Precision Sand Casting A Key Process in Modern Manufacturing
Precision sand casting is a manufacturing process that has stood the test of time, combining ancient techniques with modern innovations to meet the demands of various industries. This method is known for its versatility and cost-effectiveness, making it an essential choice for producing complex metal parts with high accuracy.
What is Precision Sand Casting?
Precision sand casting involves creating a mold from fine sand mixed with a binder material, typically clay or resin. This mixture is shaped around a pattern, which represents the final dimensions of the part. Once the mold is created, molten metal is poured into it, allowing it to cool and solidify. After cooling, the mold is broken away, revealing the cast part.
The term precision in precision sand casting refers to the high level of dimensional accuracy that can be achieved during this process. Fine sand allows for intricate detailing, while modern techniques help minimize defects and produce consistent results.
Advantages of Precision Sand Casting
1. Cost-Effective Precision sand casting is particularly advantageous for producing large quantities of parts. The initial investment in mold creation can be high, but the cost per unit decreases significantly with mass production.
2. Material Versatility This process can accommodate a variety of metals, including aluminum, iron, and bronze. Each material has unique properties, allowing manufacturers to choose the best one for their specific application.
3. Complex Geometries The ability to produce complex shapes with intricate details is a hallmark of precision sand casting. This feature is especially valuable in industries such as aerospace, automotive, and energy, where precise components are critical for performance and safety.
precision sand casting
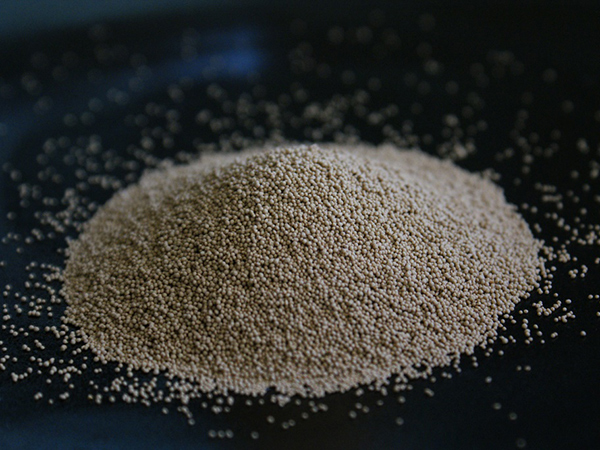
4. Sustainability The sand used in the casting process can often be reused, reducing waste and making it an environmentally friendly option compared to other casting methods.
Applications in Various Industries
Precision sand casting is employed across a broad spectrum of industries. In the aerospace sector, components such as engine mounts and landing gear are produced using this method due to the high strength-to-weight ratio that precision sand casting provides. The automotive industry relies on it for parts like engine blocks and transmission housings, where both precision and durability are paramount.
In addition to transport, the construction industry benefits from precision sand casting for creating components such as brackets, fittings, and fixtures. Even the energy sector sees applications in wind turbines and power generation equipment, where precision components are essential for efficiency and safety.
Technological Innovations
Modern advancements in technology have enhanced the precision sand casting process. Computer-aided design (CAD) software is now commonly used for creating accurate patterns and simulations, reducing the likelihood of errors before the actual production begins. Moreover, advancements in 3D printing have also begun to influence sand casting by allowing for the rapid creation of molds and patterns, thereby increasing efficiency and reducing lead times.
Conclusion
Precision sand casting is an integral part of modern manufacturing, offering a unique combination of cost-effectiveness, material versatility, and the ability to create complex geometries. As industries continue to evolve and demand more precise components, this time-tested technique is likely to remain a cornerstone of manufacturing processes. With ongoing innovations in technology, the future of precision sand casting looks promising, poised to adapt and thrive in a rapidly changing industrial landscape. As manufacturers embrace these advancements, they can continue to produce high-quality, precision-engineered components that meet the ever-increasing demands of the market.
Post time:តុលា . 22, 2024 10:35
Next:golden sands prices