Sand casting is a widely used metal casting process that has been around for centuries. This technique allows for the creation of complex shapes and sizes, making it a favorite choice in various industries, from automotive to aerospace. Central to this process is the selection of the right alloy, which plays a pivotal role in determining the final product's properties.
Alloys used in sand casting can be broadly categorized into ferrous and non-ferrous alloys. Ferrous alloys, primarily based on iron, include cast iron and cast steel, while non-ferrous alloys comprise metals like aluminum, copper, magnesium, and zinc.
Ferrous Alloys
Cast iron is one of the most popular ferrous alloys used in sand casting. It has excellent fluidity, allowing it to fill intricate mold designs. Cast iron is also known for its high wear resistance and ability to dampen vibrations, making it ideal for engine blocks and machine bases. Various grades of cast iron can be produced, including gray cast iron, ductile iron, and white cast iron, each offering distinct mechanical properties tailored to specific applications.
Cast steel, albeit less common than cast iron, is another ferrous option. It typically consists of a lower carbon content, resulting in improved ductility and toughness. Cast steel is often used for components requiring high strength and impact resistance, such as gears and frames for heavy machinery.
Non-Ferrous Alloys
sand casting alloys
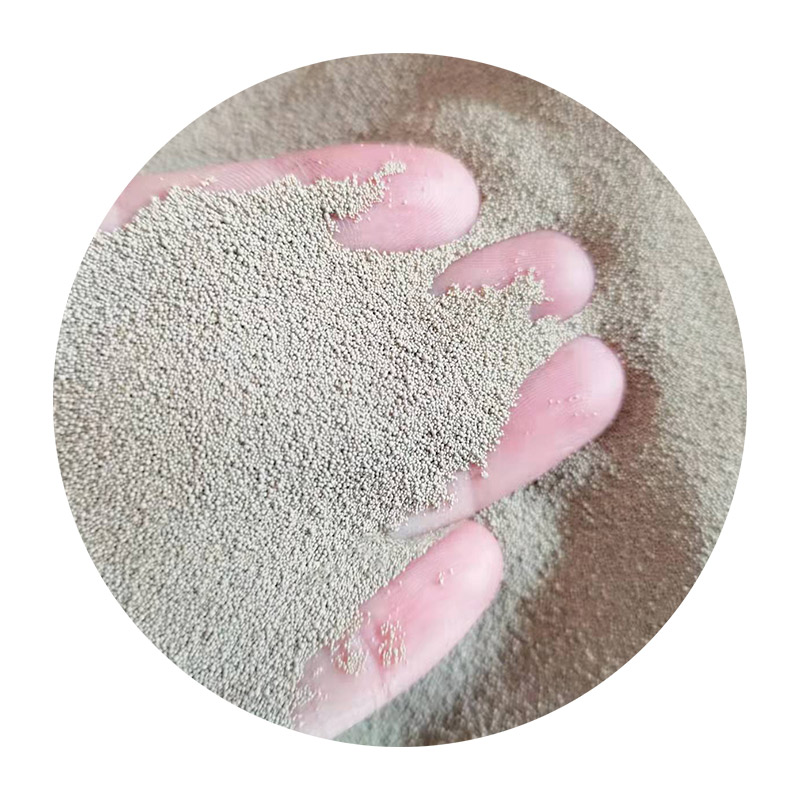
Aluminum alloys are among the most versatile non-ferrous materials used in sand casting. They are lightweight, corrosion-resistant, and possess excellent thermal and electrical conductivity. Aluminum castings are commonly found in industries like aerospace, where weight reduction is crucial, and automotive, where fuel efficiency is enhanced through lightweight components. Popular aluminum alloys used include A356 and A380, each designed for specific performance characteristics such as strength or fluidity.
Copper alloys, particularly bronze and brass, are also notable in sand casting. Bronze, consisting mainly of copper and tin, is valued for its corrosion resistance and strength, making it a preferred choice for marine applications. Brass, on the other hand, is primarily copper and zinc and is known for its excellent machinability and aesthetic appeal, often used in decorative applications and fittings.
Magnesium alloys are emerging in the casting arena due to their superior strength-to-weight ratio. These alloys are typically used in automotive applications and aerospace parts, where reducing weight without sacrificing strength is a primary concern.
Conclusion
The choice of alloy in sand casting is critical to the success of the final product. The properties required for the application will dictate whether a ferrous or non-ferrous alloy is appropriate. As industries continue to evolve, the development of new alloys and improved casting techniques will enable the production of even more complex and high-performance components. Ultimately, understanding the unique characteristics and advantages of various alloys will empower engineers and designers to make informed decisions that enhance the functionality and efficiency of their products.
Post time:សីហា . 30, 2024 22:30
Next:sand for casting