Understanding Sand Casting Costs
Sand casting is a widely utilized manufacturing process that involves creating metal components by pouring molten metal into a sand mold. This method is favored for its versatility, low cost, and ability to produce complex shapes. However, understanding the costs associated with sand casting is crucial for manufacturers, engineers, and businesses that rely on this technique.
Initial Setup Costs
The initial costs of sand casting largely pertain to the design and creation of the molds. Sand molds must be crafted to match the intended design of the component, which often requires investment in pattern making. Patterns can be made from a variety of materials, including metals or plastics, and the choice will significantly impact costs. Depending on the complexity of the component, pattern costs can range from a few hundred to several thousand dollars.
Material Costs
The type of sand used in the casting process also affects overall costs. Commonly, silica sand is employed due to its availability and affordability. However, the quality of sand affects the final product's surface finish and dimensional accuracy. Higher quality sands may incur additional costs, and reclaiming sand from the casting process—while it can save costs in the long run—requires additional infrastructure and handling, further influencing the overall financial outlay.
Labor Costs
sand casting cost
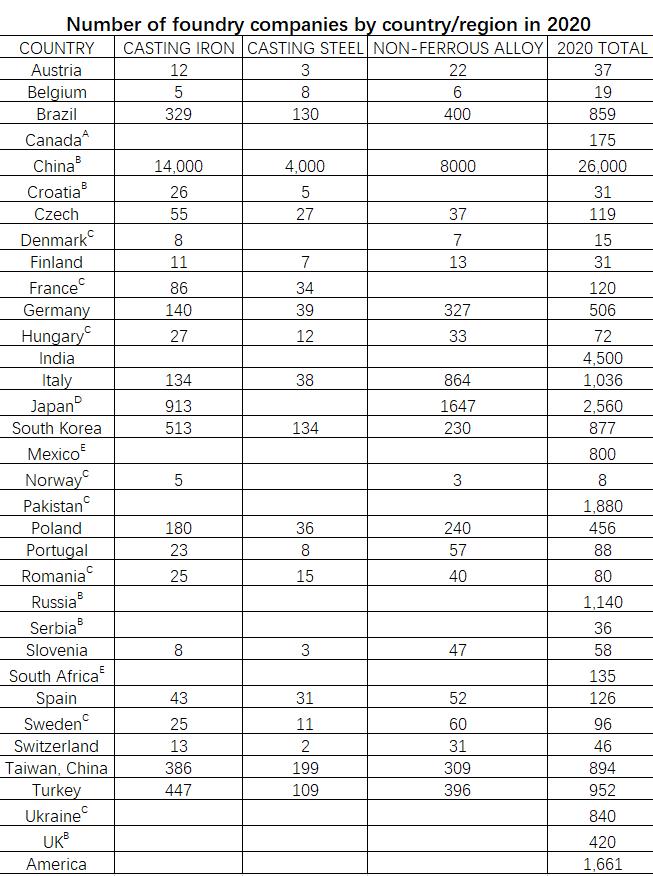
Labor plays a significant role in the cost of sand casting. Skilled workers are required to manage the intricate processes of mold making, melting metal, and finishing the cast product. In areas with higher labor costs, manufacturers need to account for these expenses when budgeting for sand casting projects. Additionally, training costs for new employees to ensure a consistent and quality production process can add to the initial outlay.
Production Volume Impact
The scale of production impacts the unit cost of sand casting significantly. For low-volume production runs, such as prototypes or custom pieces, costs can be disproportionately high due to the setup required for each cast. Conversely, high-volume productions can capitalize on economies of scale, driving down the cost per unit dramatically as fixed costs are distributed over a larger quantity of items.
Post-Casting Operations
After casting, additional operations such as machining, surface finishing, and quality inspection can incur further costs. These processes are often necessary to meet stringent specifications, especially in industries like aerospace and automotive where precision is critical. Each of these post-casting operations requires time and resources, ultimately impacting the total cost of the cast components.
Conclusion
In summary, the costs associated with sand casting are multifaceted, involving initial setup, material, labor, production volume, and post-casting operations. Understanding these cost components is essential for manufacturers looking to optimize their production processes and manage budgets effectively. By evaluating each aspect of sand casting costs, businesses can make informed decisions that enhance productivity while maintaining quality standards.
Post time:កញ្ញា . 19, 2024 16:45
Next:low pressure sand casting