Sand Printing Casting Revolutionizing Manufacturing Processes
In the realm of industrial manufacturing, sand casting has long served as a fundamental technique for producing metal parts, thanks to its versatility and cost-effectiveness. However, advancements in technology have propelled the traditional sand casting method into the modern age with the advent of sand printing casting, a process that integrates 3D printing into sand casting to create more intricate and precise components.
The Basics of Sand Casting
Traditionally, sand casting involves creating a mold from a mixture of sand and a binding agent. Once the mold is prepared, molten metal is poured into it and allowed to cool and solidify, resulting in a solid metal part. This method is adept at creating large and complex shapes, making it a preferred technique in industries such as automotive and aerospace.
However, conventional sand casting has its limitations. The process can be time-consuming, and creating complex geometries requires additional time and resources. Moreover, the quality of the mold largely determines the quality of the cast part, and achieving high precision can be a challenge.
Enter Sand Printing Casting
The integration of 3D printing technology into sand casting has emerged as a game changer. Sand printing casting leverages additive manufacturing techniques to fabricate sand molds directly from digital designs. This process allows for the creation of highly detailed and intricate parts that were previously difficult or impossible to produce with traditional methods.
sand printing casting
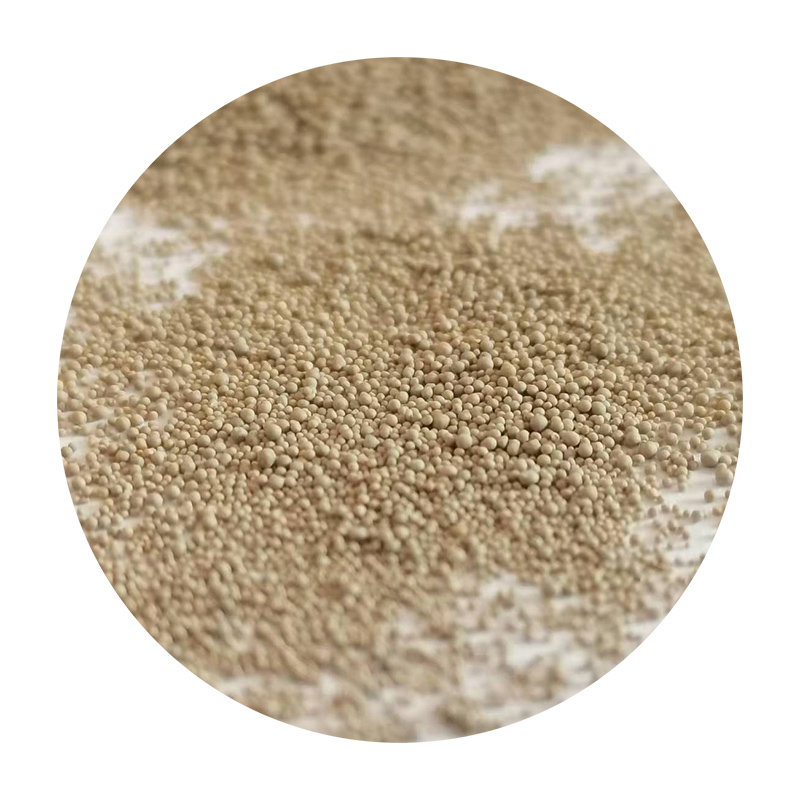
One of the key advantages of sand printing casting is the drastic reduction in lead time. Traditional molds can take days to weeks to manufacture, but with sand printing, molds can be created in a matter of hours. This speed not only accelerates the overall production process but also facilitates rapid prototyping, enabling engineers and designers to iterate quickly on their designs.
Cost-Effectiveness and Sustainability
Cost considerations are paramount in manufacturing, and sand printing casting presents a unique blend of affordability and efficiency. By reducing material waste—since only the necessary amounts of sand are used—this technology becomes more economically viable. Additionally, the ability to create molds without the need for expensive tooling reduces upfront costs, making it more accessible for small businesses and startups.
Sustainability is also a key aspect of sand printing casting. The materials used in sand printing can often be recycled, contributing to a circular economy within the manufacturing industry. Moreover, the reduced energy consumption associated with faster production times aligns well with increasing environmental regulations and sustainability goals.
Future Implications
As technology continues to evolve, the future of sand printing casting appears promising. With the ongoing development of advanced materials and improved printing techniques, we can expect to see even greater precision and capability in the production of complex components. Industries that rely on custom and low-volume production will greatly benefit from this innovative approach.
In conclusion, sand printing casting represents a significant leap forward in the world of manufacturing. By merging the traditional methods of sand casting with modern 3D printing technologies, this process not only enhances efficiency and precision but also promotes sustainability within the industry. As manufacturers continue to explore and adopt this technology, we might witness a new era of production that embraces both innovation and environmental responsibility.
Post time:កញ្ញា . 07, 2024 21:16
Next:Examples of Sand Casting Products