The Sand Casting Industry A Comprehensive Overview
Sand casting, one of the oldest and most versatile metal casting processes, has cemented its place in various industries, from automotive to aerospace. This method involves creating a mold from sand to hold molten metal, allowing for the formation of complex shapes and designs. As industries evolve and demand for high-quality castings increases, understanding the intricacies of sand casting becomes essential.
The Sand Casting Process
The sand casting process begins with the creation of a mold made from a mixture of sand, clay, and water. The binding properties of the clay, alongside the sand grain structure, allow for the creation of strong molds that can withstand the extreme temperatures of molten metal. There are two primary types of sand used in sand casting green sand and resin-bonded sand. Green sand is a mixture of sand, clay, and water, while resin-bonded sand uses synthetic resins as a binder, offering improved surface finish and dimensional accuracy.
Once the mold is prepared, a pattern (usually made from metal, plastic, or wood) is placed within the sand to form the cavity where the molten metal will be poured. After the pattern is removed, the sand mold is assembled, ensuring that it is tight and secure to prevent leakage during the pouring process. When the mold is ready, molten metal is poured into the cavity, filling it completely. After the metal cools and solidifies, the mold is broken apart to retrieve the cast part, which may require additional finishing processes.
Applications of Sand Casting
The versatility of sand casting allows for its application across numerous industries. In the automotive sector, components such as engine blocks, transmission housings, and brackets are commonly produced using sand casting. This method enables the production of complex shapes and large parts that are crucial for vehicle functionality.
The aerospace industry also benefits from sand casting, particularly for components that require high strength-to-weight ratios, such as turbine housings and various structural parts. These components must meet stringent safety and performance standards, making quality control and process precision paramount.
Moreover, sand casting plays a significant role in the manufacturing of machinery parts, plumbing fixtures, and even artistic sculptures. The ability to produce both small batches and large volumes of cast parts makes it appealing to manufacturers catering to diverse demands.
sand cast industries
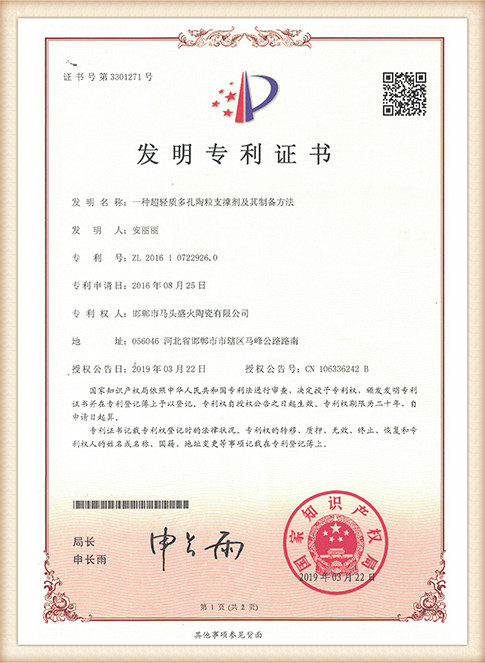
Advantages of Sand Casting
One of the primary advantages of sand casting is its cost-effectiveness. The materials used are relatively inexpensive, and the molds can be produced quickly, reducing lead times for production. Additionally, sand casting allows for a high degree of design flexibility, enabling manufacturers to create intricate designs that may be challenging to achieve using other casting methods.
Another notable benefit is the capability to cast a broad range of metals, including iron, steel, aluminum, and bronze, making sand casting a staple in various manufacturing processes. This adaptability allows companies to tailor their production to meet specific market needs.
Challenges in the Sand Casting Industry
Despite its many advantages, the sand casting industry faces several challenges. One significant issue is the variability in the quality of the final casting, which can result from inconsistencies in the sand mixture, the mold making process, and the pouring method. Manufacturers must continually invest in quality control measures to ensure that cast parts meet required specifications.
Environmental concerns are also prevalent in the sand casting industry. The disposal of used sand and the emissions generated during the casting process are issues that need addressing. Many companies are now exploring sustainable practices, such as recycling used sand and reducing emissions through advanced technologies.
Conclusion
The sand casting industry remains a vital component of modern manufacturing, offering a unique blend of cost-effectiveness, versatility, and design flexibility. As technology advances, so too will the techniques and practices surrounding sand casting, allowing it to continue thriving in an ever-evolving industrial landscape. The continued adaptation to market demands and environmental responsibilities will define the future of this enduring manufacturing process.
Post time:តុលា . 18, 2024 08:34
Next:ပျောက်သွားခဲ့တဲ့ ပရိုဂရမ်တွေပါ။