Sand Casting Technique An Overview
Sand casting, one of the oldest metal casting techniques, has been a fundamental process in metalworking for centuries. It is a versatile and economical method used to create complex shapes and intricate designs, making it a popular choice in various industries such as automotive, aerospace, and art.
The Process of Sand Casting
The sand casting process begins with the creation of a mold. Molds are typically made from a mixture of sand, a binding agent, and water, creating a material known as green sand. This mixture is packed tightly around a model of the object to be cast, which is often made of metal or another durable material. The model is removed after the mold is formed, leaving a cavity in the shape of the desired part.
Once the mold is prepared, it is then subjected to further treatments, such as drying or hardening, depending on the specific requirements of the casting. After the mold is finalized, molten metal is poured into the cavity. The metal, typically aluminum, iron, or steel, must be heated above its melting point to ensure it flows smoothly into the mold.
After the metal has cooled and solidified, the mold is broken apart to reveal the cast object. This object may require additional processing, such as grinding, polishing, and machining, to achieve the final shape and finish desired.
Advantages of Sand Casting
One of the primary advantages of sand casting is its cost-effectiveness. The materials used are inexpensive, and molds can be recreated relatively easily. The process is also highly adaptable, allowing for various shapes and sizes, making it suitable for both small production runs and large-scale manufacturing.
sand casting technique
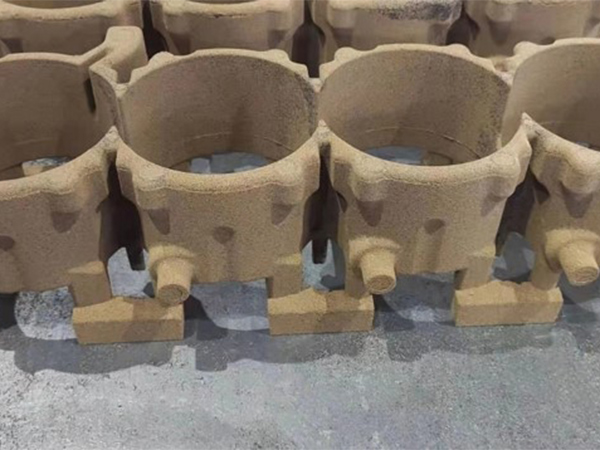
Additionally, sand casting can accommodate a wide range of metal types, providing flexibility in material selection. This method is particularly advantageous for producing large or heavy parts that would be challenging to create using other casting methods.
Another benefit of sand casting is its capability to produce complex geometries. The sand mold can be shaped into intricate designs that might be difficult or impossible to achieve with other manufacturing processes. This makes it an excellent choice for artistic applications and custom metalwork.
Challenges and Considerations
Despite its advantages, sand casting does come with some challenges. The quality of the final product can be affected by factors such as sand quality, mold stability, and pouring temperature. Additionally, the sand casting process can result in surface defects, such as sand inclusions and rough textures, which may require significant post-processing to rectify.
Moreover, the time it takes to create and prepare molds can be prolonged, especially for intricate designs. This aspect makes sand casting less suitable for high-speed production needs where rapid turnaround times are essential.
Conclusion
In conclusion, sand casting is a time-honored technique that continues to play a vital role in modern manufacturing. Its adaptability, cost-effectiveness, and ability to create complex shapes make it a go-to method for a wide range of applications. However, manufacturers must also consider the associated challenges and invest in quality control measures to ensure optimal results. As technology advances, the sand casting technique is likely to evolve, incorporating new materials and processes that further enhance its utility in the manufacturing landscape.
Post time:វិច្ឆិកា . 25, 2024 07:38
Next:Tips for Sanding and Smoothing 3D Printed Surfaces Effectively