Sand Casting Foundries An In-Depth Look
Sand casting is one of the oldest and most versatile metal casting processes used in the manufacturing industry. Its significance lies not only in its historical roots but also in its continued application across various sectors, including automotive, aerospace, and consumer goods. Sand casting foundries are essential facilities where this process takes place, transforming raw materials into complex metal components.
The sand casting process involves several steps, starting with the creation of a mold. Foundries primarily use silica sand because of its excellent heat resistance and ability to retain shape. The sand is mixed with a binding agent, usually clay, and water to create a moldable mixture. Once the mold design is established, the sand mixture is packed around a pattern that represents the desired final product. After the mold is formed, the pattern is removed, leaving a cavity where molten metal will be poured.
One of the key advantages of sand casting is its flexibility in producing large and intricate parts. The process can accommodate a wide range of metal compositions, including aluminum, copper, iron, and steel, making it highly adaptable to different requirements. Moreover, sand molds can be produced quickly and at a lower cost, making them ideal for low to medium production runs.
sand casting foundries
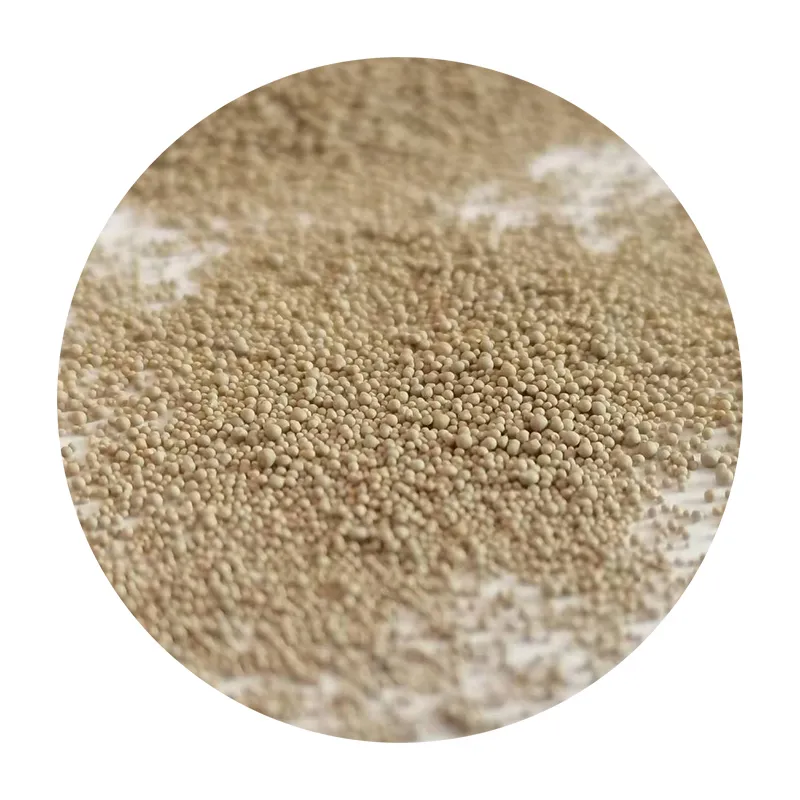
Quality control in sand casting foundries is critical to ensure that the final products meet industry standards. Foundries employ a range of techniques to monitor and improve the casting process, including using advanced computer simulations for mold design and conducting rigorous inspections on the finished products. These measures help to minimize defects such as porosity, miscasting, and surface imperfections, which can adversely affect the performance of the components.
Another significant aspect of sand casting foundries is their environmental impact. Traditional sand casting can generate substantial waste, both in terms of used sand and metal. As industries become more conscious of their environmental footprint, many foundries are adopting sustainable practices, including recycling sand and employing cleaner technologies.
In conclusion, sand casting foundries play a vital role in the manufacturing landscape, offering flexibility and efficiency in producing metal components. With ongoing advancements in technology and a growing emphasis on sustainability, the future of sand casting looks promising. As industries continue to evolve, sand casting foundries will undoubtedly adapt, ensuring their relevance in modern manufacturing.
Post time:វិច្ឆិកា . 17, 2024 12:36
Next:foundry casting sand