Sand Casting Metal Process An Overview
Sand casting, one of the oldest and most versatile metal forming techniques, is widely used in manufacturing complex metal parts
. This process involves creating a mold from a sand mixture and using it to pour molten metal, allowing for the production of intricate shapes and designs.The sand casting process begins with the creation of a pattern, typically made from a material that is easy to shape, such as wood, metal, or plastic. This pattern is a replica of the final product and is essential for forming the mold. Once the pattern is ready, it is placed in a sand mixture, which consists of sand, clay, and water. This mixture is compacted around the pattern to create the two halves of the mold.
After the mold is formed, it is carefully removed from the pattern. The next step involves assembling the two halves of the mold, ensuring they fit snugly together. This step can also include adding any cores if hollow sections are required in the casting. Cores are additional pieces made from sand that create internal cavities within the final product.
The prepared mold is then heated to remove moisture, which can cause defects in the final casting. Once the mold reaches the desired temperature, molten metal, typically aluminum, iron, or bronze, is poured into it. The metal is heated to a liquid state and poured through channels designed to guide it into the mold cavity. It is essential to pour the metal at the appropriate temperature and speed to prevent defects such as cold shuts or misruns.
sand casting metal process
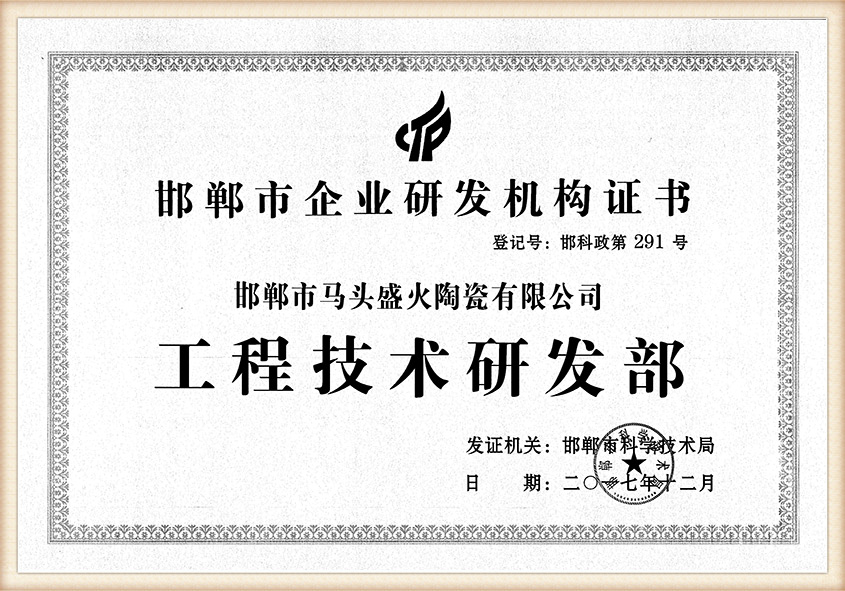
After the molten metal cools and solidifies, the next step is demolding. The sand mold is broken away to reveal the casting, which often retains sand particles. Cleaning processes, including sand blasting or grinding, are used to remove the sand and any surface imperfections.
One of the primary advantages of sand casting is its adaptability. It can accommodate a variety of metals and alloys, and it is particularly effective for producing larger components that may not be feasible with other casting methods. Moreover, the cost of producing sand molds is relatively low, making it an economical choice for both low and high production runs.
Despite its advantages, sand casting does have limitations. The surface finish and dimensional accuracy are generally inferior compared to other casting methods, such as investment casting. However, with modern advancements in materials and techniques, many of these limitations are being addressed.
In conclusion, sand casting is a timeless manufacturing process that continues to be invaluable in producing complex metal parts. Its unique combination of adaptability, cost-effectiveness, and capability to create intricate designs makes it an essential process in various industries, including automotive, aerospace, and machinery.
Post time:កញ្ញា . 05, 2024 13:40
Next:Sanding 3D Printed Parts - Achieve a Smooth Finish