Exploring the World of Sand Foundries
Sand foundries play a vital role in the manufacturing sector, providing essential services for creating metal parts through the casting process. This method has been utilized for centuries, and its enduring relevance speaks volumes about its efficiency and adaptability. In this article, we will delve into what sand foundries are, their operational processes, advantages, challenges, and their future in the evolving industrial landscape.
Understanding Sand Foundries
A sand foundry is a facility where metal casting is performed using sand as the primary molding material. The process involves creating a mold from a mixture of sand, clay, and water, into which molten metal is poured to form solid components once cooled. Castings produced through sand foundries can vary in size, shape, and complexity, making this process suitable for various industries, including automotive, aerospace, and general manufacturing.
The Sand Casting Process
The sand casting process consists of several key steps
1. Pattern Making The first step involves creating a pattern that replicates the final product. Patterns can be made from various materials, such as wood, metal, or plastic, and are often slightly larger than the intended casting to account for shrinkage during cooling.
2. Mold Creation Using the pattern, foundry workers will create a mold by packing a sand mixture around it. The sand is typically mixed with a binder (often clay) to help it hold its shape. Once the mold is created, it is separated into two halves (the cope and the drag), allowing for the removal of the pattern.
3. Melting The next stage involves melting the desired metal, which can include ferrous metals (like iron and steel) and non-ferrous metals (such as aluminum and copper). The molten metal is usually heated in a furnace until it reaches a liquid state.
4. Pouring Once the metal is molten, it is poured into the pre-prepared mold. The precision of this step is crucial, as the molten metal must fill the mold evenly to avoid defects.
5. Cooling and Shakeout After pouring, the molten metal is allowed to cool and solidify. Once it has cooled sufficiently, the sand mold is broken away, revealing the cast part.
sand foundry
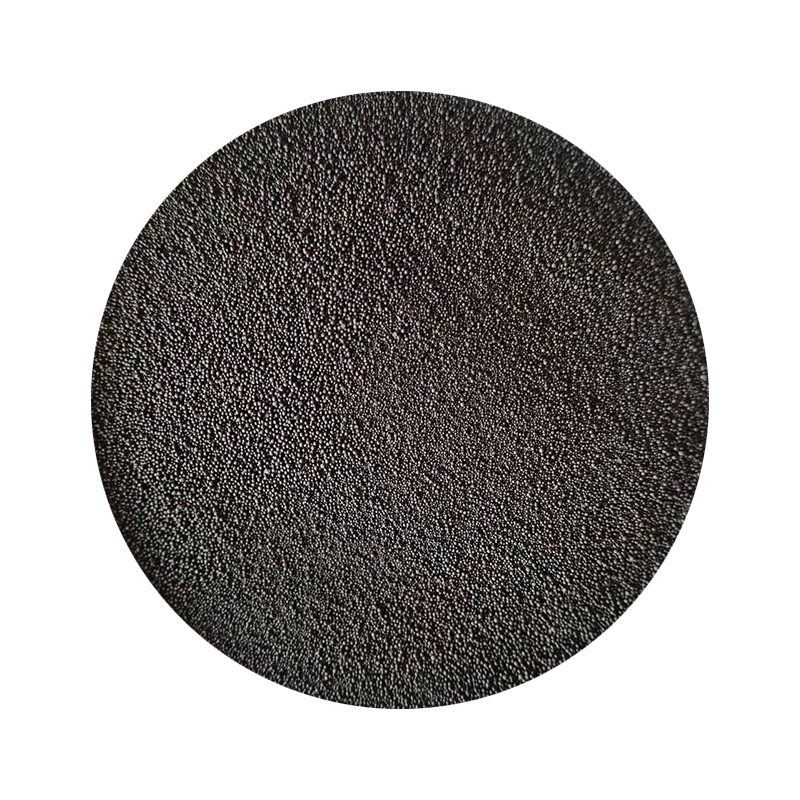
6. Finishing The final step involves cleaning and finishing the casting. This may include trimming excess material, polishing surfaces, and performing inspections to ensure quality standards.
Advantages of Sand Casting
Sand foundries provide several advantages that contribute to their popularity
- Versatility Sand casting is suitable for a wide range of metals and is capable of producing intricate shapes and large components. - Cost-Effectiveness The materials used (sand and clay) are relatively inexpensive, and the manufacturing process is conducive to batch production, making it economical for both small and large runs. - Reusability of Sand After the casting process, sand can often be reclaimed and reused, reducing waste and material costs.
Challenges Facing Sand Foundries
Despite their advantages, sand foundries face several challenges
- Environmental Regulations The use of sand and binding agents can lead to environmental concerns, especially regarding dust and emissions. Foundries must comply with stringent regulations and adopt sustainable practices. - Labor-Intensive Processes The manual nature of sand casting can result in high labor costs and variable quality. Many foundries are exploring automation to improve efficiency. - Technological Advancements As industries evolve, the demand for precision and quality increases. This pushes sand foundries to adopt new technologies, such as computer-aided design (CAD) and 3D printing, to stay competitive.
The Future of Sand Foundries
Looking ahead, sand foundries are likely to undergo significant transformations. The integration of digital technologies will enable better design capabilities and precision in the casting process. Additionally, as industries shift towards sustainable practices, foundries will need to invest in environmentally friendly processes and materials.
In conclusion, sand foundries remain a cornerstone of the manufacturing world. Their ability to produce complex metal parts efficiently and cost-effectively ensures their relevance in today’s industrial ecosystem. By addressing challenges and embracing technological advancements, sand foundries can continue to thrive and adapt in an ever-evolving market.
Post time:វិច្ឆិកា . 08, 2024 04:19
Next:Exploring the Art and Science of Sand Casting Techniques in Metalworking Industry