The Resin-Coated Sand Process An Overview
The resin-coated sand process is a significant advancement in the field of metal casting, particularly useful in producing high-quality castings with improved dimensional accuracy and surface finish. This method has gained prominence due to the rising demand for precision components in industries such as automotive, aerospace, and industrial machinery.
What is Resin-Coated Sand?
Resin-coated sand consists of sand grains that are coated with a thermosetting resin. These resins, typically phenolic or epoxy-based, create a strong binding matrix when heated. The process begins with selecting high-quality silica sand, which is then treated with a specific resin and catalyst mixture. This coating allows the sand to retain its shape during the casting process yet is still capable of being removed easily to reveal the final casting.
The Process of Producing Resin-Coated Sand
1. Preparation of Sand The process starts with the raw silica sand. The sand is cleaned and graded to achieve the desired particle size distribution, which is crucial for achieving uniformity in the final product.
2. Coating The next step involves mixing the cleaned sand with resin and a catalyst. The quantity and type of resin used are critical as they influence the properties of the sand. The mixture is typically carried out in a hot mixer, which provides the necessary heat to initiate the resin bonding process.
3. Curing Once the sand is coated, it is cured through a process that usually involves further heating. The heat causes the resin to harden and create a chemical bond with the sand particles. This results in a stable mold that can withstand the molten metal during the casting process.
resin coated sand process
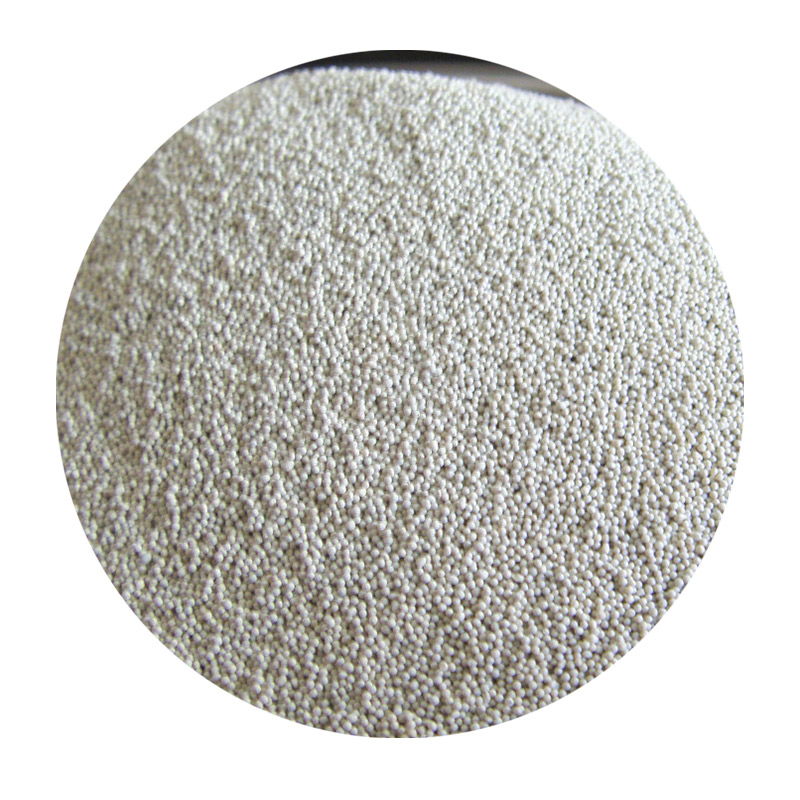
4. Molding and Casting The resin-coated sand is then shaped into molds using various techniques, such as the shell mold process or traditional sand casting. The high strength of the coated sand allows for the production of intricate designs with fine details. After the molds are crafted, molten metal is poured into them to create the final casting.
5. Demolding and Finishing Once the metal has cooled and solidified, the mold can be easily removed. The sand's ability to break down allows for a clean separation, minimizing the need for extensive finishing work. This results in castings with superior surface finishes and reduced post-processing costs.
Advantages of the Resin-Coated Sand Process
One of the main advantages of the resin-coated sand process is the improved quality of the castings. The process allows for tighter tolerances and enhanced surface finishes compared to traditional sand casting methods. The addition of resin provides better resistance to deformation, ensuring shape retention during the pouring of molten metal.
Moreover, the process is more environmentally friendly as it reduces the amount of binder needed, and the sand can often be reused multiple times, providing substantial cost savings over time.
Conclusion
The resin-coated sand process represents a paradigm shift in casting technology. As industries increasingly demand high-precision components, the benefits offered by this method—such as improved quality, reduced waste, and enhanced efficiency—make it an attractive choice for manufacturers. As technology continues to advance, we can expect further innovations in resin-coated sand processes, paving the way for even greater possibilities in metal casting. With its myriad advantages, the resin-coated sand process is likely to remain a fundamental technique in modern foundries, meeting the evolving needs of various industries around the globe.
Post time:វិច្ឆិកា . 24, 2024 17:03
Next:The Advantages of Sand Casting in Manufacturing Processes