Sand Casting Technology An Overview
Sand casting, also known as sand molded casting, is one of the oldest and most versatile casting methods used in metallurgy today. Its process involves creating a mold from a mixture of sand, water, and a binding agent; this mold is then filled with molten metal to create complex metallic parts. The inherent advantages of sand casting technology have made it a popular choice across industries, from automotive to aerospace and even art.
The Process of Sand Casting
The sand casting process begins with the creation of a pattern, which is a replica of the final product to be produced. This pattern is usually made from materials like wood, plastic, or metal and is designed slightly larger than the desired finished part to account for metal shrinkage during cooling.
Once the pattern is made, it is placed in a mold box, and fine sand mixed with a bonding agent (like clay) and water is packed around the pattern. The sand mixture is compacted to ensure it holds its shape. After the mold is formed, the pattern is removed, leaving a cavity in the shape of the desired part. This process can be done using two halves (cope and drag) to create a complete mold.
After creating the mold, molten metal is poured into the cavity. The metal can be a variety of alloys, including aluminum, iron, or bronze. Once the metal cools and solidifies, the mold is broken apart, and the casting is removed. The final step involves cleaning and finishing the casting to achieve the required surface quality and dimensions.
Advantages of Sand Casting
One of the primary advantages of sand casting technology is its ability to produce large objects and complex shapes with relative ease. Unlike other casting processes, sand casting can accommodate a wide range of sizes, making it an ideal choice for both small and large-scale production.
sand casting technology
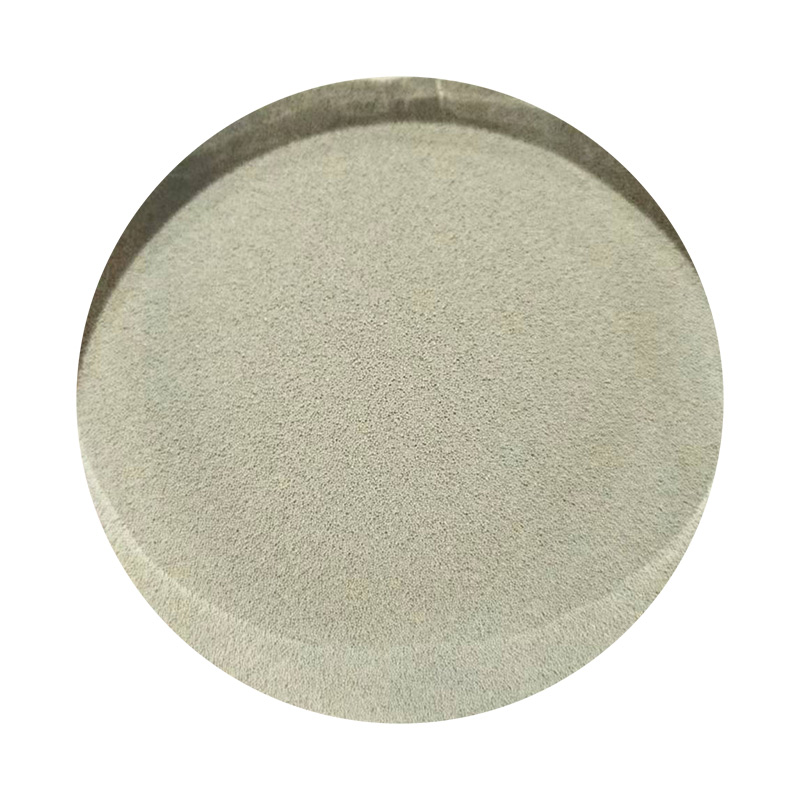
Another benefit is the cost-effectiveness of the materials used. Sand is inexpensive and widely available, significantly reducing the overall production costs. Additionally, the sand molds can often be reused multiple times, further enhancing the economic efficiency of the process.
Sand casting also offers a high degree of design flexibility. Manufacturers can create intricate designs that would be challenging or impossible to achieve with other fabrication methods. This flexibility extends to various industries, allowing for custom solutions tailored to specific applications.
Limitations and Innovations
Despite its many advantages, sand casting does have some limitations. The surface finish of sand cast parts is not as smooth as those produced by other casting methods, such as investment casting. Additionally, achieving tight tolerances can be challenging, often requiring additional machining.
However, advancements in technology are addressing these limitations. Innovations such as 3D printing and improved sand mixtures have enhanced the precision and surface quality of sand castings. Moreover, the adoption of simulation software allows engineers to predict potential issues in the casting process, leading to better designs and less material waste.
Conclusion
In summary, sand casting technology remains a fundamental and crucial part of metalworking due to its versatility, cost-effectiveness, and ability to produce complex shapes. As technology continues to evolve, sand casting is likely to undergo further enhancements, maintaining its relevance in modern manufacturing. This enduring method not only plays a crucial role in traditional industries but also paves the way for innovative applications in the future, showcasing the blend of age-old techniques and contemporary technology.
Post time:ធ្នូ . 19, 2024 03:43
Next:ceramic sand price