Rapid Sand Casting Innovations in Efficiency and Quality
In the realm of manufacturing, the need for efficiency and quality has never been more pressing. One innovative method that has gained traction in recent years is rapid sand casting. This technique combines traditional sand casting methods with modern technologies to significantly enhance the speed and precision of metal casting processes. As industries increasingly demand rapid production without sacrificing quality, rapid sand casting has emerged as a pivotal solution.
Understanding Rapid Sand Casting
Traditional sand casting involves the creation of a mold using sand, where a liquid metal is poured to form parts. While effective, this method can be time-consuming and may lead to variability in the final product. Rapid sand casting, however, streamlines this process. By utilizing advanced techniques such as 3D printing and improved sand technologies, manufacturers can create molds more quickly and with greater accuracy. This transformation not only reduces production time but also allows for the production of complex and intricate designs that were previously difficult to achieve.
Advantages of Rapid Sand Casting
One of the most significant advantages of rapid sand casting is the reduction in lead time. Traditional sand casting can take days or even weeks to produce a mold, particularly for complex designs. In contrast, rapid sand casting can produce these molds within hours. This accelerated timeline is vital in today’s fast-paced market, where companies must respond quickly to customer demands and changing market conditions.
Additionally, rapid sand casting allows for enhanced design freedom. With the aid of 3D printing technologies, designers can create molds with intricate geometries that optimize material usage and performance. This capability results in lighter, stronger components, which is especially beneficial in industries such as aerospace and automotive, where weight reduction is critical.
rapid sand casting
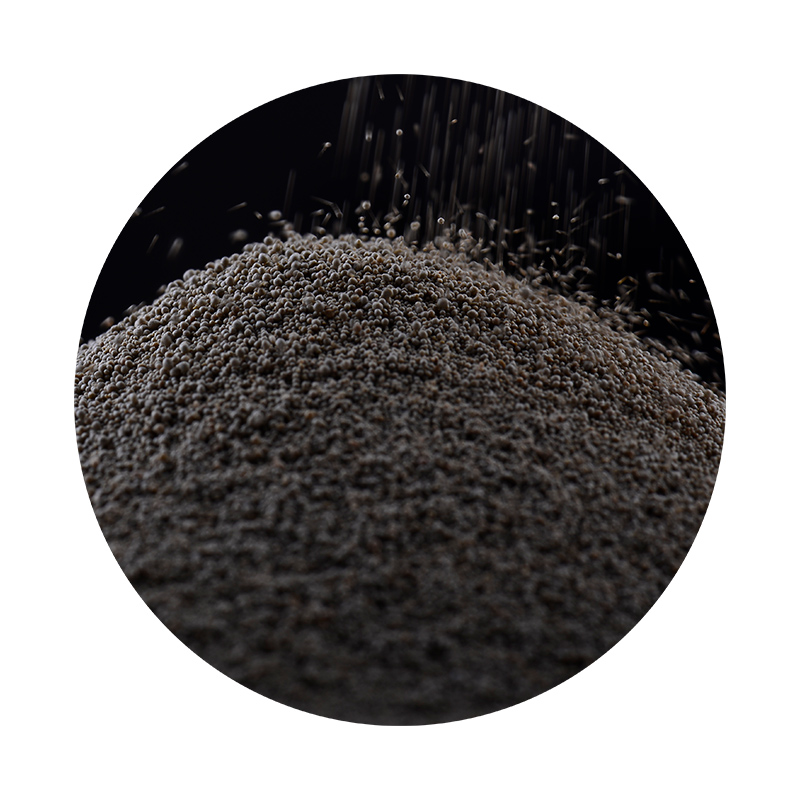
Another notable advantage is the consistency and quality of the final products. Traditional sand casting can sometimes produce defects such as porosity or surface imperfections. Rapid sand casting mitigates these issues through precise control over the mold-making process and the ability to fine-tune parameters in real-time. This quality assurance is crucial for industries requiring stringent adherence to specifications and standards.
Applications Across Industries
The applications of rapid sand casting are vast and varied. In the automotive industry, for instance, manufacturers are utilizing this method to produce engine blocks, transmission cases, and intricate components that meet the demanding performance standards of modern vehicles. The aerospace sector also benefits significantly, where lightweight and high-strength parts are essential for fuel efficiency and overall performance.
Moreover, rapid sand casting serves the medical device industry, where custom and precise components are often required. Using this method, manufacturers can produce specialized surgical instruments and implants tailored to specific patient needs, enhancing both the safety and effectiveness of medical procedures.
Future Prospects
As technology continues to advance, the future of rapid sand casting looks promising. Ongoing research into new materials and processes is likely to lead to even greater efficiencies and capabilities. The integration of automated systems and artificial intelligence into the sand casting process may further enhance production speed and consistency, allowing manufacturers to stay competitive in a global market.
In conclusion, rapid sand casting represents a significant leap forward in the field of metal manufacturing. By combining traditional methods with cutting-edge technology, it provides a solution for the increasing demand for efficient and high-quality production. With continued innovation and application across various industries, rapid sand casting is poised to play a crucial role in shaping the future of manufacturing.
Post time:ធ្នូ . 25, 2024 17:54
Next:different types of foundry sand