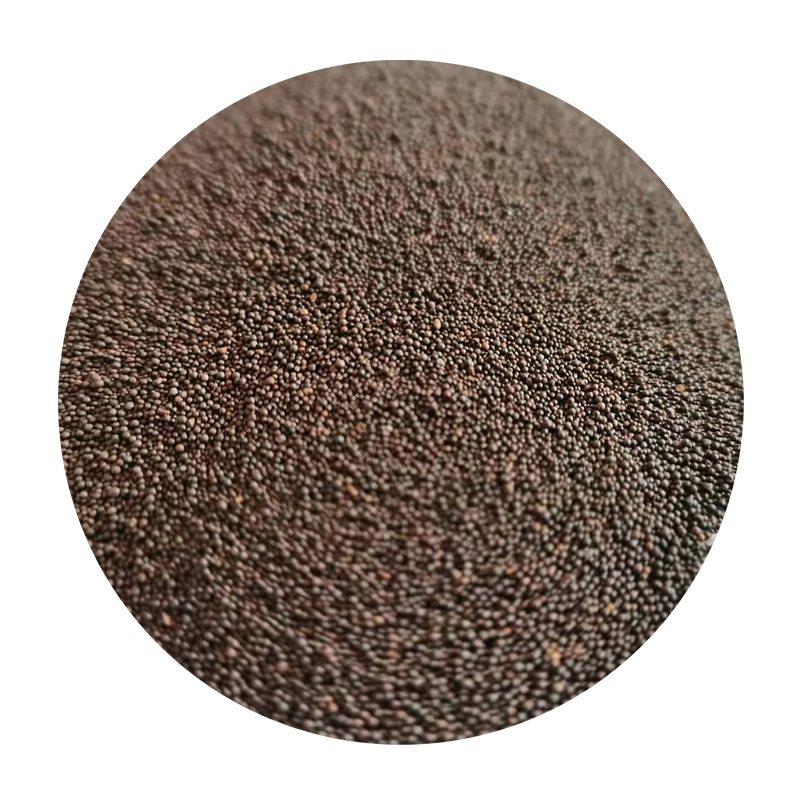
Stages of Sand Preparation
The sand preparation process involves several critical steps to ensure the sand achieves the right properties for casting
1. Sand Molding The first step focuses on acquiring the appropriate sand type according to the casting requirements. The raw sand is screened to remove impurities and ensuring uniformity in grain size.
2. Additives and Blending After screening, additives like clay, water, and various chemical binders are introduced to the sand. This blending process is crucial for achieving the desired cohesiveness and workability of the sand mix.
3. Moisture Control Water content plays a significant role in the quality of the sand mold. Excess moisture can lead to defects in the casting process, so careful monitoring and adjustment are necessary.
4. Sand Recycling A sustainable aspect of modern foundries involves recycling used sand. After casting, the sand is collected, cleaned, and reprocessed to reduce waste and costs, thereby promoting environmental responsibility.
5. Quality Control Finally, thorough testing and analysis of the prepared sand are conducted. Tests may include assessing the sand's moisture content, grain size distribution, and bonding strength to ensure it meets industry standards.
Conclusion
In summary, sand preparation is an indispensable process in the foundry industry that directly impacts the quality and performance of castings. By understanding the types of sand available, the preparation stages involved, and the importance of meticulous quality control, foundries can produce superior products that meet the stringent demands of various applications. As the industry continues to evolve, innovative techniques and practices in sand preparation will likely lead to even greater efficiencies and improved casting quality in the future.
Post time:ធ្នូ . 22, 2024 12:19
Next:3Dプリントのサンディングとコツについてします