Sand Casting Techniques An Overview
Sand casting, also known as sand mold casting, is one of the oldest and most versatile metal casting techniques. It involves creating molds from a mixture of sand and a bonding agent to produce complex parts used in various industries, including automotive, aerospace, and machinery. This article will explore the fundamentals of sand casting, its advantages, disadvantages, and the various techniques employed in this casting process.
The Basics of Sand Casting
The sand casting process begins with the creation of a mold. This is typically done by packing a mixture of sand with a binding agent around a pattern. The pattern, usually made of metal, plastic, or wood, replicates the desired shape of the final product. Once the mold is formed, the pattern is removed, leaving a cavity that will receive the molten metal.
The next step involves pouring molten metal into the mold cavity. The temperature of the molten metal varies depending on the type of metal being used. Common materials in sand casting include aluminum, iron, copper alloys, and stainless steel. After the metal has cooled and solidified, the mold is broken apart to release the cast component.
Techniques in Sand Casting
There are several techniques employed in sand casting, each offering its distinct advantages
1. Green Sand Casting This is the most traditional method, utilizing a mixture of sand, clay, and water. The sand is pliable and can be easily shaped, making it suitable for creating intricate designs. Green sand casting is ideal for low to medium production runs.
2. Dry Sand Casting In this technique, molds are made using sand mixed with a binding agent that requires a curing process. This results in a stronger mold that can withstand the high temperatures of molten metal. Dry sand casting is suitable for high-production environments where durability is essential.
sand casting techniques
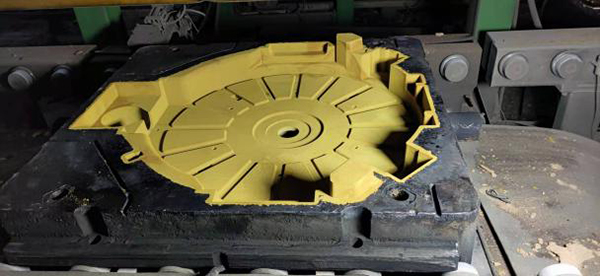
3. No-Bake Casting This involves a chemical binding agent which hardens when mixed with sand, eliminating the need for moisture. It allows for greater dimensional accuracy and is often used in large-scale production, where precision is key.
4. Lost Foam Casting A pattern made of polystyrene foam is used in this method. The foam evaporates when molten metal is poured, creating a mold in the shape of the foam pattern. This technique provides excellent surface finish and dimensional accuracy, allowing for more complex geometries.
5. Shell Molding This process involves creating a thin shell mold using a mixture of sand and resin. The shell is formed by heating the mold to harden the resin. Shell molding offers better surface finish and can achieve higher tolerances compared to traditional sand casting.
Advantages and Disadvantages
One of the primary advantages of sand casting is its versatility. It can accommodate a wide range of metals and allows for complex shapes and designs. The materials used for the molds are relatively inexpensive, making it cost-effective for small to medium-sized production runs.
However, sand casting has its drawbacks. The surface finish may not be as smooth as other casting methods. Additionally, the dimensional tolerance is generally lower than that of processes like injection molding or die casting. Furthermore, the sand molds are typically single-use, leading to additional waste and environmental concerns.
Conclusion
Sand casting remains a vital method of manufacturing across various industries due to its cost-effectiveness and adaptability to different materials. With advancements in technology and techniques, the sand casting process continues to evolve, offering improved precision, efficiency, and sustainability. For engineers and manufacturers, understanding these techniques is crucial in selecting the appropriate method for their specific needs, ensuring high-quality final products that meet the demands of modern production.
Post time:វិច្ឆិកា . 04, 2024 19:52
Next:Benefits and Drawbacks of Using Sand Casting in Manufacturing Processes