Understanding Sand Castings A Key Manufacturing Process
In the realm of manufacturing, sand casting remains one of the oldest and most versatile processes utilized in creating intricate and durable metal parts. This time-tested method has been adopted across various industries, ranging from automotive to aerospace, owing to its efficiency, cost-effectiveness, and ability to produce complex shapes. In this article, we will delve deeper into sand casting, exploring its process, advantages, applications, and the role of sand casting manufacturers in the modern manufacturing landscape.
The Sand Casting Process
Sand casting involves several key steps, beginning with the creation of a mold. The mold is typically made from sand mixed with a binding agent that allows it to hold its shape. This mixture is packed around a pattern, which is a replica of the part to be produced. Once the pattern is removed, it leaves a hollow cavity in the sand that defines the shape of the final product.
The next stage is melting the metal, which can be done using various heating methods depending on the type of metal being used, including induction furnaces and electric arc furnaces. Common metals for sand casting include aluminum, bronze, and iron. Once the metal reaches its melting point, it is poured into the prepared sand mold.
After the metal has cooled and solidified, the mold is broken apart to retrieve the newly formed casting. The casting often requires some finishing work, such as trimming excess material, sanding, or machining, to achieve the desired surface finish and specifications.
Advantages of Sand Casting
1. Cost-Effective One of the primary advantages of sand casting is that it is relatively inexpensive compared to other casting methods. The materials used, such as sand and binder, are readily available and affordable.
2. Versatility Sand casting can produce a wide variety of shapes, making it an excellent choice for both simple and complex designs. It is particularly useful for creating large parts that might be challenging to produce with other methods.
4. Scalability Sand casting is suitable for both low and high-volume production runs. Whether a company needs a single prototype or thousands of parts, sand casting can be adjusted to meet production demands.
sand castings manufacturer
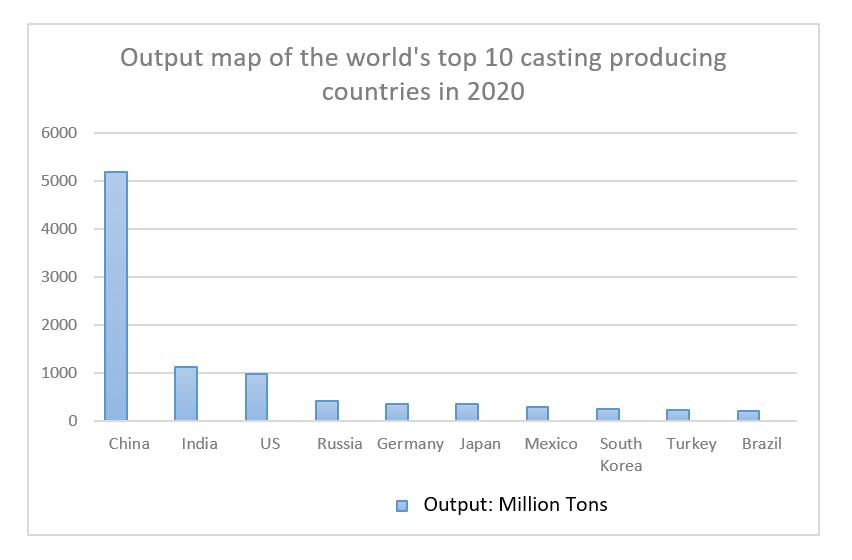
Applications of Sand Castings
The applications of sand castings are vast, with industries leveraging this process for numerous components. Some common applications include
- Automotive Components Engine blocks, transmission cases, and housing for various automotive parts are often produced using sand casting due to their durability and the complex shapes often required.
- Aerospace Parts The aerospace industry uses sand casting to create critical components like turbine housings and structural parts, where precision and reliability are essential.
- Marine Applications Parts for boats, ships, and various marine equipment are frequently manufactured using sand casting, providing the strength needed to withstand harsh environments.
- Industrial Equipment Many manufacturing machines and industrial tools utilize sand-cast components for their durability and cost-effectiveness.
The Role of Sand Casting Manufacturers
Sand casting manufacturers play a crucial role in ensuring the quality and precision of the cast parts produced. These manufacturers invest in modern technologies and skilled labor to optimize the sand casting process. Many employ computer-aided design (CAD) software to enhance the accuracy of mold designs and streamline production.
A reputable sand casting manufacturer also adheres to strict quality control measures, often following industry standards to ensure that each casting meets specifications. They typically offer services that extend beyond casting, such as machining, surface treatment, and finishing, providing clients with end-to-end solutions that simplify the manufacturing process.
Conclusion
Sand casting remains a fundamental method in the manufacturing sector due to its practicality and versatility. With a wide range of applications and benefits, it is a preferred choice for numerous industries seeking high-quality cast parts. As technology continues to advance, sand casting manufacturers are well-positioned to meet the evolving demands of the market, ensuring that this classic casting method remains relevant in today’s high-tech world.
Post time:វិច្ឆិកា . 24, 2024 23:52
Next:buy sand casting