The Advantages of Sand Casting
Sand casting, a time-honored metal casting process, has been utilized for centuries to create a wide variety of metal parts and components. This method involves the use of a sand mold to shape molten metal, allowing for complex designs and superior detail. The advantages of sand casting are numerous, making it a preferred choice for various industries, from automotive to aerospace and beyond.
One of the primary advantages of sand casting is its versatility in terms of the materials that can be used. This casting method can accommodate a wide range of metals, including aluminum, bronze, iron, and steel. Such versatility allows manufacturers to choose the right material for their specific application, ensuring that strength, precision, and cost-effectiveness are prioritized.
The Advantages of Sand Casting
Cost-effectiveness is a further advantage of sand casting. The materials required for sand casting—primarily sand and a bonding agent—are relatively inexpensive compared to other casting materials. Additionally, the sand used in the process can often be reused multiple times, reducing production costs significantly. This cost efficiency makes sand casting an attractive option for both small-scale manufacturers and large industrial operations.
sand casting advantages
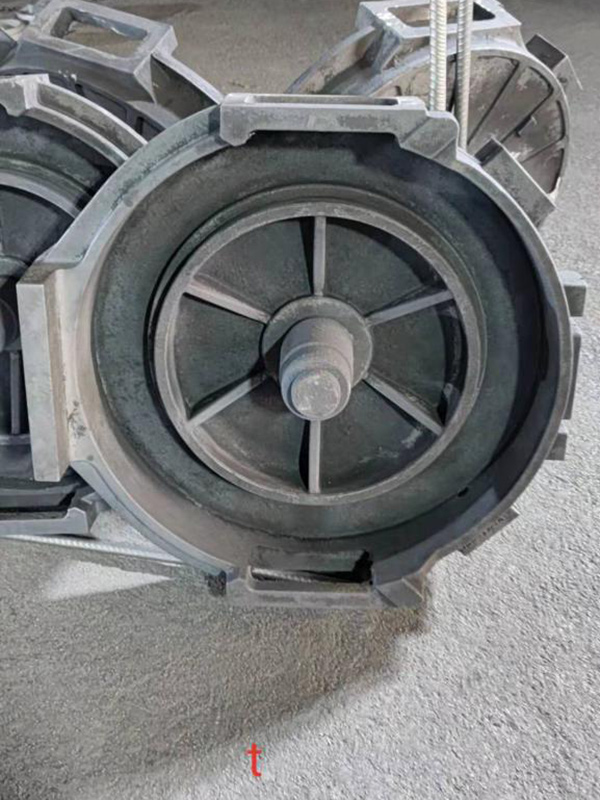
Moreover, sand casting allows for excellent surface finishes and dimensional accuracy. The ability to create highly detailed molds results in castings that often require minimal machining to achieve the desired specifications. This not only speeds up the manufacturing process but also reduces waste and improves overall efficiency.
The process of sand casting is relatively straightforward, adding to its appeal. The basic steps—creating a pattern, building the mold, pouring the metal, and allowing it to cool—are easily understood, making it accessible for smaller manufacturers and hobbyists alike. This simplicity minimizes the need for highly specialized equipment, allowing a broader range of companies to engage in this type of manufacturing.
Environmental considerations also play a role in the advantages of sand casting. Many modern sand casting foundries are adopting more sustainable practices, such as using silica sand and recycling sand materials, which helps reduce their ecological footprint. Compared to some other casting methods, sand casting has a smaller environmental impact when properly managed.
Lastly, the skillset required for sand casting is highly transferable. Workers trained in sand casting techniques can easily adapt their skills to other forms of manufacturing, which helps support workforce development in various industries. This adaptability fosters a knowledgeable workforce capable of navigating the ever-evolving landscape of manufacturing technologies.
In conclusion, sand casting boasts numerous advantages that make it an indispensable process in metal manufacturing. Its flexibility with materials, ability to create complex shapes, cost-effectiveness, excellent surface finishes, straightforward process, environmental advantages, and transferable skills make it a favored choice. As industries continue to innovate and evolve, sand casting will undoubtedly remain a vital part of the manufacturing landscape. Whether for large-scale production or bespoke components, the advantages of sand casting will continue to drive its relevance and utilization in the modern world.
Post time:វិច្ឆិកា . 19, 2024 09:04
Next:Techniques for Smoothing Small 3D Prints Efficiently and Effectively