The Importance and Applications of Sand Casting Components
Sand casting is one of the oldest and most versatile manufacturing processes utilized for producing metal components. It involves creating molds from sand, into which molten metal is poured to form a solid shape upon cooling. This technique is characterized by its adaptability to various metal alloys and its ability to produce complex geometries. In this article, we will delve into the significance of sand casting components, their production process, and various applications.
At the heart of sand casting lies the mold, typically made of a mixture of sand, clay, and water. The mold is created by compacting the sand around a pattern that mirrors the desired component's shape. After the pattern is removed, the two halves of the mold are joined together, ready to receive molten metal. This method allows for the easy creation of intricate designs that would be difficult to achieve with other casting techniques.
The Importance and Applications of Sand Casting Components
Furthermore, sand casting is highly adaptable. It can accommodate various materials, including iron, steel, aluminum, and bronze. This versatility allows engineers to select metals based on the specific requirements of the component, such as strength, weight, and resistance to corrosion. As a result, sand casting is widely used in various industries, including automotive, aerospace, and machinery.
sand casting components
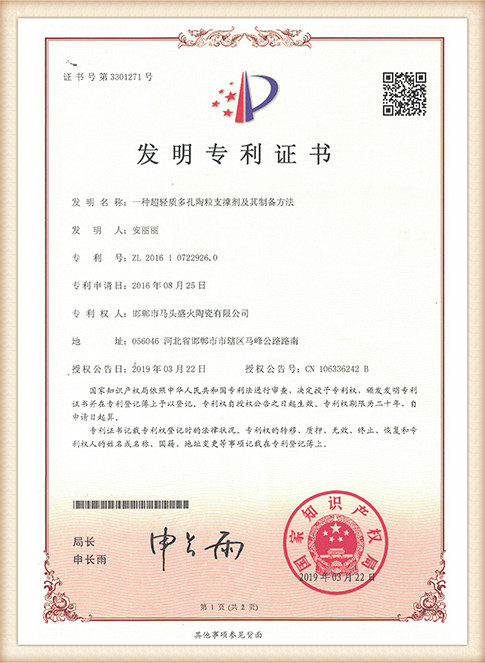
In automotive manufacturing, for instance, sand casting is employed to produce critical components like engine blocks, cylinder heads, and housings. These parts require exact tolerances and robust material properties to ensure performance and reliability. The ability to create complex shapes means that designs can often be optimized for weight and strength, leading to improved fuel efficiency and overall vehicle performance.
In the aerospace sector, sand casting is utilized for the production of parts that endure high levels of stress and extreme temperatures. Components such as turbine housings and structural frames are often cast using this method due to the need for high precision and material integrity. Additionally, the ability to handle large components makes sand casting an invaluable process in this highly specialized field.
Another area where sand casting shines is in the creation of machine components. Gear housings, brackets, and custom-made parts can all be efficiently produced using sand casting techniques. The process allows for rapid turnaround times and the ability to adapt designs even at late stages in development, which is crucial in fast-paced manufacturing environments.
In conclusion, sand casting remains a vital process in the production of components across various industries. Its cost-effectiveness, adaptability to different metals, and capability to produce intricate designs make it a preferred method for engineers and manufacturers alike. As technology advances, the sand casting process continues to evolve, integrating new techniques and materials that enhance its efficiency and effectiveness, ensuring its relevance in the manufacturing landscape for years to come.
Post time:វិច្ឆិកា . 19, 2024 21:03
Next:Exploring the Benefits and Techniques of Sand Casting with Resin for Creative Projects