Sand Casting Foundries An Overview of the Process and Its Benefits
Sand casting is one of the oldest and most versatile manufacturing processes, widely used in foundries around the world. This method involves pouring molten metal into a sand mold to create various metal components. The flexibility and cost-effectiveness of sand casting make it a popular choice for many industries, from automotive to aerospace and beyond. This article delves into the sand casting process, the types of foundries, and the advantages and challenges associated with this method.
The Sand Casting Process
The sand casting process begins with creating a mold. The mold is typically made from a mixture of sand, clay, and water, which gives it the ability to hold its shape. The sand is packed tightly around a pattern, which is a replica of the object to be cast. Once the mold is formed, the pattern is removed, leaving a cavity in the shape of the desired part.
Next, molten metal is poured into the cavity. The melting point of the metal varies depending on the material; common metals used in sand casting include aluminum, bronze, iron, and steel. Once the metal has cooled and solidified, the mold is broken apart to reveal the casting. The final step involves cleaning and finishing the metal piece, which may include processes like machining, polishing, or surface treatment to meet specific requirements.
Types of Sand Casting Foundries
There are two main types of sand casting foundries green sand foundries and resin-bonded sand foundries
.- Green Sand Foundries These foundries use “green sand,” a mixture of sand, clay, and water. The term green does not refer to the color but rather the moisture content of the sand. Green sand molds offer excellent collapsibility, allowing for easy removal of the casting. They are typically used for producing larger, less complex parts, making them suitable for heavy industries.
- Resin-Bonded Sand Foundries In this type, the sand is coated with a thermosetting resin, which is activated by heat. This method allows for higher precision and finer details compared to green sand casting. Resin-bonded sand foundries are commonly used for intricate parts required in applications such as aerospace, where accuracy is crucial.
sand casting foundries
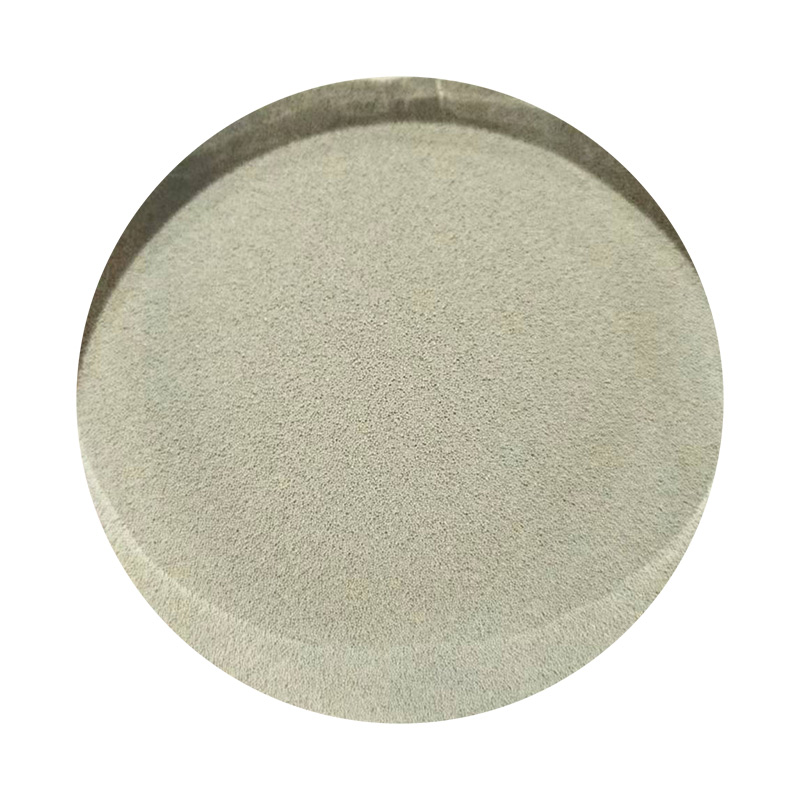
Benefits of Sand Casting
One of the primary advantages of sand casting is its versatility. It can accommodate a wide variety of metals and is suitable for small batches as well as large production runs. Additionally, sand casting can produce complex shapes and intricate designs that might be challenging to achieve with other manufacturing methods.
Cost-effectiveness is another significant benefit. The materials used in sand casting are relatively inexpensive compared to other molding processes. Furthermore, the ability to reuse sand for multiple casting cycles enhances its sustainability and reduces waste. This makes sand casting an economically viable option for manufacturers aiming for high productivity at lower costs.
Challenges of Sand Casting
Despite its benefits, sand casting does come with challenges. The quality of the mold directly influences the final product; imperfections in the mold can lead to defects in the casting, such as porosity or dimensional inaccuracies. Achieving the desired surface finish may require additional machining and finishing processes, which can add to the overall production cost and time.
Moreover, controlling the cooling rate of the molten metal is crucial. Uneven cooling can lead to internal stresses and distortions in the final casting, affecting its strength and durability.
Conclusion
In summary, sand casting foundries play a pivotal role in modern manufacturing by providing a reliable and flexible method for producing metal components. With its ability to create complex shapes and accommodate various metals, sand casting remains a preferred choice for many industries. While challenges in mold quality and cooling control exist, advancements in technology and processes continue to enhance the capabilities and efficiency of sand casting. As industries evolve, sand casting foundries will undoubtedly adapt and innovate, ensuring their place in the future of manufacturing.
Post time:ធ្នូ . 19, 2024 06:02
Next:Innovative Techniques in 3D Printing with Sand for Advanced Applications