Sand Casting Mass Production An Overview
Sand casting is one of the oldest and most popular methods of metal casting, widely utilized in various industries for producing a multitude of components. This technique involves pouring molten metal into a mold made from sand, which hardens to create a solid object. Sand casting mass production has gained significant traction due to its cost-effectiveness, versatility, and ability to produce complex shapes with high precision. In this article, we will explore the intricacies of sand casting mass production, including its advantages, the process involved, and its applications.
The Process of Sand Casting
The sand casting process begins with the creation of a pattern, which is a replica of the final product. This pattern is generally made from materials like wood, plastic, or metal, and is carefully designed to account for the shrinkage of the metal as it cools. Once the pattern is ready, the next step involves making the mold. This is achieved by packing sand, often mixed with binders, around the pattern in a two-part mold. The sand is compressed to create a solid form that can withstand the pressure of the molten metal.
After the mold is prepared, the pattern is removed, leaving a cavity in the shape of the desired component. The next phase is to pour the molten metal into the mold cavity. The metal is heated to its melting point in a furnace, and it is poured through a sprue into the mold, filling the cavity. Once the metal cools and solidifies, the mold is broken apart to reveal the casting. The final step involves cleaning and finishing the casting to remove any imperfections and ensure it meets the required specifications.
Advantages of Sand Casting Mass Production
One of the primary advantages of sand casting is its adaptability. This method can accommodate a wide range of metal types, including aluminum, iron, and bronze, making it suitable for various applications. Additionally, sand casting allows for the creation of parts with intricate geometries that may be challenging to produce using other methods.
Cost-effectiveness is another significant benefit. The materials used for sand molds, primarily sand and binder, are inexpensive and readily available. Moreover, the ability to produce large quantities of parts simultaneously helps to lower production costs, making sand casting an attractive option for mass production.
sand casting mass production
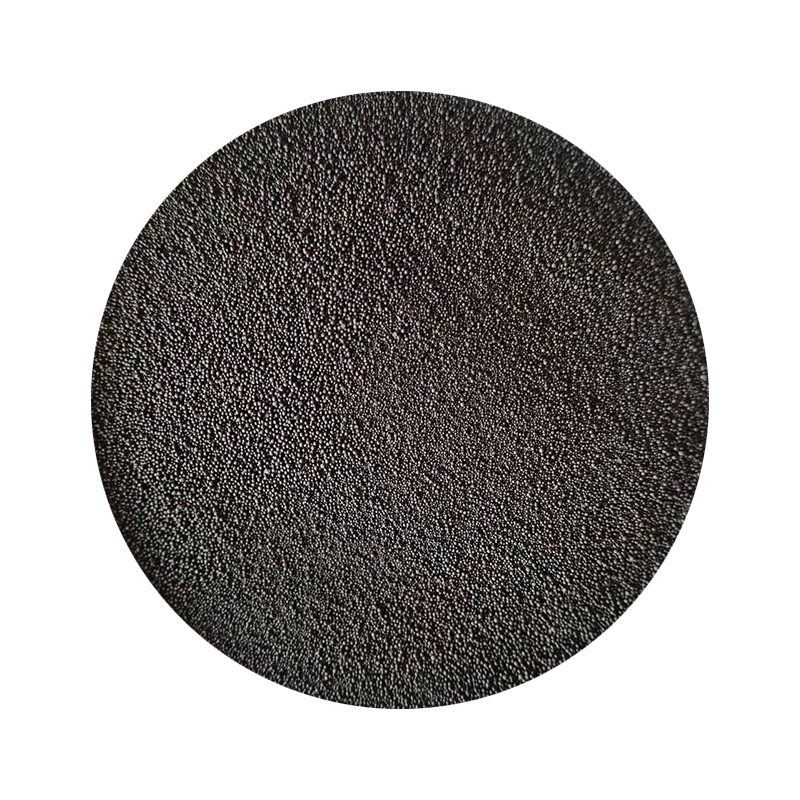
Furthermore, sand casting is less restrictive in terms of the size of components that can be produced. It can handle both small parts and large structures, making it versatile for numerous industries, including automotive, aerospace, and construction.
Applications of Sand Casting
The applications of sand casting span across various sectors, reflecting its broad utility. In the automotive industry, sand casting is often employed to produce engine blocks, transmission housings, and other critical components. The process's ability to create intricate designs aids in weight reduction and enhances the performance of vehicle parts.
In the aerospace sector, sand casting provides a solution for producing lightweight yet durable parts, contributing to advancements in aircraft design and efficiency. Components such as landing gear and turbine housings are often manufactured using this technique.
Additionally, the construction industry benefits from sand casting in producing structural components and machinery parts required for building projects. Its flexibility in producing both high-performance and heavy-duty items makes it invaluable in various construction applications.
Conclusion
In conclusion, sand casting mass production is a time-tested method that offers numerous advantages, including versatility, cost-effectiveness, and the ability to produce complex shapes. As industries continue to demand high-quality and efficiently manufactured components, sand casting will remain a pertinent choice for manufacturers worldwide. Its wide-ranging applications, from automotive to aerospace and construction, underscore its significance in the modern manufacturing landscape. As technology advances, innovations in sand casting processes and materials are likely to enhance its effectiveness, ensuring its continued relevance in the manufacturing sector.
Post time:វិច្ឆិកា . 24, 2024 14:57
Next:industrial sand casting